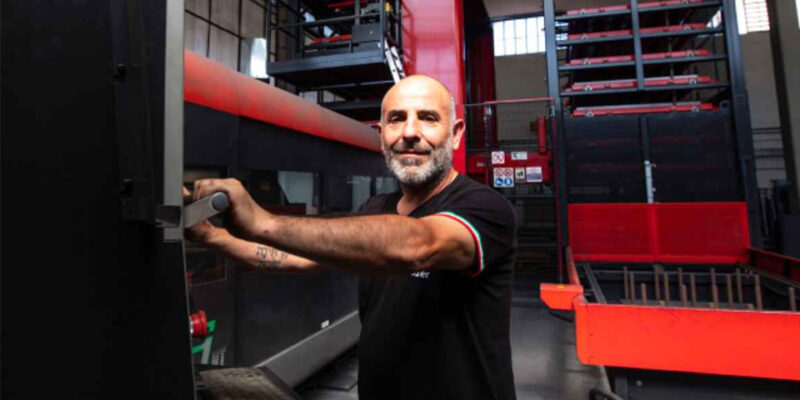
Microlaser Srl is a sought-after partner in the region when it comes to the production of semi-finished sheet metal products manufactured using laser and oxyfuel cutting technology. In addition to cutting, the company also offers the option of further processing by folding and bending.
The company’s flat organizational structure allows easy and flexible access to all internal resources and facilitates the coordination of different departments for lean and fast production.
Why the change?
One of the reasons that led Microlaser to look for a new software solution was the search for better technical support. Silvia Donnini explains that while it is important to first have a program that is technically suitable for production, it is equally crucial to have a qualified vendor service at your side at all times.
At SigmaNEST, both the sales and technical teams are always available to Microlaser. The smooth communication during the implementation of SigmaNEST as well as the intuitive user interface, which allowed a quick learning curve, proved to be success factors.
Switching to a new software is not easy, but in this case, even the habitual users who had a deep attachment to their previous software successfully accepted the change. After identifying priorities in a workshop, SigmaNEST’s technical department worked with Microlaser’s IT manager to coordinate smooth implementation and training. Giving the customer the tools to manage the program independently was the first of many points discussed.
For sheet metal processing, Microlaser Srl relies on an Amada LC3015 F1 for laser cutting, an Amada HFP220-4L for bending, and an Esab Suprarex Rxe for oxyfuel cutting.
The decisive element for the turnaround
The strong customer/supplier relationship built between the Microlaser and SigmaNEST teams was the cornerstone of this installation. The owner of Microlaser explains that it is not easy to find a partner who understands the real needs on the shop floor and wants to implement the most appropriate solution.
Competence and availability were key factors in the final selection. In the end, the entire staff was behind the decision. Apart from the quality of the software product, which could be evaluated and confirmed at an early stage, Microlaser’s expectations regarding all additional services were met.
The workflow at Microlaser
The implementation of SigmaNEST and SigmaMRP on the shop floor enables a smooth workflow. The interchange of information between the programs and the resulting real-time communication between the different departments makes the production flow from the office to the shop floor much more efficient. Scheduling priorities and job preparations are properly managed, and orders are processed while minimizing human error.
In addition, the automation of the SigmaNEST solution allowed the company to reallocate human resources in the areas where they were most needed—after the retirement of an employee from the technical office, the company was able to use the freed-up financial resources to reinforce the staff in the workshop, thus improving production quality and the company’s competitiveness.
Plans for the future?
In the coming months, the company plans to migrate from their self-developed quoting software into the integrated quoting process of SigmaMRP and SigmaNEST. In this way, all information will be managed with the same software, which will be adapted to Microlaser’s needs while maintaining SigmaNEST standards.
Further on, Microlaser has a desire to completely eliminate paper and digitize all processes and controls. Their goal is both to drastically reduce human errors, and to transform their business towards environmental sustainability.
Microlaser srl www.microlasertaglio.it