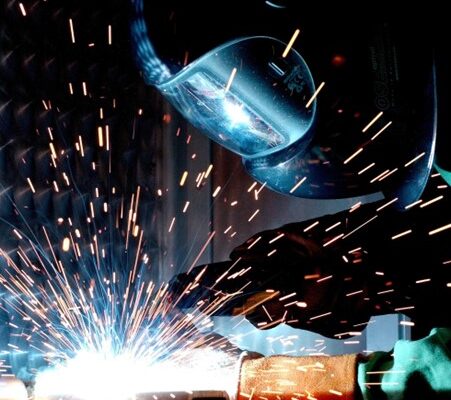
Ensure Quality Welds: Importance of Welding Inspection explained by Saint Anns Sheet Metal Company Limited Company Ltd
Welding is a fundamental process in various industries, playing a vital role in joining metal components together. However, the strength and reliability of welds heavily depend on the quality of the welding process. This is where welding inspection steps in, serving as a critical quality control measure.
Understanding Welding Inspection
Welding inspection is the systematic examination of welds to ensure they meet specified standards and criteria. It involves assessing various aspects of the welding process, including weld appearance, dimensions, strength, and overall integrity. By conducting thorough inspections, potential defects, discontinuities, and deviations can be detected early, mitigating the risk of structural failures, product defects, and safety hazards.
Importance of Welding Inspection
Ensuring Structural Integrity:
Welds form the backbone of many structures, such as bridges, buildings, and pipelines. Welding inspection verifies the integrity of welds, guaranteeing the structural strength and longevity of these critical assets. By identifying flaws or imperfections, prompt corrective actions can be taken to maintain structural integrity and prevent catastrophic failures.
Enhancing Product Quality:
Welding inspection is instrumental in maintaining high-quality standards for welded products. By adhering to established inspection methods and criteria, manufacturers can verify that welds meet or exceed specified requirements. This ensures consistent quality, customer satisfaction, and compliance with industry regulations and standards.
Welding Inspection Methods:
Visual Inspection:
Visual inspection is the most basic and commonly used method for weld assessment. It involves visually examining the welds for surface discontinuities, such as cracks, porosity, and incomplete fusion. Qualified inspectors use specialized tools like magnifiers, borescopes, and cameras to thoroughly evaluate weld appearance and identify any potential defects.
Non-Destructive Testing (NDT):
NDT techniques provide a deeper level of inspection without causing damage to the weld or the base material. Common NDT methods for welding inspection include radiography, ultrasonic testing, magnetic particle testing, and liquid penetrant testing. These techniques enable inspectors to detect internal defects, assess weld soundness, and ensure weld quality.
Criteria for Reliable Weld Assessment
Welding Codes and Standards:
Welding inspection relies on established codes and standards specific to the industry and application. These guidelines define acceptable weld quality criteria, such as weld size, penetration depth, reinforcement, and joint strength. Inspectors compare actual weld characteristics against these criteria to determine compliance and quality.
Acceptance and Rejection Criteria:
Welding inspection sets clear acceptance and rejection criteria for welds. These criteria outline the maximum allowable discontinuities, such as cracks or lack of fusion, to ensure weld quality and safety. Inspectors use specific measurements, visual indicators, or non-destructive testing results to assess whether welds meet these defined criteria.
Conclusion:
Welding inspection is an indispensable process in ensuring the quality, integrity, and safety of welds. By conducting thorough inspections using various methods and adhering to established criteria, manufacturers can uphold the highest standards of weld quality. Whether it’s verifying structural integrity or enhancing product quality, welding inspection plays a vital role in every welding operation. Embrace the significance of welding inspection and harness its power to create reliable and durable welds.