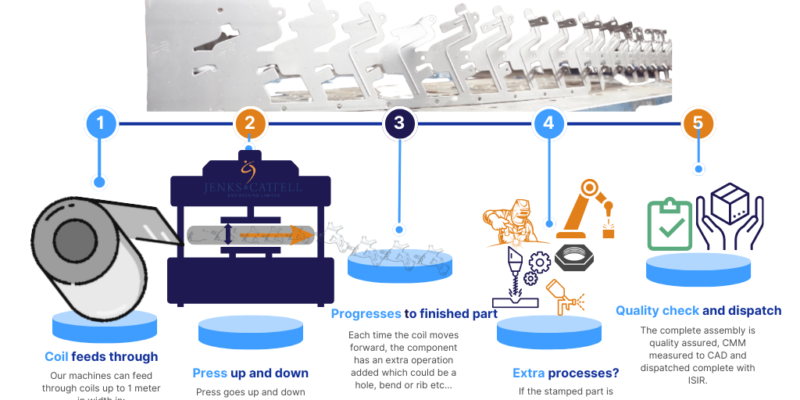
Jenks & Cattell Engineering have been using the progression stamping / presswork method of manufacturing sheet metal components for over 100 years, and are considered market experts.
What is progression stamping?
It is a metalworking method which can produce mid-high volume complex and precise metal components in a fast and cost-effective way on a strip of sheet metal that is fed from a coil.
It involves using a series of stations in a single tool, each performing one or more operations as the metal coil is fed through progressively until the finished part is cut off from the strip and coming off the press in seconds.
Progression stamping can perform various operations including punching, coining, bending, shaving, and embossing, strengthening.
Some of the advantages of progression stamping are:
- The production cycle time is reduced, and the output rate is increased = more parts made quickly and more cost efficiently.
- The production cost is lower as less material is wasted and less manual handling is required.
- One part can be produced in a matter of seconds with multiple operations being performed simultaneously and progressively.
- The quality of the component is repeatable, consistent, and accurate.
- The designs can be complex, with the tool being designed bespoke for one component, or left-right handed if applicable. It can create a complete customised shape and size of part to customer CAD.
- The unit cost of the component is very low, often pennies compared to other methods.
Does progression stamping save money?
If you are manufacturing more than 5,000 components a year, as a rule of thumb you will save money after 1-year after the initial tooling investment.
We can quote multiple manufacturing methods to ensure you have the most cost-effective route, for example laser cut fabrication will be best if there is not a budget for tooling.
Some of the disadvantages of metal stamping are:
- Presswork / stamping is not suitable for prototypes and low volume as the tooling investment is too great. To overcome this challenge, Jenks & Cattell Engineering offer alternative pre-production manufacturing methods including soft prototype tooling, laser fabrication and CNC machining which can cater to different customer needs and specifications.
- Tool making is essential. This is a relatively large (£10k-£100k average) investment, and it can take up to 16 weeks to begin production. Laser cut fabrications can be instant.
Is presswork / stamping the best manufacturing method for your project?
- Are your volumes higher than 5,000 components – Yes
- Are your components similar (left-handed/right-handed) – Yes (save money on only procuring one tool)
- Do you have a budget for tooling? Yes
- Do you want a lower unit cost per component? Yes
- Do you want your initial components manufactured within days? No (tooling is 16 weeks)
- Do you want to manufacture thousands of complex metal parts within minutes? Yes
- Are you at the prototype stage? No (we can assist with prototype tooling and laser cutting instead)
- Do you want the very best quality, with repeatable and consistent components? Yes
Our history in this industry dates back to 1886, and we are home to an impressive range of progression presses, transfer lines and single action presses up to 1000 tonnes to manufacture mid-high volume stamped components for various industries. We also offer laser fabrication, manual and robotic welding, CNC machining and assembly services to provide complete solutions for customers.