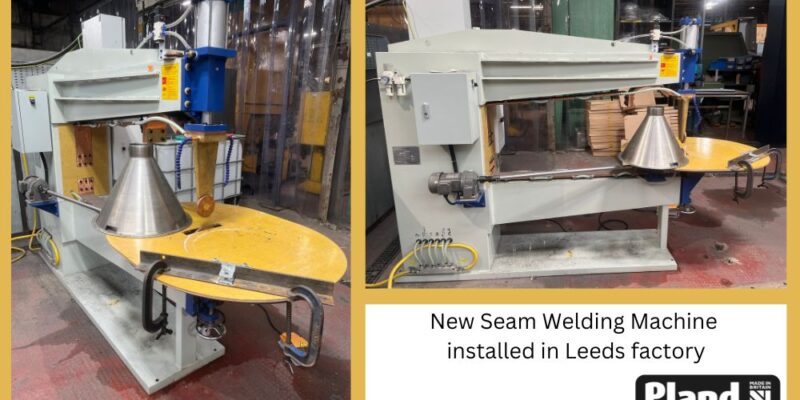
Leeds-based manufacturer Pland Stainless has invested in a new Seam Welding machine to help satisfy the growth in the demand for its stainless-steel commercial products.
The new seam welder uses a wheel-shaped electrode to form a continuously welded and leak-tight seam when fixing two stainless steel elements together. It is a powerful way to fuse metal sheets into one solid piece with a strong, continuous seam. It uses a special roller and electric current to achieve air and watertight welds.
The metals in this process “melt” together and join when an electric current is passed between the two wheels. The amount of current applied is crucial for a good quality weld. This method is especially important for making things where leaks could cause damage. As one of the largest UK manufacturers of commercial stainless-steel sinks, it is used here, for example, to assemble a flushing rim to a cone prior to further welding of the product into its finished surround. This new addition to the factory in Leeds will increase much needed capacity.
“We are constantly reviewing the machinery we have in the factory to ensure it remains current and helps our skilled workforce produce quality products safely and efficiently. The Seam Welder is just one machine in a long list that we utilise when manufacturing stainless steel products, and this new machine adds to the efficiency and capacity of the factory. Our Management team are always looking for areas where we can increase efficiency through investment.” Said Steve Duree, MD of Pland Stainless.