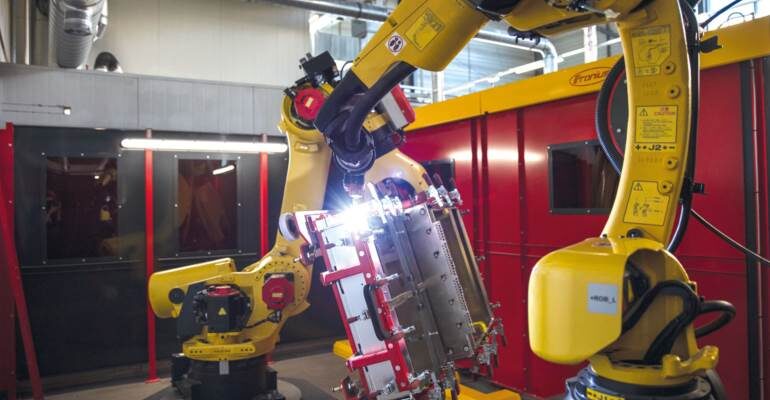
Fronius Solar Energy has been a pioneer of solar power from day one, continuously producing photovoltaic solutions. The latest inverter is the Tauro. With a Handling-to-Welding robotic welding system of the latest generation, tightly welded all the way round and intended for commercial use outdoors, it can withstand any weather conditions.
Its double-walled, actively cooled housing makes the Tauro ideal for use outdoors. Whether in rain, heat or direct sunlight, the inverter can withstand all weather conditions and perform to 100 percent of its capabilities. Developed by future-oriented solar experts, it satisfies international degree of protection IP65. These types of high-tech device are protected against contact, water spray from any angle, and the ingress of dust. “Due to the different sheet thicknesses, the challenges when it came to welding the aluminum housing were huge”, explains Jasmin Gross, Fronius Solar Energy. “With Fronius Welding Automation, we have the perfect partner in-house”.
First the simulation
The housing and swing doors are welded in a state-of-the-art “Handling-to-Welding” robotic welding cell that has been developed specifically for this job. “We program and simulate all robot movements and welding sequences offline with Fronius Pathfinder, i.e. away from the system on a digital twin,” explains Anton Leithenmair, Head of Welding Automation. “This enables us to detect any interference contours in advance. The same applies to axis limits and torch positions. Again here we can intervene early, without having to wait until the first welding samples. As soon as the welding sequences have been programmed, Pathfinder transfers the data to the post-processor, where it is translated into the language of the Fanuc robot. This allows us to save valuable time and costs. Offline programming shortens the robot teaching process in the welding cell by several hours!”
Workflow planning down to the minute
Before production begins, the Tauro selling orders are created in an Enterprise Resource Planning (ERP) system. They form the basis for material resource planning (MRP). This is where all production orders for housings and wing doors are generated. Next, a production date is assigned to every order. The detailed planning that follows is carried out by the Manufacturing Execution System (MES). Every order is planned down to the minute, assigned to a free order corridor, and then listed.
Perfectly coordinated: pre-tacking, setup, welding
Due to the different sheet thicknesses, the welding of the double-walled inverter housing posed a particular challenge from the outset. “Before we join the individual sheet elements in the robotic welding cell in line with standards, they are manually pre-tacked. We use the MAG welding process for this. Even at this stage, precise work is required,” says Christian Kraus, group leader in sheet metal production.
Once tacking is complete and this has been entered on the system terminal, the central system controls release the next step: robotic welding. The housing is now placed on the set-up trolley, clamped and moved into the lock. Once this has been acknowledged, the system starts the next job and the robot program responsible for positioning and welding is selected on the clamping device by means of an RFID (Radio Frequency Identification) chip.
“Regardless of which component we place in the lock, the RFID chip knows which welding program to use,” adds Kraus. “We can even place an inverter housing in lock one while welding a wing door in lock two via the component feeder. And vice-versa. The use of RFID technology enables us to weld components completely independently of their shape, size, and quantity. Whether it’s a batch size of 1 or series production – our Handling-to-Welding robotic welding cell can do it all.”