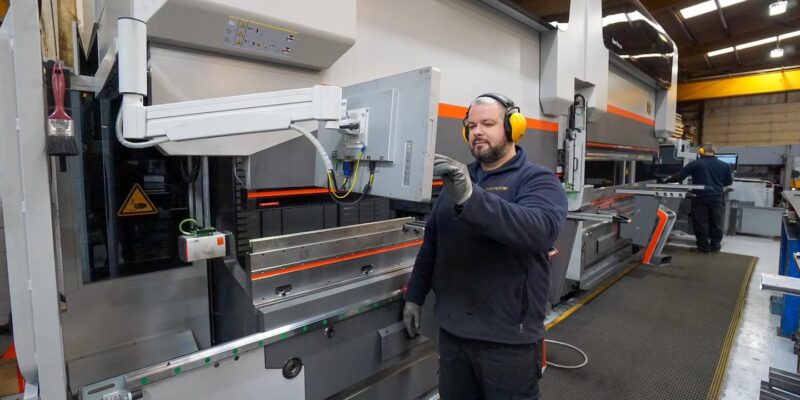
Econ Engineering has invested more than £500,000 in new machinery to process sheet metal used in the construction of its legendary gritters at its Ripon manufacturing base.
The Bystronic Xpert Pro press brakes are used for bending sheet metal. With the two new acquisitions, one of which is a 2500KN 3.1m machine, the other a 3200KN 4.3m machine, the firm will be able to press materials up to a length of 7.4 metres.
This latest investment comes on the back of the family-owned and run business – which makes more than eight out of ten winter maintenance vehicles on the UK’s roads – purchasing a £250,000 welding robot and the opening of a £7m engineering facility in Sowerby, Thirsk, which has now become home of Econ’s 1,000-strong gritter hire fleet.
These new presses are equipped with the latest pressure referencing systems, dynamic crowning lower beams, deflection compensation and bending technologies.
Alongside Bysoft CAM software (offline programming) and Byvision machine monitoring, this technology means that handling these machines is very simple for the operators.
The Bysoft CAM software allows the programmes to be created away from the presses themselves. The operators simply follow the on-screen instructions for setting the tooling and the bending sequence, making the operation far more efficient.
Jonathan Lupton, Econ Engineering’s Managing Director, said: “The purchase of these two new press brakes is a further demonstration of our commitment to investing in new technology within our manufacturing process.
“The opening of Sowerby has given us more space within our Ripon headquarters to accommodate the press brakes and the laser cutter, which help to boost efficiency and reduce waste.
“One of our strengths is being able to adapt our products to a customer’s individual specification, and this technical advancement will enhance our ability to craft each vehicle to meet their exacting needs.”