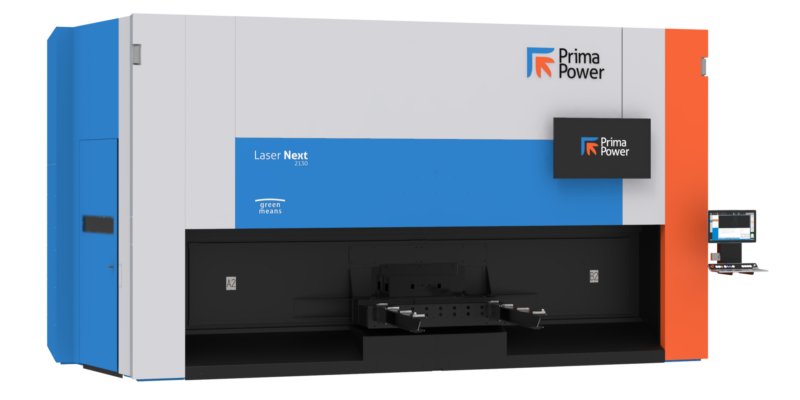
Siemens, the global technology company leader in industrial automation and digitalization, and Prima Power, the world-class manufacturer of sheet metal working machinery and 3D laser cutting technology, are proud to announce the result of an intensified collaboration that is redefining standards in the automotive manufacturing industry.
This collaboration has led to the integration of Siemens’ leading numerical control system, SINUMERIK ONE, into the latest model of Prima Power’s flagship 3D laser cutting machine, Laser Next. Laser Next 1530/2130 is the first Prima Power’s 3D laser cutting machine on the market to be equipped with Siemens’ SINUMERIK ONE.
This collaboration between two industry leaders leverages Siemens’ cutting-edge control & digitalisation systems and over 40 years of Prima Power’s expertise in laser technology for automotive applications and set new benchmarks for productivity, efficiency and integrability in the vehicle manufacturing.
Advancing 3D laser cutting through integration
The new version of the 5-axis laser machine Laser Next incorporates state-of-the-art technologies to offer improved dynamic performance and productivity achieved through the flexible and high-performance multicore architecture of SINUMERIK ONE, combined with Prima Power’s proprietary algorithms.
Laser Next 1530/2130 equipped with SINUMERIK ONE results more productive, faster, flexible and more efficient also thanks to integrated SIMATIC S7-1500F PLC controller and Siemens
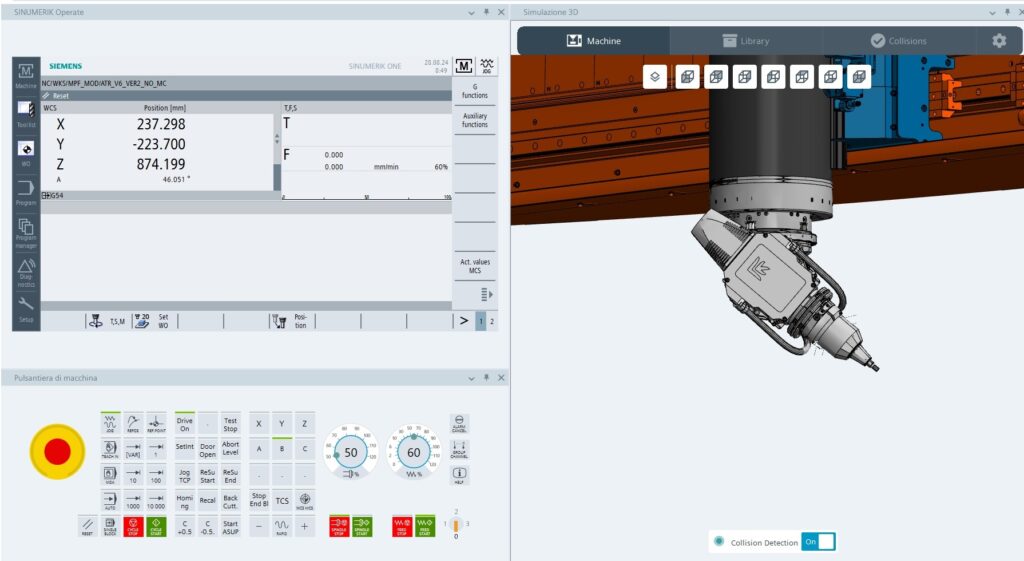
Totally Integrated Automation Portal ecosystem.
Laser Next 1530/2130, with SINUMERIK ONE, sets new trends in manufacturing efficiency and sustainability introducing Siemens’ Digital Twin capabilities. The Digital Twin of SINUMERIK ONE, – Create My Virtual Machine -, has been a key element in Prima Power digital transformation helping the Prima Power R&D department to simulate and test workflows in a completely virtual environment.This innovative Digital Twin made it possible to engineer and optimize the machine even before the real-life new Laser Next prototype was made available with significant shortening of machine’s time to market.
The Digital Twin of the machine enables the creation of an accurate digital replica: the entire process is virtualized, eliminating the need for physical machining on the shop floor for certain activities. Furthermore, in SINUMERIK ONE collision avoidance functionalities can be enabled even in complex scenarios, involving cutting machines integrated with robotic solution. Digital Twins address real-world challenges, enhancing business efficiency and safety and fostering sustainability.
The machine’s compatibility and integration capability have also been significantly enhanced. Incorporating the advanced safety features of SINUMERIK ONE allows to meet global safety standards without the need for additional modules, in fact thanks to the comprehensive integration of the safety functions in the control and drive technology of SINUMERIK Safety Integrated, the system is extremely efficient and flexible.
The integration with automation systems is streamlined, thanks to Siemens’ availability of comprehensive PLC standard communication protocols. Moreover, compatibility with OPC-UA and MQTT communication protocols meets global market demands for simplified integration of data collection systems, enabling endless solutions for data-driven application development.
Highly integrated security functionalities are a further plus of the new Laser Next model achieved through SINUMERIK ONE, certified in accordance with IEC 62443 and offering a comprehensive protection through the Siemens “Defense in Depth” concept, safeguarding plant, network, and system security. With “Defense in Depth,” Siemens provides a multilayer security concept that gives machines and plants both all-round and in-depth protection as recommended by the international standard IEC 62443. It is aimed at plant operators, integrators, and component manufacturers alike, and covers all security-related aspects of industrial cybersecurity.
A synergy for customer success
The synergy between Prima Power’s advanced laser technology and Siemens’ innovative control & digitalisation systems offers automotive manufacturers a powerful solution to level up their production processes. The combined strengths of the SINUMERIK ONE and Laser Next 1530/2130 are set to drive significant advancements in performance, security, and digitalization, making them ideal solutions for the evolution of smart automotive manufacturing.
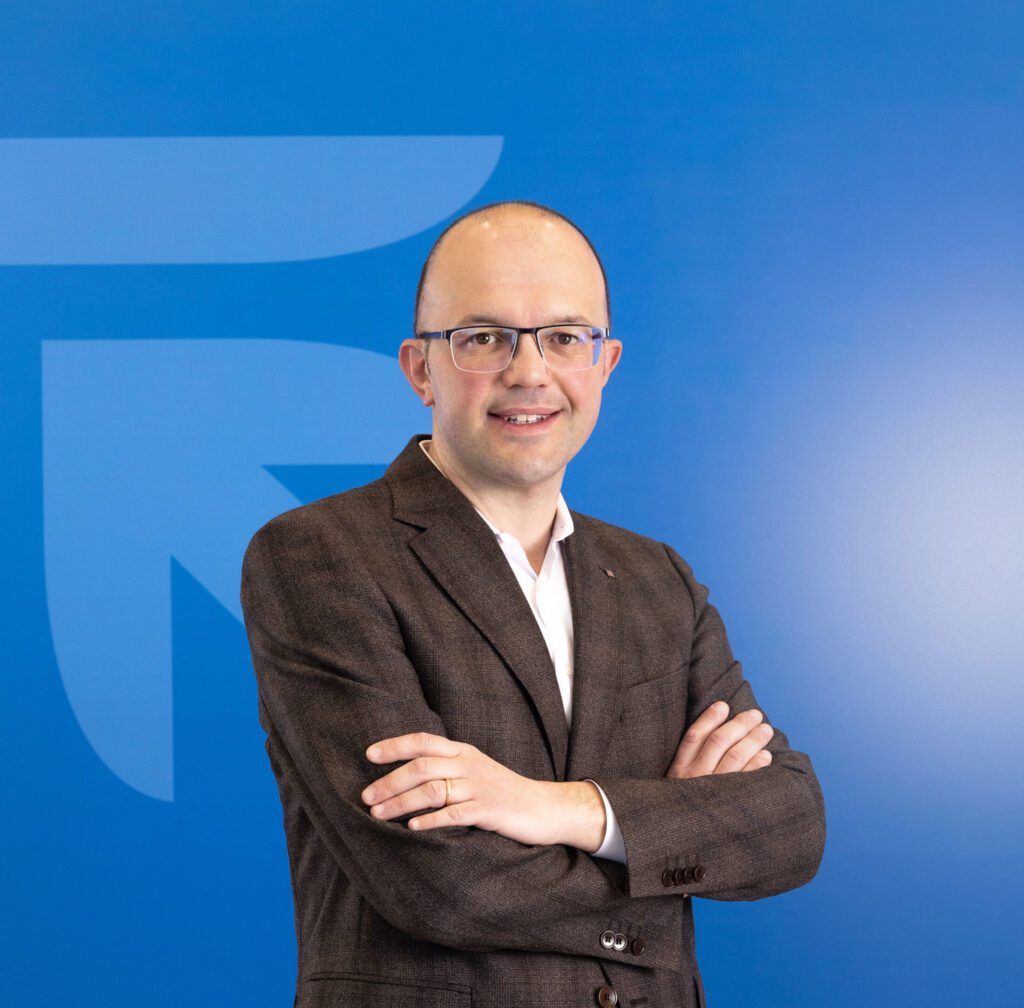
“This successful collaboration between two industry leaders combines Siemens’ pioneering expertise in high-performance, digitally-native CNC systems with Prima Power’s extensive knowledge in laser technology for automotive manufacturing. This synergy is embodied in our latest 3D laser machine, the fastest on the market, boasting +20% higher dynamic performance and a +13% increase in productivity for typical automotive production. Marking a significant milestone in the automotive production sector, Prima Power’s Laser Next is the first 3D laser cutting machine on the market to be equipped with Siemens’ SINUMERIK ONE. This cooperation is a key element in our ‘Evolve by integration’ strategy. We provide our customers with advanced, future-ready solutions that level up their manufacturing processes to new heights” stated Giovanni Negri, CEO of Prima Power and Prima Industrie Group.
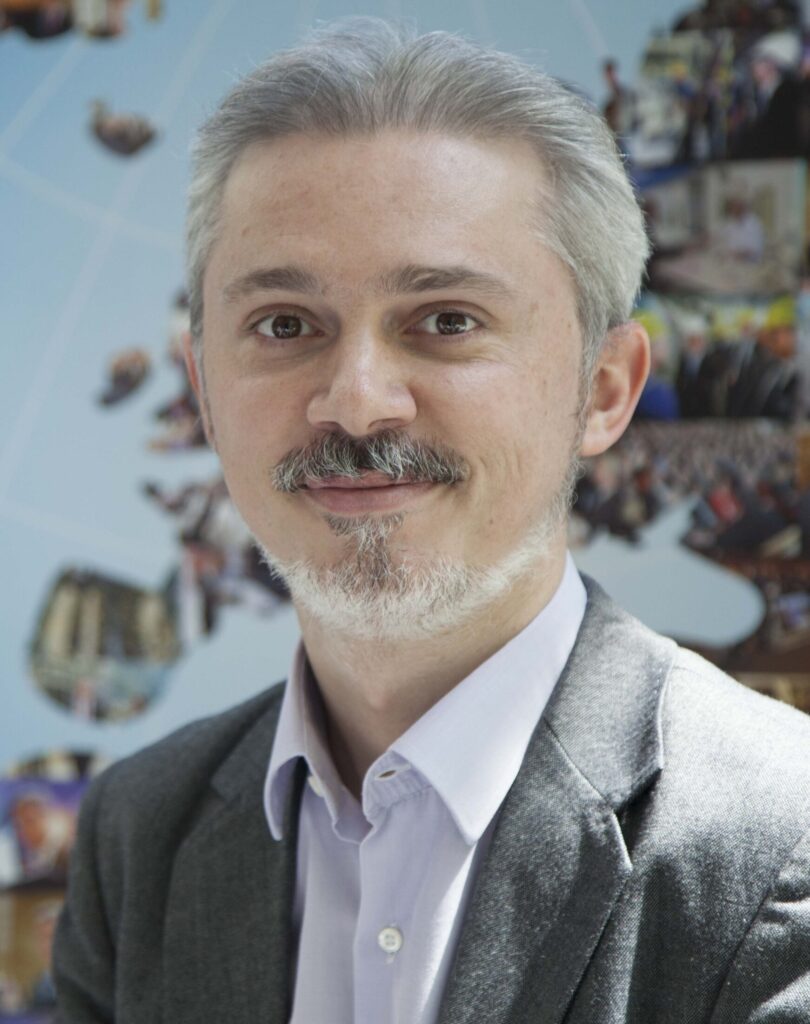
“We’re enthusiastic about this collaboration with Prima, as its well-known expertise in laser technology and innovative approach to machine design, particularly using digital twin, have been key drivers of this fruitful cooperation. The Siemens digital twin & digitalization portfolio allowed Prima Power to further optimize the performance and speed of Laser Next machines, resulting in a significant increase in competitiveness. Siemens advanced technology represents a future-proof platform for Laser Next machines, ensuring a high level of performance and flexibility. It enables to meet the growing demands of end users for secure, powerful, and innovative machines. We look forward to continuing this successful collaboration and driving further advancements” stated Massimiliano Galli Head of Motion Control at Siemens Digital Industries in Italy.