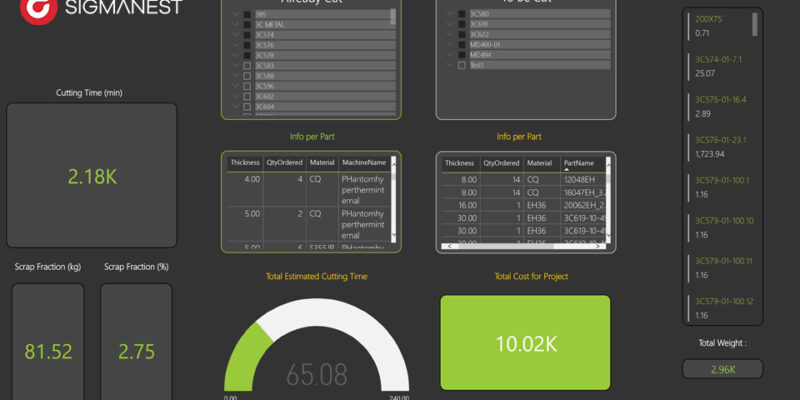
Time, performance and cost considerations are paramount when investing in programming tools
Fabrication software has consistently tapped into computer-aided manufacturing (CAM) to provide the programming for fabrication equipment. But software has quickly evolved to capture price quotes, shop floor data and more—driving profitability and key business decisions.
“That wasn’t the case as much as 15 years ago. But it certainly is true now,” says Kevin Keane, product strategy manager for software developer SigmaNEST. “Fabrication software now gives business owners the enhanced ability to actively manage the operation. This can include monitoring the effectiveness of the shop to improve throughput, increase quote conversion rates to generate more business, or by automating mundane tasks that choke off employee productivity,” says Keane.
Effectiveness can mean different things to different business owners. In general, effective management yields predictability, productivity and profitability. After a number of years in the aerospace industry, Keane pivoted to software and joined SigmaNEST in 2000. In his role there, he draws on his aerospace roots and takes the long view in software technology, appreciating the advancements already made in the industry. “Now there is more demand for software to tie together the activities of a shop’s people, equipment and business outcomes.”
Three Pillars
Sigma Nest’s portfolio of software comprises three pillars of technology: CAM software, manufacturing ERP software and shop floor management software. The Cincinnati-based company has long been a provider of CAM software that optimizes material use (SigmaNEST for flat products, SigmaTUBE and SigmaCTL for long products). Integral to these solutions are advanced nesting capabilities with a wide range of customizable, modular features. A team of mathematicians and engineers develop and maintain the software. “We also have a sophisticated material analyst tool to inform the amount of material required for inbound jobs. This tool can give the fabricator a heads-up to order specified material if it’s not in the shop,” Keane points out. “Fabricators don’t always want to keep a lot of inventory on hand.”
Predictability and Consistency
Leveraging advanced fabricating software allows the user to plan and schedule workflow and completion dates with more accuracy. “It’s one of the first things a customer asks: ‘When can I have it?’ The definition of predictability is knowing what works and doing it over and over again with the same expected outcome. Collecting and using accurate data from the shop floor enables predictable outcomes,” explains Keane.
Another key aspect of effective planning and scheduling is the ability to anticipate and solve congestion points on the shop floor. “When the customer has the wider field of view, they can redirect work around a bottleneck to optimize each piece of equipment and minimize downtime,” Keane says.
Another outcome of predictability is controlling material costs. SigmaNEST software can calculate how much material will be needed for a job.
“This is where our nesting expertise comes in. With robust nesting, waste is minimized,” states Keane. Waste is an example of a hard cost. But utilizing all the knowledge from data generated by software can minimize soft costs as well.
“Let’s say the nesting software reduces the number of sheets needed for a large run of parts by 10 percent. That could translate to fewer cycles of the crane or forklift, as well as fewer sheets to load and fewer skeletons to transport to the recycling bins,” Keane explains.
Productivity and Quality
Rigorous quality standards are the norm for aerospace and every other industrial sector. Adherence to a quality management system, like ISO 9001 or Six Sigma, is commonplace on the fabrication shop floor. “Monitoring part quality is an essential indicator to areas for improvement and enhanced productivity,” says Keane. He uses as an example the quality of a finish or a cut. “When the fabricator improves cut quality, it influences other downstream activities in terms of time, performance and cost. An improvement in cut quality translates to less grinding, so [you are using] fewer grinding discs, less PPE and less labor to rework parts,” he says. “Through the collection of shop floor data, SigmaNEST software is more than just a product. It’s a productivity enabler.”
Profitability and Efficiency
Using an integrated software system for price quoting brings consistency to the estimating process. Software can provide data that helps an estimator determine the amount of material required for a project.
“A unique benefit of the SigmaNEST manufacturing ERP solution is the tight coupling with the CAM software; this simplifies the user experience, providing accurate quotes very quickly. For a fabrication shop, being able to compare what they thought would happen (estimated) to what actually happens, puts the results in the crosshairs of the business. Having all this data integrated within one family of software makes it easier for the business to get a realistic perspective on their estimating accuracy,” Keane notes. “Each time a fabricator quotes a job accurately, it’s an opportunity to be profitable.”
Changing Requirements
In the past 20 years, Keane has witnessed significant changes in the fabrication industry and customer needs. The level of sophistication of fabrication machines and ancillary equipment has been elevated. “There’s a lot more technology on today’s equipment. This means the level of training and skills required of the operator—and for equipment maintenance— has also increased,” says Keane. The desire for automation is growing exponentially. “In the U.S., we are seeing a lot more automation coming on line, for example robotic loaders and unloaders. This trend started elsewhere and has migrated to the U.S.,” explains Keane.
Post-pandemic, another customer concern is attracting and retaining skilled personnel. “A tool like SigmaNEST can give shop owners more flexibility in hiring. We bring consistency to the estimating process, so an employer can hire a new estimator who can work within the guardrails of the software and get up to speed quickly,” suggests Keane. The same applies to CAM. A new equipment operator can be brought in and work within the confines of the SigmaNEST software. “These guardrails also apply to existing team members who are being cross-trained on other shop floor equipment.”
Staying Current
Because SigmaNEST software is not developed by an equipment manufacturer, it is machine agnostic and integrates with other software platforms. “As a software developer, we have evolved with the best practices of the software industry,” notes Keane. SigmaNEST offers a customer portal for live updates and guided installation support to get customers onto the latest version of their software.
“Our architecture also allows users to write their own plug-ins. And we have open APIs for customers that have in-house capabilities. We expect this capability to increase over time at fabrication shops,” predicts Keane.
For fabricators in an increasingly digital world, Keane advises self-reflection: Does my software help me capture and access my information? It is never too late to “look at how hard your software and data are working for you to streamline operations and accelerate profits,” he says.
Published in FFJournal, February 2023
“Proactive Management”
https://www.qgdigitalpublishing.com/publication/