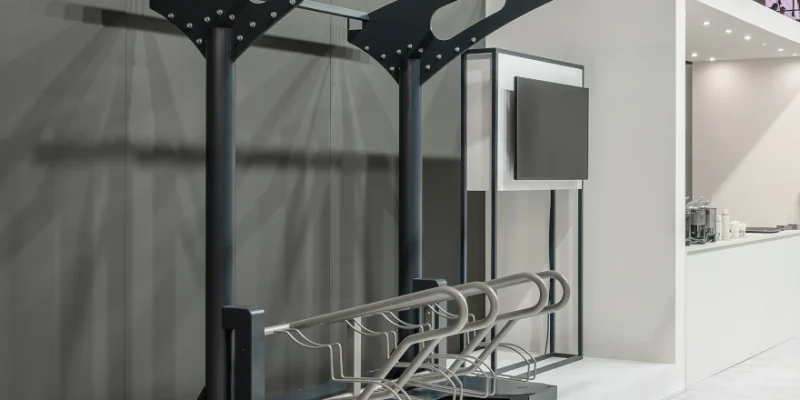
In this article, a BLM Group practical case study was examined to illustrate how the adoption of Lasertube, tube benders and wire benders, along with related programming and integration software, saved time and reduced material consumption in the construction of a bicycle shelter.
This project demonstrates how contractors and designers can benefit from these modern tube and wire processing systems to make the fabrication of structures and tubular frames more efficient. The main steps carried out during the design and production process:
- Project description and design features of the bike shelter
- Simplifying connections through the use of joints and bend cuts
- Replacement of complex elements made of sheet metal cut, bent and welded together, with simpler tubular elements
- Laser cutting and bending to reduce material consumption
- An optimized process thanks to BLM GROUP’s production management MES
1. Project description and design features of the bike shelter
The shelter is an outdoor urban structure designed for bicycle parking. The frame is made of tubes of different diameters, metal wire and sheet metal.
3D model of the bike shelter before re-engineering.
Under normal conditions, the expected lead time for this structure, using conventional manufacturing technologies, ranges from 6 to 8 weeks, 2 days of which are required for component assembly.
This prolonged assembly phase is mainly attributable to the use of numerous welding jigs. Indeed, the parts must be prepared, carefully placed, and then welded by experienced personnel.
Regardless of the operator’s experience, due to the complexity of the structure, the degree of precision in the final assembly remains limited.
The use of BLM GROUP’s Lasertube, tube bending machines and wire bending machines has made it possible to simplify the entire production process through the complete re-engineering of the product and the optimal management of the entire production.
The result is a 50% reduction in manpower, 52% reduction in production time, 26% reduction in production costs and 20% reduction in material costs.
Detailed picture of savings post re-engineering of the bike shelter.
2. Simplifying connections through the use of joints and bend cuts.
The use of joints, pass through holes, hooks and cut and bend parts are an effective approach to simplify the construction of the frame.
These types of connections ensure precise positioning of the components, thus facilitating assembly and welding and improving the precision of the entire structure.
In this project, laser cutting of the tube made it possible to create joints in an extremely precise, simple and practical way.
A fundamental role has been played by ArTube,the Lasertube programming software, which offers a wide library of joints and connections ready to be applied parametrically in the CAD model of the part to be produced.
3. Replacement of complex elements made of sheet metal cut, bent and welded together, with simpler tubular elements.
In the initial design, the rack support elements were composed of cut, bent and welded sheets.
Their creation required the use of three different machines: a sheet metal cutting system ( laser or other), press brake and a welding machine.
Thanks to Lasertube systems, these elements have been replaced by a single component obtained from a tube with a rectangular section laser cut and bent.
Instead of the three machines mentioned above, it was sufficient to use a single Lasertube system.
In addition, the introduction of two simple dots allowed precise positioning during assembly, simplifying the subsequent welding of the component to the roof support pylon.
Rack support element before and after the introduction of Lasertube technology.
4. Laser cutting and bending to reduce material consumption
Slots and teeth also played a crucial role in the construction of the rack.
The transverse support tube has been equipped with holes and slots necessary to accommodate the bent tubes and rods that support the bikes.
This solution has not only simplified the assembly and welding of components but has also saved material by reducing the length of the rods.
However, the reduction in material consumption is not only the result of a general lightening of the structure, resulting from the re-engineering, but also from the use of All-In-One technology which, by adapting the position of the cutting geometries to compensate for the deformation effects of tube bending, has eliminated waste and enabled laser cut and bent tube parts right from the start.
5. An optimized process thanks to BLM GROUP’s production management MES
CAD/CAM design software (ArTube for Lasertube and VGPNext for tube bending machines and wire bending machines) played an essential role in product re-engineering, from importing 3D models, optimizing components to creating part programs for laser cutting and bending systems.
Through the BLM GROUP Manufacturing Execution System (MES), the entire production cycle was managed in an integrated and flexible way: transferring production orders to the involved machines, planning activities with evidence of precise processing times, assigning execution priorities and specifying the involved materials.
The clear and intuitive exposure of data makes it possible to streamline processes by reducing design times, eliminating material waste, and minimizing inefficiencies.
A rigorous scheduling of orders and the exact estimation of production times have allowed quick estimation of the entire project starting from the 3D assembly of the product, while the real-time control of the machines has allowed for consistent high production performance and prompt intervention in cases of downtime.