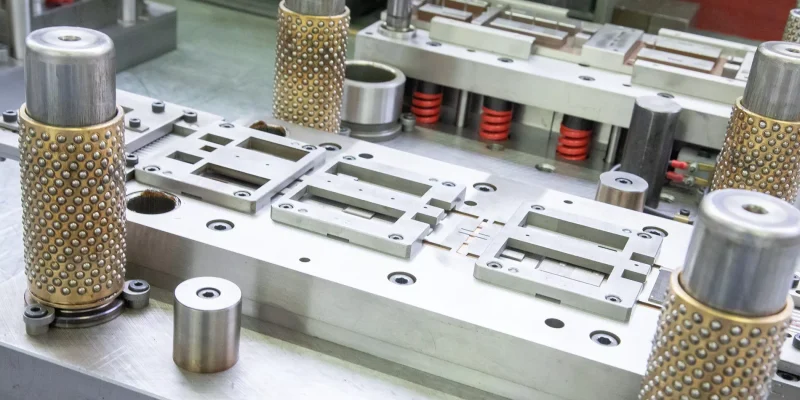
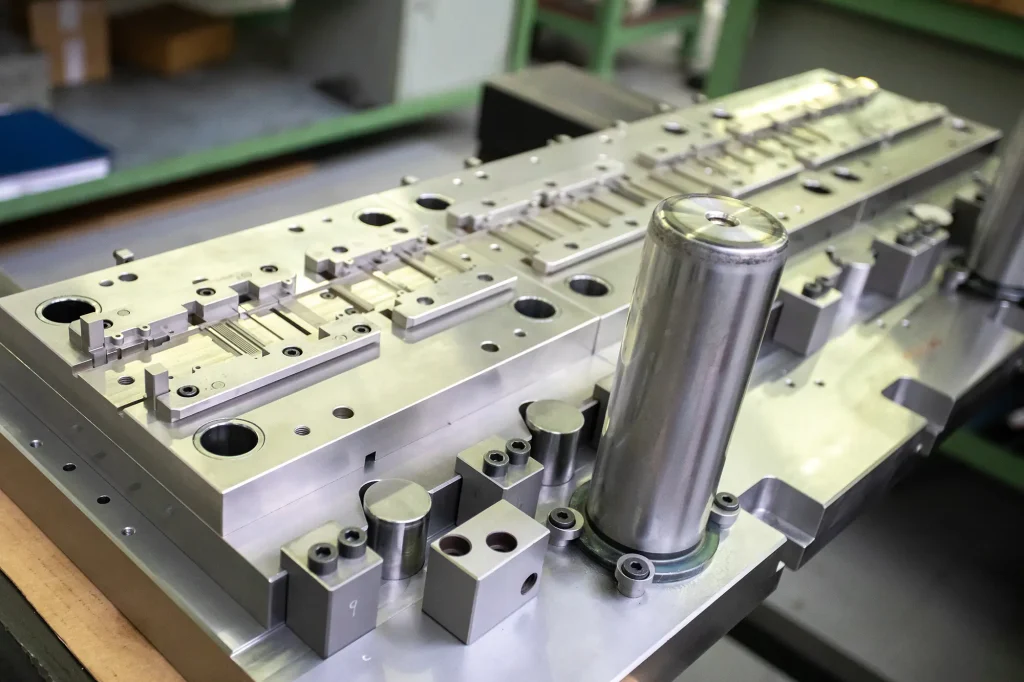
With the precision manufacturing industry evolving day by day, so too do the tools and processes that underpin them. One such critical area is press tooling, a technology that has quietly reformed the way components are produced, from automotive parts to cutting-edge medical devices. As demands for efficiency, quality, and cost-effectiveness continue to rise, advancements in press tooling are paving the way for the next era of manufacturing excellence.
Press tooling is playing a transformative role in global manufacturing, and the exciting future developments shaping this essential field are poised to redefine industry standards. One significant trend is the shift towards modular tooling systems, which provide manufacturers with greater flexibility and adaptability. These systems allow for quicker reconfiguration and upgrades, enabling businesses to respond rapidly to changing market needs without incurring extensive downtime or costs.
Introduction to press tooling: what it is and why it is essential
Press tooling involves the design and development of tools used in the stamping or forming of materials into specific shapes and sizes. This process is critical in industries that demand precision, durability, and cost-effectiveness, as it enables manufacturers to mass-produce high-quality components at scale. Without press tooling, products such as automotive parts, electronic devices, and household appliances would be significantly more expensive to produce, less uniform, and lower in quality.
The precision of press tooling is essential for industries where even the slightest deviation from specifications can lead to product failure or safety hazards. For example, in the automotive industry, detailed laminations are necessary for motors, ensuring that they operate efficiently and reliably. Similarly, in the medical technology sector, surgical instruments and diagnostic equipment require exact measurements and functionality.
Press tooling is also essential for producing consumer electronics including casings, connectors, and internal components with precision to meet functional and quality standards. It also supports renewable energy advancements by manufacturing battery components, and is fundamental in creating motor parts for reconnaissance drones.
Moreover, the advancement of technology in press tooling has led to innovations such as modular tooling systems and automation, which enhance production efficiency and flexibility. These developments enable manufacturers to quickly adapt to changing market demands, reduce lead times, and lower production costs.
As industries continue to evolve, the importance of press tooling will only grow, ensuring that manufacturers can meet the rigorous standards required by the market while maintaining a competitive edge.
How press tooling enhances manufacturing precision
At the heart of precision manufacturing lies the use of cutting-edge press tooling techniques. Precision tooling ensures that components meet tight specifications and are produced with minimal variability, even across millions of units. This consistency is especially vital in industries such as automotive and aerospace, where the tiniest deviation in component specifications could lead to significant product malfunctions or inefficiencies. In these sectors, press tooling acts as a safeguard against potential failures, ensuring that every component performs to the highest standards.
One of the key advantages of modern press tooling is its ability to maintain tight tolerances throughout the manufacturing process. For instance, Brandauer’s micron precision tooling can achieve accuracy to less than 10 microns, which is equivalent to 1/10th of the width of a human hair. By ensuring that components adhere to stringent quality requirements, manufacturers can enhance product performance and reliability, fostering trust among consumers and stakeholders alike.
Moreover, advancements in press tooling have led to significant reductions in tool design time and production costs. Brandauer’s 14-stage process map, for instance, has cut tool design time by an impressive 30% and tooling production costs by 10%. These efficiencies not only enhance manufacturing precision but also create a more cost-effective production environment.
The impact of these advancements extends beyond individual companies; they also contribute to the overall competitiveness of the manufacturing sector on a global scale. As manufacturers adopt modern press tooling techniques, they position themselves to capitalise on emerging opportunities and navigate the challenges of a rapidly changing market. The combination of high precision, reduced costs, and shorter design timelines not only benefits manufacturers but also translates into better products for consumers, reinforcing the essential role of press tooling in the future of precision manufacturing. With continued investment in these cutting-edge techniques, the potential for innovation and excellence in manufacturing is boundless.
Brandauer’s expertise in global press tooling solutions
With over 160 years of experience, Brandauer has established itself as a leader in global press tooling solutions. This expertise lies in Brandauer’s development of modular precision tooling, which helps manufacturers to reduce lead times, minimise maintenance costs, and ensure the consistent production of high-quality components.
Brandauer’s investment in press tooling innovation exceeds £2 million, with £1.5 million allocated to upgrading its toolroom in Birmingham. Additionally, the company has forged research partnerships with the WMG Group and Birmingham City University, further cementing the manufacturer’s position as a pioneer in press tooling technology.
What sets Brandauer apart from competitors is a focus on modular tooling solutions. Traditional tooling methods often require separate tools for each component size, leading to longer production times and higher costs. In contrast, Brandauer’s modular tooling enables manufacturers to produce multiple component sizes using the same tool. This flexibility is especially valuable in industries such as electric mobility, med-tech, and aerospace, where demand for precision and cost-efficiency continues to grow.
Future trends: press tooling advancements to watch
While processes in global manufacturing continuing to evolve, the field of press tooling is following it closely. Several trends are emerging that promise to revolutionise how manufacturers approach tooling design, production, and maintenance.
The following advancements are shaping the future of press tooling, enabling manufacturers to enhance efficiency, reduce costs, and improve product quality. Keeping an eye on these trends will be essential for companies looking to stay competitive in the wide market of global manufacturing.
Modular Precision Tooling
Modular tooling, as exemplified by Brandauer’s innovations, will continue to gain traction in the coming years. The ability to quickly change over tools and replace specific modules rather than entire tools will reduce downtime and extend the life of press tools. Manufacturers can expect up to a 25% reduction in tooling costs and lead times cut by 6-9 weeks due to these advancements.
Automation and Smart Tooling
Automation is set to play a pivotal role in the future of press tooling. Automated processes allow for faster tool changeovers, improved production efficiency, and better on-time delivery rates. For instance, Brandauer’s integration of automation has increased its on-time delivery from 50% to 93%. Furthermore, real-time monitoring through sensors embedded in press tools allows manufacturers to identify wear and tear on tools, preventing breakdowns and reducing maintenance time.
Sustainability in Tooling Processes
Sustainability will be a critical focus for manufacturers looking to reduce waste and optimise resource use. Press tooling innovations, such as Brandauer’s modular approach, will help manufacturers extend tool life by millions of blows between maintenance cycles. This not only cuts down on waste but also ensures that fewer raw materials are used in the production of new tools.
Digitalisation and IoT Integration
Digitalisation is another key trend transforming the press tooling industry. The integration of IoT (Internet of Things) technologies allows manufacturers to monitor tooling performance in real time. By gathering and analysing data, manufacturers can make informed decisions about when to replace or repair specific tool components, improving overall production efficiency and reducing downtime.
Electrification and E-Mobility
The rise of electrification in the automotive industry is another trend that will drive the future of press tooling. As demand for electric vehicles (EVs) increases, manufacturers will need highly precise tooling solutions to produce the components required for electric motors and batteries. Brandauer’s press tooling expertise in producing high-precision laminations for electric motors positions the company as a key player in this rapidly growing sector.
Advanced Materials in Tooling
While the use of advanced materials in press tooling is still in its early stages, it is likely to become more prevalent in the future. Materials with higher wear resistance and strength could help extend the lifespan of press tools even further, reducing the need for frequent repairs or replacements.
Skills Development and Training
Finally, the future of press tooling will depend on the development of skilled toolmakers. Brandauer’s co-funding of a £1 million Precision Tooling Academy is a prime example of how the industry is addressing the skills shortage in toolmaking. By training the next generation of toolmakers with expertise in modular tooling, the industry will ensure that manufacturers can continue to innovate and meet the demands of a rapidly changing global market. As well as this, the Level 6 Tool Process Design Apprenticeship and other similar courses ensure that essential skills are transferred to UK manufacturing.