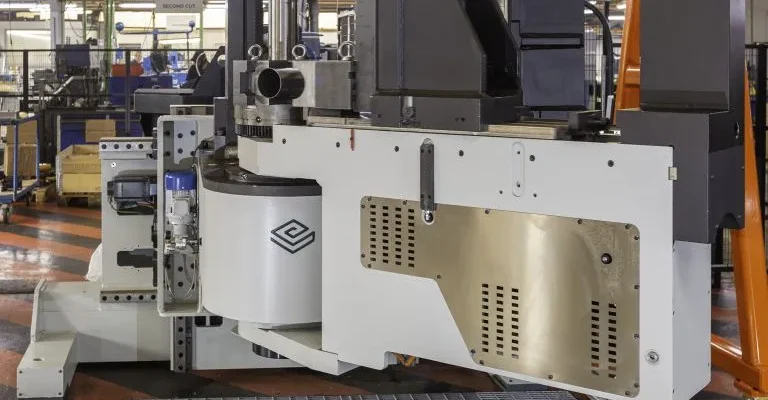
When it comes to bending large diameter tubes, it is usually necessary to use tube elbow joint sections to fabricate the bends on any tubes over three inches in diameter.
This can not only lead to an increased cost of parts, but is also results in a higher risk of leaks because of the number of welded joints required.
However, there is a solution to this problem, and it comes in the form of the BLM Elect 150 CNC Bending machine.
The BLM Elect 150 is a serious of piece of kit, 18 tons of kit to be precise. It is leaner, meaner, and greener, and it is a revolutionary solution for large diameter tube bending.
The BLM 150 makes the process of producing large diameter tube assemblies leaner as it can bend anything up to 6 inch diameter tube with wall thickness up to 3.5mm. The output of bending large diameter assemblies has increased from 1 to 15 parts per hour for a CNC bent tube compared to a fully fabricated tube assembly.
The full CNC bending of tubes also helps improve the quality and integrity of a part as it massively reduces the number of welds and therefore potential leak paths on an assembly. This improvement in quality makes for meaner PPM numbers compared to a fabricated route, and this in turn makes for a happier customer.
An example of how the BLM 150 has improved products for a customer are some 5 inch diameter Charge Air pipes that we manufacture for a customer. The parts were originally designed with three elbow sections for the bends along with some other fittings and a flange plate welded to the tube end. There were previously 21 welds on these assemblies which have been reduced to 9 due to the switch to bending the tube with the BLM 150.
The high number of welds meant that the parts had a Not Right First Time rate of 95% when leak tested underwater, these failure rates required significant amounts of additional welds to remove the leaking joints. However, since we have switched to bending on the BLM 150, the Right First Time rate has increased by 75%, meaning less re-work, better products and reduced costs.
Finally, being an all-electric machine it is greener as it uses less energy than either traditional hydraulic bending machines and the fabricating of welded elbow joints on large diameter tube assemblies. The BLM Elect 150 uses the latest energy efficient motor and operating systems to save costs as well as helping to be a more sustainable bending process for the future.
In summary, the reduction in processing time, the reduction in fabricated joints, and reduced energy consumption result in parts with lower cost, faster processing time and to a better quality standard.
The BLM 150 bender makes leaner, meaner, and greener large diameter tube assemblies.