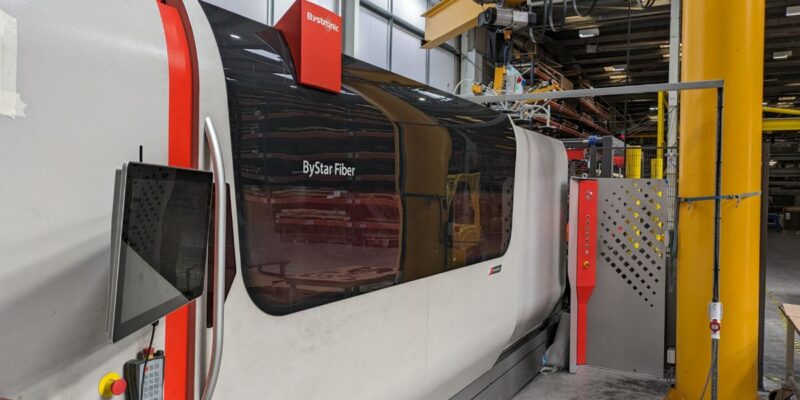
Metal fabrication, transforming raw metal into finished products, has evolved remarkably. What once relied heavily on manual labour and traditional techniques such as metal flattening, bending, and forming has been revolutionised by mechanical automation in modern metal fabrication workshops. Wrightform take a quick look into the journey of metal fabrication, exploring how manual processes have evolved into automated systems and the role of key machines such as press brakes, metal flattening machines, and laser cutting machines in driving efficiency and productivity.

From Manual to Mechanical
Historically, metal fabrication involved highly skilled craftsmen utilising hand tools and machinery to shape metal components. Processes like metal flattening, where raw metal sheets are compressed and smoothed, require considerable physical effort and time. Similarly, bending and forming metal into desired shapes relied on manual manipulation of the material using tools like hammers, anvils, and manual presses.
However, as technology advanced, the landscape of metal fabrication underwent a significant transformation. The introduction of mechanical automation revolutionised the industry, paving the way for faster, more precise, and more efficient production processes. Manual tasks that were once labour-intensive and time-consuming began to be replaced by automated machinery capable of performing tasks with greater speed and accuracy.
Key Machines in Modern Metal Fabrication
Press Brakes: Press brakes are versatile machines that bend and form metal sheets and plates. They feature a hydraulic or mechanical ram that applies force to a die, bending the metal to a desired angle. Modern press brakes have advanced controls and automation features, allowing for precise control over bending parameters such as angle, depth, and speed. CNC (Computer Numerical Control) press brakes enhance efficiency by automating the bending process based on programmed instructions, reducing setup time and minimising errors.
Metal Flattening Machines: Metal flattening machines, also known as levellers or straighteners, are used to flatten and smooth metal sheets, eliminating wrinkles, waves, and distortions. These machines utilise rollers or adjustable plates to apply pressure evenly across the surface of the metal, restoring it to a flat and uniform state. Automated metal flattening machines feature advanced sensors and controls that monitor and adjust pressure levels in real time, ensuring consistent flattening results across different materials and thicknesses.
Laser Cutting Machines: Laser cutting machines have revolutionised metal fabrication by offering precise, high-speed cutting capabilities with minimal material waste. These machines use a focused laser beam to melt, burn, or vaporise metal, creating intricate shapes and patterns with exceptional accuracy. CNC-controlled laser cutting machines allow automated cutting of complex designs based on digital blueprints or CAD (Computer-Aided Design) files. This eliminates manual cutting and reduces production time significantly, making laser cutting an indispensable tool in modern metal fabrication workshops.
Benefits of Automation
Adopting mechanical automation in metal fabrication workshops has brought numerous benefits, driving efficiency, productivity, and quality across the manufacturing process. Some key advantages include:
Increased Speed – Automated machines perform tasks much faster than manual labour, reducing production time and enabling faster turnaround of orders.
Enhanced Precision – Automation ensures consistent and precise results, minimising errors and improving product quality. CNC-controlled machines offer unparalleled accuracy in bending, flattening, and cutting metal components to specifications.
Improved Safety – Automated machines eliminate many safety hazards associated with manual labour, reducing the risk of workplace accidents and injuries. Advanced safety features and interlocking systems enhance operator safety in modern metal fabrication workshops.
The evolution of metal fabrication from manual to automated processes represents a transformative journey driven by technological advancements and innovation. Mechanical automation has revolutionised the industry, enabling metal fabrication workshops to achieve unprecedented efficiency, productivity, and quality. Key machines such as press brakes, metal flattening, and laser cutting have played a pivotal role in this evolution, offering faster, more precise, and cost-effective solutions for shaping and manipulating metal components. As the industry continues to embrace automation, the future of metal fabrication holds exciting possibilities for further advancements and improvements in manufacturing processes.
Finally, it is important to emphasise the importance of prioritising quality control and assurance in your metal fabrication operations. At Wrightform, we have implemented robust quality control measures at every production phase. When selecting a subcontractor, ensure they uphold stringent quality standards to guarantee the accuracy and integrity of fabricated components. With thorough inspection protocols, you can have confidence that your parts will consistently meet or surpass industry benchmarks, minimising the likelihood of errors and rework.