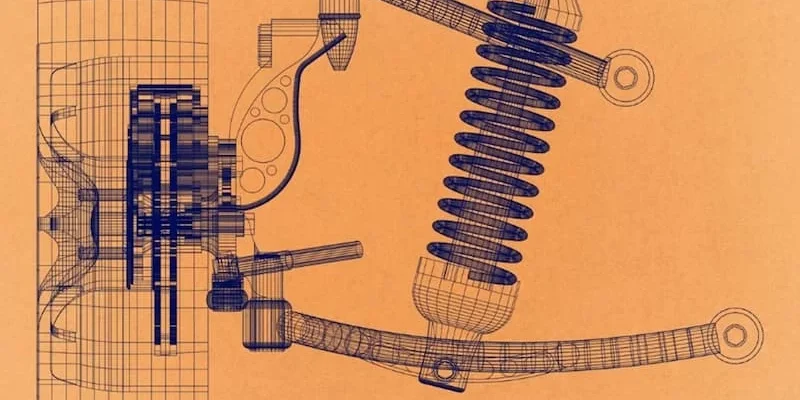
Springs are essential components within almost every application, from commercial products to industrial machinery and transport. The unique requirements of these varied applications demand the creation of a broad range of spring designs, each tailored to fulfil a specific role; this is where spring design comes in.
Read on to explore the complexities our engineers and spring designers overcome as they mass-produce a broad range of these invaluable components for every industry.
THE IMPORTANCE OF SPRING DESIGN
The importance of design in spring manufacturing cannot be overstated. Precise measurements and careful consideration of various elements are crucial. A bespoke spring design must account for factors like type, load, and movement, as even the slightest alteration can impact performance.
For example, simply changing the material of a spring can significantly impact its capabilities, even without modifying the dimensions. Even a slight adjustment to the outer diameter of a spring can make a world of difference.
When designing a spring, it is essential to consider aspects such as free length, solid height, number of coils, travel and load, force capacity, spring ends, and inner diameter.
We collaborate closely with our clients during the manufacturing process, ensuring our experienced team can effortlessly assist in creating the perfect spring design for your project.
Moreover, it is vital to prioritise spring design before finalising other components of your product. Neglecting spring design can result in safety issues or failure to perform as desired.
A well-thought-out spring design produces the following benefits:
- Longevity, as the design considers the spring’s operating environment and material specifications.
- Exceptional quality, thanks to carefully selected spring materials and manufacturing processes.
- Compatibility with the product it will be integrated into, as precise dimensions are accounted for during the design stage.
Considering the correct spring design also helps to avoid budget overruns. Improperly designed springs can be unreliable, potentially causing product launch delays and increased expenses due to rework or requiring additional batches. By ensuring the initial design is correct, you can have functional springs with the right dimensions, eliminating the need for fixes or reordering.
At European Springs, we encourage collaboration with our customers with our spring design support service to understand your specific needs and ensure that every aspect of spring design is thoroughly evaluated to deliver the best possible results.
Force, Displacement and Stiffness in Spring Design
The fundamental characteristic to remember about springs is their ability to store potential energy when deformed and release it when the deforming force is removed. Force is not the only aspect to consider when designing spring specifications; there is also displacement and stiffness. Here is an explanation of what defines each:
- Force refers to the applied external load or the resistance a spring offers to deformation.
- Displacement is the change in position or length of a spring when subjected to a force.
- Stiffness, however, quantifies how resistant a spring is to deformation. It is determined by the spring’s material, geometry, and dimensions. Higher stiffness means the spring requires more force to induce a given displacement.
Understanding the relationship between force, displacement, and stiffness is key to designing efficient and reliable springs. These fundamentals are essential to establishing the core requirements of the eventual spring design.
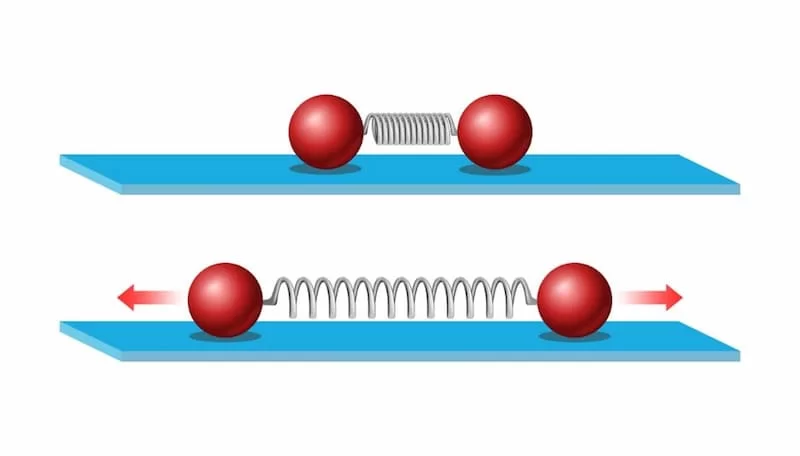
SPRING DESIGN CONSIDERATIONS AT EUROPEAN SPRINGS
Designing an effective spring requires a thorough understanding of its operating environment, the application requirements, and the spring material’s physical characteristics. For designers and manufacturers to achieve optimal performance from a custom spring, they must consider several fundamental design principles.
SPRING MATERIAL CHOICES
One of the most critical factors in spring design is the choice of material. Selecting the right material can ensure that the spring has the required strength, durability, and corrosion resistance for its intended use. Common materials used in spring manufacturing include stainless steel, carbon steel, high-carbon spring steel, and alloy steel.
Once the material is chosen, designers must consider the spring’s dimensions. Spring dimensions are calculated with a high degree of accuracy using theoretical models. At European Springs, their designers use in-house developed software for all traditional spring types and specially configured FEM software for complicated geometries. This ensures the spring can withstand heavy loads, achieve the required deflection, and maintain its shape and function over time.
SPRING MECHANICS AND FUNCTIONALITY
Designers must also be mindful of each metal’s mechanics, strength theories, and potential functionality. The effect of residual stresses and the control of these stresses are important and are always considered in every design. Our experts maintain detailed knowledge of the many applications and all the standards and specialities that are required for optimal spring design.
Another critical factor to consider is the processing methods involved in spring manufacturing. Processes such as coiling, end grinding, shot peening, and heat treatment are all important considerations in spring design, as they can affect the spring’s performance, fatigue resistance, and longevity. At European Springs, its manufacturing process is adaptable to any specific customer requirement, with various treatments applied to its springs, from electroplating to powder coating.
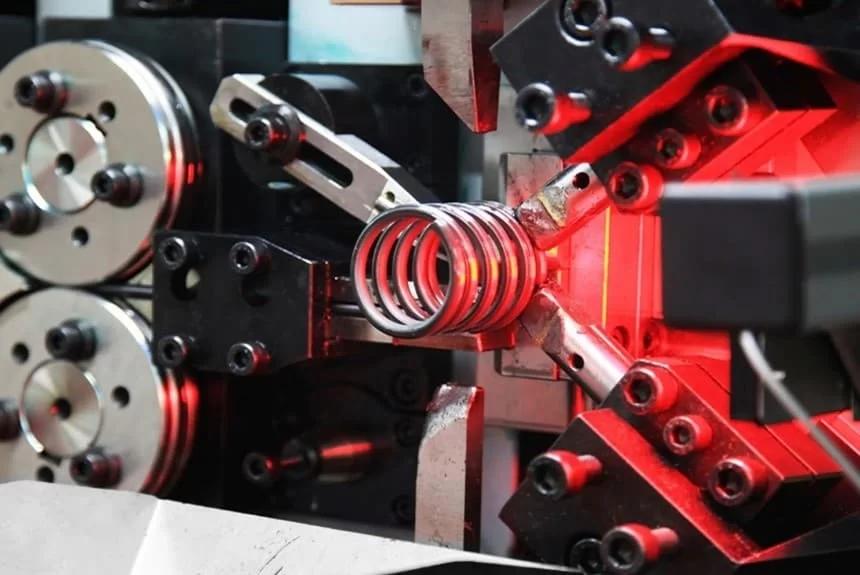
Furthermore, high-speed shock loading and transient phenomena are areas that are important in some applications and are taken into consideration by industry experts. Professional teams can select stress levels through specific training and experimental processes, evaluate creep relaxation and fatigue performances and determine the best processing methods and surface treatment for a particular application.
It is worth noting that the process of spring designing involves many different branches of science. This includes the above-mentioned material science, processing methods, and mechanical engineering theories, spring manufacturing technology, and the importance of tool/control of residual stresses. European Springs encourages and supports customers with a high understanding of springs, spring materials, and surface treatments to work with the company’s team of experts to achieve the best products in the spring and pressing field.
Prototyping and Testing
Prototyping and testing play pivotal, final role in the spring design process. Through iterative design improvements and validation, we refine our designs to achieve optimal performance and reliability. By closely examining each aspect of the prototype and rigorously testing it in real-world conditions, we ensure that our springs meet the highest quality and performance standards.
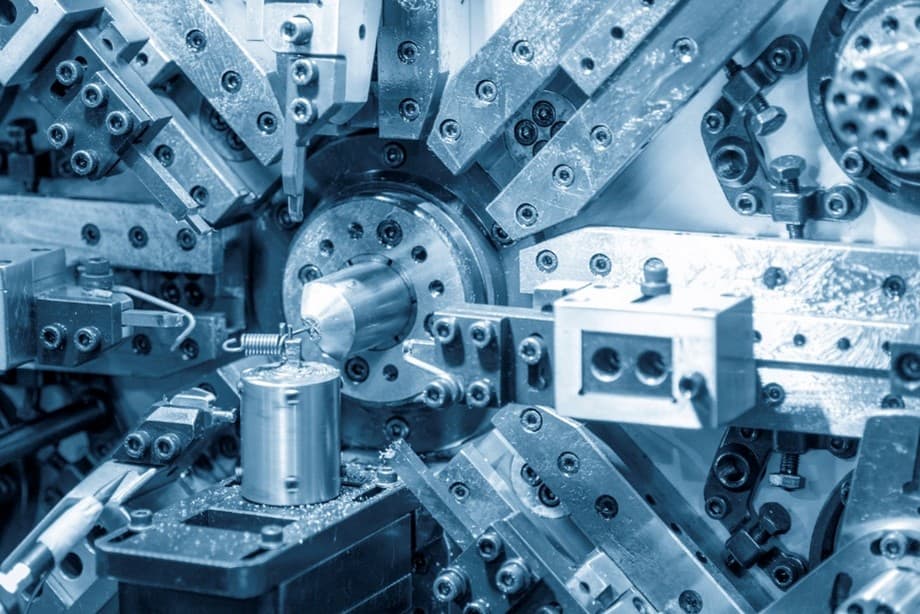
BESPOKE SPRING DESIGN AT EUROPEAN SPRINGS
At European Springs, we pride ourselves on our expertise and commitment to delivering exceptional prototype spring and pressing designs. With our team considering various design factors, embracing innovative approaches, and employing collaborative design processes, we create springs that perform flawlessly and enhance the overall design.