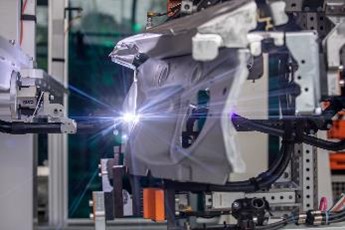
Acerios hot active plasma technology from Fronius removes particulate and film impurities from both metallic and non-metallic surfaces. Auto manufacturer Audi has been using the process on thin aluminum body parts for the last two years. Acerios has substantially reduced cleaning costs in those areas where metal sheets have to be prepared for stud welding. At the same time, resource efficiency has also been increased.
“In the worst case, the failure of a ground stud connection can bring a vehicle to a complete stop,” says engineer Daniel Rudolph, technology developer responsible for joining and lightweight construction at Audi AG. “In building the Audi A8, we fit numerous ground studs and have to make sure that every single one is perfectly connected. We go to great lengths to meet the quality requirements.”
This is because the quality of every stud weld critically depends several factors, including the surface characteristics. Contamination by drawing oils and dry lubricants – as used in metal forming – can lead to a defective joint.
Clean flash unsuitable on thin sheets
The problem of contamination can often be solved with the stud welding unit itself. This involves supplying a burst of current (clean flash) upstream of the actual welding process, which cleans the welding surface. However, this approach is not practicable for aluminum sheets less than 2 mm thick, as the heat input is too high and the sheet would burn through during the welding process. Other problems include the fact that pores can occur with this process, which negatively affect the weld seam quality.
One such part at Audi is the bulkhead of the Audi A8. This is made of aluminum sheet alloy (6xxx) and is only 1.5 mm thick at those points where ground studs are welded: “In the first few years after series production began, the whole part had to be chemically cleaned and pickled, which was both time-consuming and expensive,” explains Rudolph. “That was the only way we could definitely guarantee the requisite 100 percent quality of the stud welded joint.”
In 2017, Audi was about to build a new production line for the fifth generation A8. It wanted to find a way around the complex chemical cleaning process. Hot-active plasma (HAP) technology, which the company’s long-standing welding technology supplier and development partner Fronius was already working on intensively, was seen as a possible solution. Audi had also been pursuing the HAP approach with university partners.
As Rudolph’s responsibilities also include evaluating new manufacturing technologies and developing them for series production, the joining technology specialists from Audi and Fronius worked together closely. This engineering approach was then jointly developed and certified for series production. Rudolph explains: “Fronius was mainly responsible for developing the process and system technology. Our production department then carried out application-oriented function trials, parameter tests, service life tests, and functional tests. We also addressed the question of how the use of the technology affects further process chains such as joining, strength, paint adhesion, and a lot more besides.”
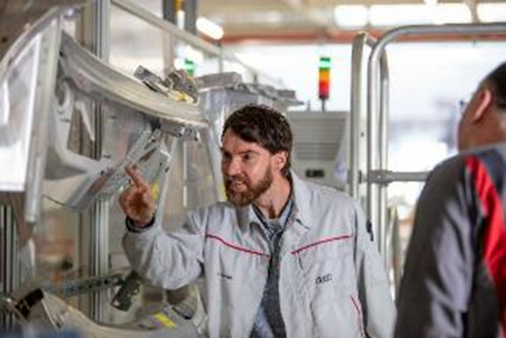
Local cleaning with plasma is the solution
Treating surfaces with Acerios hot active plasma (HAP) technology from Fronius has many advantages. Using a stream of shielding gas, the arc plasma is formed into a flame with a core temperature of up to 1,000° Celsius. This triggers thermal and chemical processes which ensure that material surfaces are locally cleaned of organic residues and film impurities with pinpoint accuracy. At the same time, the surface is activated. With Acerios, the arc is created between the plasma nozzle and the tungsten electrode of the welding torch, which means that a ground earth connection to the workpiece is not required. As a result, non-metallic materials can also be cleaned with hot active plasma.
“As with all new technologies we decide to look at closely, we tested Acerios to determine its fitness for purpose, the welding variables, and possible parameter windows. Together with Fronius, we then quickly and selectively optimized the prototype for series use,” says Rudolph. “Our system planners and colleagues from production then set about identifying a favorable installation situation.”
The technicians responsible for the A8 line finally decided to use Acerios in a robot cell that had enough free downtime to clean two areas measuring 12 cm² each. “This meant the available time was even sufficient to increase the Acerios burning duration to six seconds per welding spot. As a result, the distance between the welding torch and the workpiece is 30 mm. And we can then lower the current to 120 A without any loss of cleaning effect,” adds Jürgen Kolbenschlag, welding expert from the A8 body shop.
“This saves on wearing parts,” which Audi initially replaced after 10,000 cleaning points. It became apparent that the wear limits were far from being reached. The replacement cycle was therefore continually extended. By the middle of 2021, the wearing part limit had still not been reached – despite 25,000 cleaning points having been set.
Effortless integration
Integration of the hot-active plasma technology was made easier by the fact that the planners were able to install the Acerios PCT 2000 plasma torch in a stationary position. A minimal working area within the robot’s radius of action was sufficient for this. “What is more, the power supply needs less than one square meter of floor space, so we were able to place it well outside the cell between existing power supply units,” reports Rudolph.
The robot’s previously unused downtimes are used to convey the bulkhead to the welding torch. Accessibility to the workpiece is also very good thanks to the narrow torch, so that the plasma flame operates exactly vertically and is optimally aligned with the surface. Nor is it necessary to move down lanes during the cleaning process: the cleaning effect, which starts from the inside outwards, covers the whole of the required surface within the burning duration.
The fact that Acerios uses the inexpensive shielding gas argon also suited Audi. This meant that the existing argon ring main could be used to supply the MIG welding machines, thereby preventing any additional costs.
Audi also integrated the plasma power source – which is connected to the welding torch via a 6 m long hosepack – with ease, as Rudolph explains: “The interface of the Acerios system matches that of our Fronius MIG/MAG welding devices. Since this is part of the VW interface specification, we had no difficulty connecting the Acerios unit to the plant control system within one day.”
The setting and operation of the system are also largely based on those of the TIG power sources, as Rudolph confirms: “Anyone who can set a TIG power source can also work with the Acerios system. Operation is simple anyway, as only a few parameters such as amperage or burning duration need to be set.”
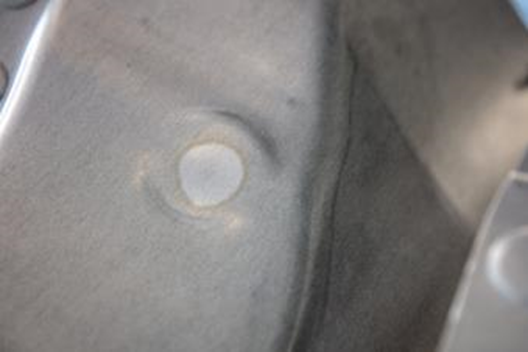
Reasonable cost of purchase and operation
The investments needed to deploy Acerios at Audi have turned out to be relatively low, thanks not only to the possibility of dual use of existing resources and various items of hardware. Moreover, Audi’s extensive experience with other Fronius power sources and their low maintenance costs was not the only deciding factor. Compared to other local cleaning solutions, Fronius’s HAP system is remarkably cheap to purchase.
For example, compared to laser-based systems, which require a basic investment of around one million euros, the Acerios configuration is many times cheaper. Including the associated automation system, the Fronius solution is in the mid five-figure range. What is more, no separate, shielded robot cell – as required by the laser system – is needed. Power consumption is also significantly lower compared to a cleaning laser. Acerios additionally requires about 15 liters of gas per minute.
Considerable savings are also achieved compared to the complex wet cleaning process normally used in the past, as Rudolph confirms: “We were able to reduce the cleaning costs per bulkhead by an amount in the lower single-digit euro range and at the same time increase resource efficiency without compromising cleaning quality. To achieve similar savings in vehicle manufacturing usually requires a lot more effort.”
Based on its practical experience of the system, Audi AG concludes that given the low operating and purchase costs, the use of Acerios pays off even with smaller unit quantities, but also in large-scale production. Moreover, Fronius HAP technology is particularly useful in confined spaces and for spot cleaning tasks that take a matter of seconds.
Acerios expands Audi’s technology portfolio
In view of these consistently good results, Audi has already integrated Fronius cleaning technology at another point: on a tunnel part, surfaces for four stud welds are also cleaned using HAP technology. “Acerios optimally expands the portfolio of technologies at our disposal,” concludes Rudolph. “Now, whenever we have to weld ground studs on thin-walled parts, this HAP technology is immediately shortlisted for the cleaning process.”