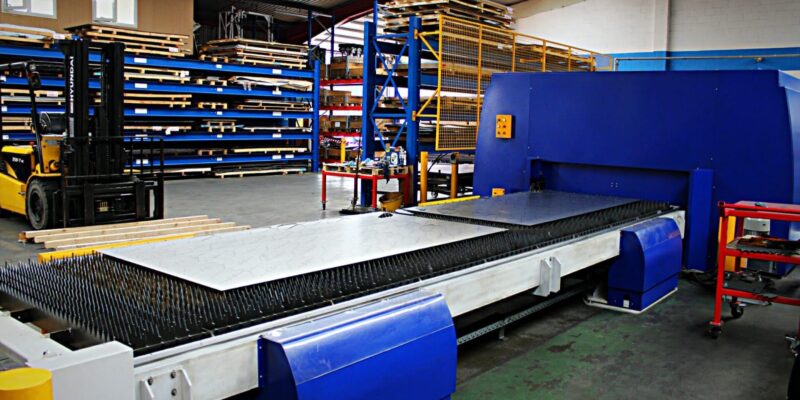
Mace Industries specializes in the design and manufacture of conveyers, roof loaders, elevators, hoists and soil and aggregate screeners for the construction industry.
These products were designed by the company to fill a need for a faster, simpler and less labour intensive way to get tiles to scaffolding at roof level – avoiding potentially dangerous ladder work.
From the initial prototypes the range and capability of its products has considerably expanded and includes equipment that can lift passengers and materials up to heights of 100m, conveyers that can work at an angle of 50 degrees and move up to 110 tons per hour and the latest version of its popular Bumpa product for roof loading which can operate at 65 degrees with a 10m reach. Now, the machines are also used in other sectors such as warehousing and are very popular with equipment hire companies.
To manufacture these products, Mace Industries has its own manufacturing 24,000 sq ft facility in Corby, Northants where it makes the components for its machines and also carries out laser cutting and folding operations opening up its capabilities for other 3rd party customers.
John Honan, Laser and Fabrication Department Manager, says, “For conveyer manufacture we have a Microstep fiber laser which can cut sheets 6m x 1.5m which are needed in our products. We can offer this unique capability to other customers that need to make large parts. Additionally, we have a Trumpf 5030 fiber laser and we can fold components up to 4m long.”
Mace Industries chose Lantek following a recommendation from another Laser cutting manufacturer and installed the software at the end of 2020. It now has three Lantek Expert systems for programming its laser cutting machines, three Lantek Integra ERP systems for managing its quotations, one Lantek Manager for its shop floor management and a link to its Sage accounting software for an inventory of material in stock.
Typically, Mace Industries generates 3-4 quotations per day for 3rd party customers with quantities of parts varying from 1 to 400, offering a niche service to a bespoke and creative market where quality and service are the most important factors for its clients.
Since the introduction of the Lantek software the parts for all the company’s conveyors, elevators and screens have been reprogrammed in Lantek Expert, which was a big task due to the thousands of different components involved. John Honan says, “We can now easily switch parts between machines which gives us extra flexibility during production.”
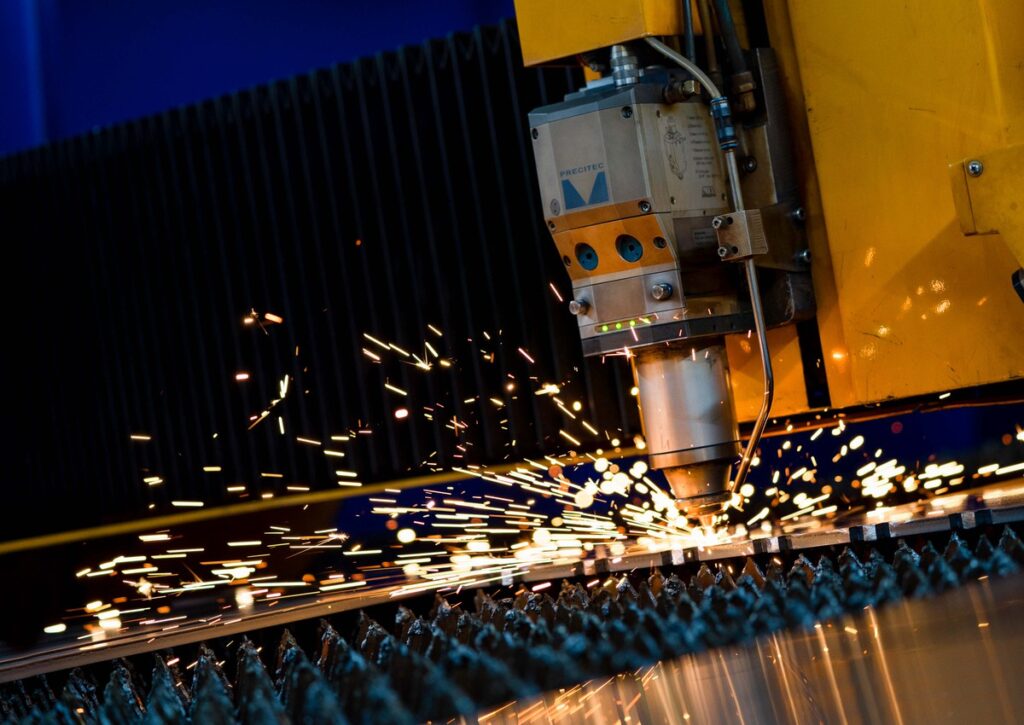
He goes on to describe the process for a new customer. “We ask the customer to send us their design in a compatible CAD format. We can then check and verify the drawing in Lantek and establish the details of the material, the in-house processes for manufacture as well as the external processes required such as powder coating. Within the system we have the latest material prices and, using Lantek, we can nest parts to find out the exact quantity of material required and the time taken to cut the parts. All the processes both internal and external are attached to the part in Lantek Integra, so if the part needs a redesign or material prices change we can quickly overwrite the old information and generate a new quotation.”
When a quotation turns into an order, all the processing information attached to the quotation passes to Lantek Manager and then automatically to Lantek Expert where a mixture of parts are nested together according to material type and thickness.
John Honan concludes, “We use Lantek exclusively now to produce quotations and for nesting and cutting parts for Mace Industries products and for our 3rd party customers. The ease of generating and amending quotations and the simplicity and flexibility of sending jobs for manufacture is very important to us. Lantek’s software makes all this possible.”