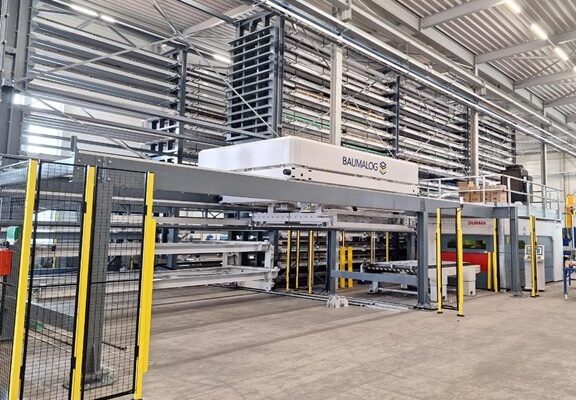
There are many ways in improving production efficiency which can change the nature of metal sheet processing. The implementation of automation systems requires the identification of the needs and challenges that exist in a production company. Based on this, a proper solution can be designed to make the whole production process more efficient. In case of sheet metal processing, innovative automation systems are a way to increase production efficiency – from the start of the storage process, through the flow of material to the processing machine, to the collection of cut details and their transport to the final stations or back to the automated storage system. Automation systems described in the following article are offered by Baumalog company.
The efficiency of the production process is a complex issue, consisting of the machines availability and their skilful use to exploit their full potential, as well as the human factor, which is responsible for carrying out not-automated activities. Increasing production efficiency is made possible by innovative automation solutions that are able to significantly improve the quality of the material handling process. Automation systems make it possible to increase the availability and thus the efficiency of laser cutting machines or bending centres.
Increasing availability of the machines
Improving machine availability involves, among other things, reducing planned machine downtime by unloading and loading the machine table. Availability decreases when an operator is solely responsible for unloading and loading of the machine. This type of work is more demanding and requires a high energy input from the operator throughout the shift. An automation system can change the picture of this activity.
The automated loading and unloading MultiLoader system consists of two independently moving modules that minimise the downtime of the processing machine. The loading and unloading station picks up a sheet from the storage system’s shelf and transports it straight to the laser cutting machine table – the whole process is repetitive in a fixed time interval, enabling 24/7 operation without the constant presence of an operator.
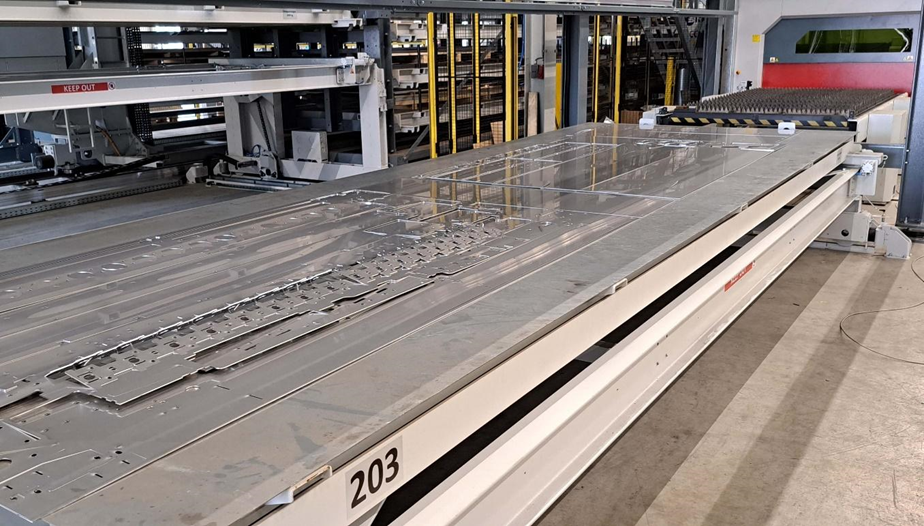
SmartFlow System from Baumalog – the answer to market needs
The use of an automation such as the SmartFlow System makes it possible to fully optimise the efficiency of production processes. The loading and unloading of processing machines would not be possible without a properly designed material flow, which starts when the material enters the production hall. SmartFlow System makes it possible to combine an automated storage system and transport modules. This enables comprehensive management of the production hall, which is significantly simplified by the Smart WMS software, which allows inventory monitoring or data reporting. Combined with the duo station, which delivers material from the storage system to the loading and unloading stations by the two independently operating levels, it forms a coherent whole that significantly improves the efficiency of the production process.
Storage and production automation at Ter Horst company
Ter Horst company, based in the Netherlands, from many years specializes in metal processing. To improve its storage processes, in 2021 the company implemented an automated storage system MultiTower in its production hall, which was expanded in spring 2023 to include an automation module for a Durma laser cutting machine for cutting sheets with a maximum dimensions of 3 m x 1.5 m.
The additional automation module made it possible to utilize the full production capacity of the laser cutting machine in operation and streamlined the flow of material from the storage system shelf to the processing machine table and the return of cut parts to the shelf. This eliminates the most repetitive and time-consuming operator’s activity of transporting the material to the right place. The entire task is taken over by the automation module and the operator is moved to more high-value work.
The process of sheet metal flow to the production machines, which is optimised by the SmartFlow System, is a key element both in companies where the production of the smallest details is carried out in-house and in companies providing sheet metal cutting services. In both cases, the production of these types of parts can be carried out on a 24/7 basis. Working with this system requires appropriate planning and automation of the processes, also to change the nature of the operator’s role and thus significantly improve the efficiency of the production process.