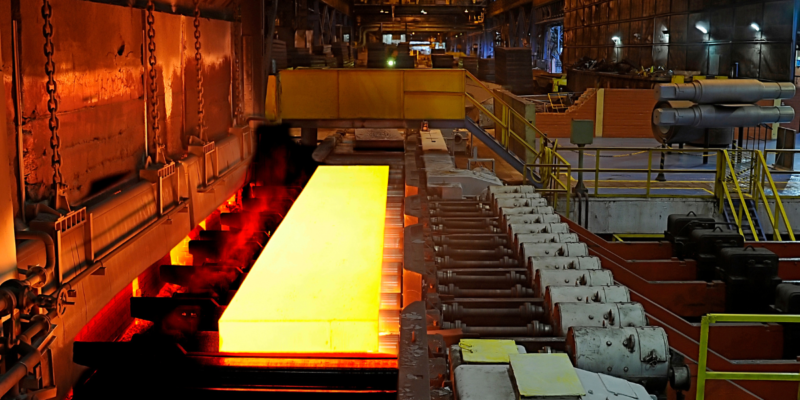
In the manufacturing industry, the quality of raw materials plays a crucial role in determining the final product’s durability, accuracy, and overall performance. One essential process that ensures the quality of these materials is metal flattening, a technique used to even out imperfections and achieve uniform thickness across metal sheets and coils. For steel mills and manufacturers, investing in high-quality metal flattening services is not just about improving product aesthetics but also about boosting efficiency, reducing waste, and enhancing the structural integrity of materials. Here’s a closer look at the key benefits of metal flattening and why it’s vital for UK businesses in steel production and manufacturing.
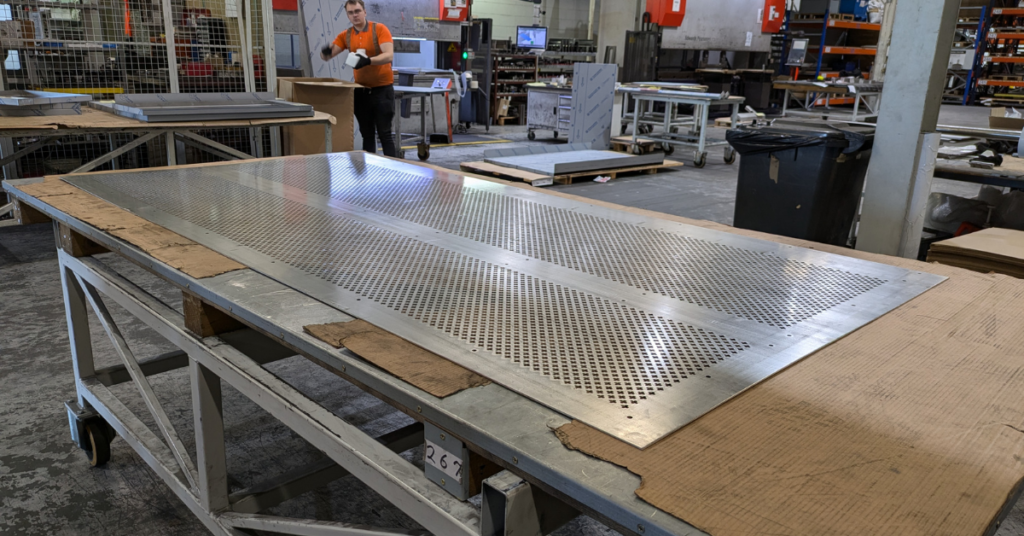
- Improved Material Quality
The metal flattening process is designed to reduce internal stresses and correct distortions during production or laser cutting. When sheets or coils emerge from the rolling mill, they often contain residual stresses that can lead to defects like warping, bending, or springing back when further processed. Flattening removes these imperfections, making metal easier to work with and less prone to structural issues later.
Flattened metal sheets are essential in automotive, aerospace, and construction industries—where precision and durability are non-negotiable. Properly flattened materials ensure that products meet exact specifications, reducing the risk of component failure or premature wear.
- Enhanced Production Efficiency
Efficiency is a priority in every manufacturing process, and metal flattening supports this goal by minimising handling time and reducing downtime caused by rework. Warped or uneven metal can cause jams, slow down automated processes, and increase the time and cost of manual adjustments. By investing in flattened materials, manufacturers can ensure that metal sheets and coils flow smoothly through production lines, optimising speed and precision.
Additionally, levelling and flattening equipment, such as that used by Wrightform, can handle various materials and thicknesses, offering flexibility to manufacturers who require different metal types and specifications. This adaptability streamlines processes and allows quick changeovers between production runs, helping to meet tight deadlines without sacrificing quality.
- Reduction in Waste and Material Costs
Reducing waste is an economic and environmental priority for manufacturers and steel mills. Flattened metal significantly reduces the likelihood of rejected parts, scraps, and production delays, all leading to wasted material and resources. By eliminating issues like rippling, bowing, or edge waves, metal flattening allows manufacturers to make the most of their raw materials, maximising yield and minimising unnecessary costs.
Studies have shown that companies implementing metal flattening in their manufacturing processes can reduce waste by up to 20%, leading to substantial savings over time. Metal flattening effectively reduces waste output and maximises every sheet or coil for steel mills looking to improve profitability and reduce their environmental impact.
- Better Product Consistency and Reliability
Consistency is critical when meeting regulatory standards, and flat metal sheets are far more predictable in performance than those with irregularities. Flattened materials are more reliable, with consistent thickness and flatness that facilitate uniform product quality across every batch. This consistency is essential for industries with stringent regulations, such as aerospace or medical device manufacturing, to meet strict safety and quality requirements.
This reliability extends to secondary processes like welding, coating, or forming. Flattened materials ensure more uniform results, making producing parts and products that meet precise tolerances easier. For steel mills and manufacturers alike, this consistency translates into a higher level of trust with clients, who can count on quality products every time.
- Improved Compatibility with Automated Equipment
Automation is the future of manufacturing, and metal flattening helps companies prepare for this shift. Many modern manufacturing facilities use automated systems to cut, weld, form, or assemble metal components. However, for these systems to work efficiently, they require materials free from defects and consistent dimensions.
Flattened metal sheets provide the precise tolerances required for automated equipment, reducing the risk of malfunctions, misalignments, or production delays. As automation becomes increasingly central to manufacturing, particularly in high-volume sectors, the importance of high-quality, flat materials will continue to grow.
- Cost Savings on Maintenance and Downtime
Manufacturing equipment can be susceptible to wear and damage when processing warped or irregular metal. Uneven materials strain machinery, leading to more frequent breakdowns, repairs, and associated costs. Flattened metal reduces the risk of these issues, as machines experience less resistance and friction during operation.
Metal flattening contributes to lower operational costs and longer machinery lifespans by minimising equipment wear and the need for unplanned maintenance. For high-capacity facilities like steel mills, where even a short downtime can result in significant losses, the cost savings associated with metal flattening can be substantial.
- Sustainability and Environmental Impact
Sustainability is a growing concern for businesses across all industries, and the steel manufacturing sector is no exception. Metal flattening supports sustainability by reducing waste, improving material utilisation, and lowering energy consumption during production. Flattened metal minimises reworking and allows for smoother, more energy-efficient processing, contributing to a smaller environmental footprint.
For UK manufacturers aiming to meet strict environmental regulations, metal flattening can be essential in reducing carbon emissions and promoting responsible resource management.