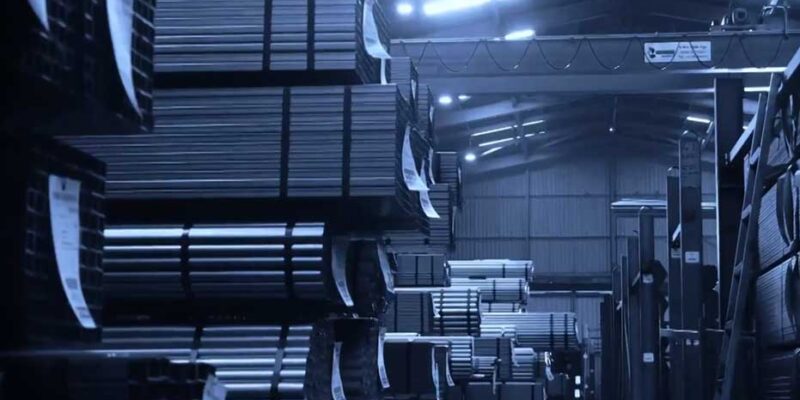

The process begins with continuous cold-forming of a steel strip from coil into a longitudinal cylinder. Then, through the application of high-frequency induction currents, the edges are heated up and forged together, culminating in the formation of a high-quality welded tube. This method stands out for its remarkable efficiency, producing tubes that serve a myriad of purposes across various industries – from automotive to construction, horticulture and furniture.
Top Tubes, prides itself on leading the charge in the steel tube manufacturing industry, especially when it comes to Electric Resistance Welding (ERW) tube production. Our depth of knowledge in this area is not just comprehensive; it’s built on a foundation of hands-on experience and a relentless commitment to innovation and environmental stewardship.
But what truly sets ERW technology apart? Its versatility and the environmentally friendly, cost-effective nature of the process. These tubes aren’t just made; they’re engineered to meet precise specifications and high standards of quality and sustainability. In the sprawling landscape of steel manufacturing, ERW Tube Mills shine as a beacon of innovation and environmental consciousness in ERW Tube Manufacture.
What is Significance of ERW Tube Mills?
In the steel manufacturing landscape, ERW Tube Mills stand out as innovative powerhouses. ERW—Electric Resistance Welding—Tube Mills are essentially advanced factories dedicated to producing steel pipes through a process known as electric resistance welding.
Efficiency is the name of the game with ERW Tube Mills. These facilities employ a sophisticated technique to weld steel strips into tubes using high-frequency electrical resistance. The result? Exceptionally high-quality tubes that adhere to strict industry standards, ensuring reliability and durability in various applications.
One of the standout features of ERW Tube Mills is their ability to optimise material use. This approach not only reduces waste but also translates into significant cost savings for manufacturers, making the process economically favourable.
However, the benefits of ERW Tube Mills extend beyond efficiency and cost-effectiveness. These mills boast remarkable versatility, capable of producing tubes in a wide array of shapes and sizes. This adaptability makes them indispensable to diverse sectors, including construction, oil and gas, and water supply, among others.
What are the advantages of ERW tube?
Durability
ERW tubes are built to last. Designed to endure tough conditions, they assure sustained performance over time. This durability is crucial for sectors like construction, automotive, and oil and gas, where longevity and reliability are non-negotiable. Specific surface coatings further enhances corrosion resistance properties and aesthetic appearance.
Cost-Effectiveness and High-Strength
One of the most appealing features of ERW tubes is their balance between affordability and strength. They provide an excellent strength-to-weight ratio, which means they offer robust performance without being excessively heavy or costly. This makes them perfect for demanding applications where durability and budget are both priorities.
Versatility
With ERW tubes available in a plethora of sizes and thicknesses, finding the right fit for specific needs is straightforward. This adaptability is invaluable, allowing for custom solutions across various industries and applications.
Environmental Friendliness
Lastly, the production of ERW tubes places a strong emphasis on sustainability. Made from recyclable materials when sourced from Electric Arc Furnaces , they contribute to environmental conservation, aligning with the growing demand for eco-friendly manufacturing practices.
Ease of Fabrication and Installation
Another significant advantage is the straightforwardness of working with ERW tubes. They can be effortlessly cut to size, shaped, and installed, which translates to savings in both time and labour costs. This ease extends to repairs and maintenance too, as ERW tubes can be quickly replaced or fixed, ensuring minimal downtime.
The Making of an ERW Tube
The journey of an ERW Tube begins with a flat strip of steel, or coil, which is then progressively formed into a cylindrical shape. The magic happens when high-frequency electrical resistance is applied, fusing the steel strip’s edges together. This technique creates a welded tube, known for its uniformity and high quality. It’s a process that combines efficiency with precision, ensuring the end product meets rigorous standards.


