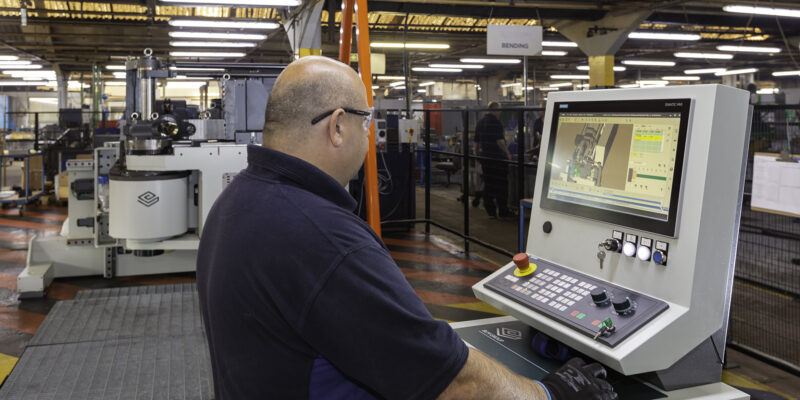
With the acquisition of Malvern Tubular Products and Maxpower Automotive from Tricorn UK towards the end of 2021, the Lander Group created the opportunity to continue its development as a single source of supply for tube-based assemblies.
Now, under the branding of Lander Tubular Products, and with the latest investment in BLM tube bending equipment, the group has the capability to provide automated tubular solutions from 4 mm through to 152 mm diameter in a range of materials, including steel, stainless steel and aluminium.
With a two-year facility uplift investment plan in place the decision was taken to initially bring the systems and processes of the two new group facilities, as well as those at their sister plants in the USA, in line with Lander’s head office facility in Birmingham, UK. With that process well under way the time was right to start the investment in machinery.
“When Lander Group acquired Malvern Tubular Products and Maxpower Automotive, it was evident that they had suffered from a significant lack of investment in capital equipment over recent years. Our vision is to update all of our facilities, within the constraints of the current economic climate,” says David Alexander, Sales and Marketing Manager, Lander Tubular Products.
The first major investment as part of that plan saw the arrival of a BLM ELECT 150 All-Electric CNC Tube Bender arrive at the Malvern facility. With capacity to bend tube up to 152 mm (6”) diameter, with added efficiency delivered by the multi-stack tooling system where up to eight tool sets can be mounted simultaneously, the BLM ELECT 150 will add to the group’s overall capability and allow further expansion of its growing customer base.
“At Malvern we focus on lower volume production of larger tube diameters, often with higher complexity of bends, mainly for the off highway, construction and power generation industries, with the new BLM machine we can look to expand into new market segments with our fully finished tubular products.”
Given the scale of the BLM ELECT 150, some 18,000 kgs, this puts Lander Tubular Products in a strong position to win new work by combining its now extended bending capabilities with its existing customer support for design, prototype development through to full production.
While large scale, the machine is extremely versatile and brings greater control to production through its control system. BLM’s software systems ensure that quality, repeatability and right-first-time every time are guaranteed, which will be invaluable in the low-volume environment at the Malvern facility.
Aiding that quality promise is the ability to utilise the machine’s variable torque system that allows torque to vary between 2 and 6 metric ton to eliminate part deformation, even on tight radius bends and, the surface finish of the tube is maintained to the highest levels. Control is via a Siemens Simotion control, which in conjunction with BLM’s proprietary VGP3D programming and 3D simulation software makes set-up and operation efficient as well as being able to generate accurate cycle time estimates.
“We see many positives in the arrival of the BLM ELECT 150, and with many other BLM machines within the group we already have a good understanding of how to maximise their potential. This new machine will add to our lower volume, high complexity work at Malvern through consistent quality, reduced potential leak paths by eliminating the need to fabricate, cut and weld larger diameter tubes, reduced process times and the confidence we have from our experience of BLM,” says David Alexander.

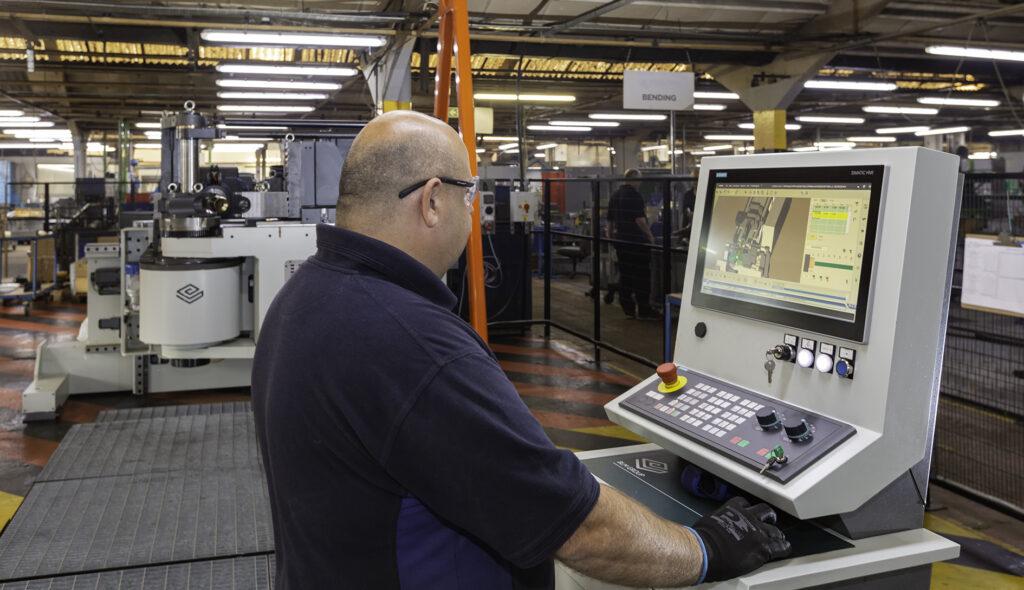
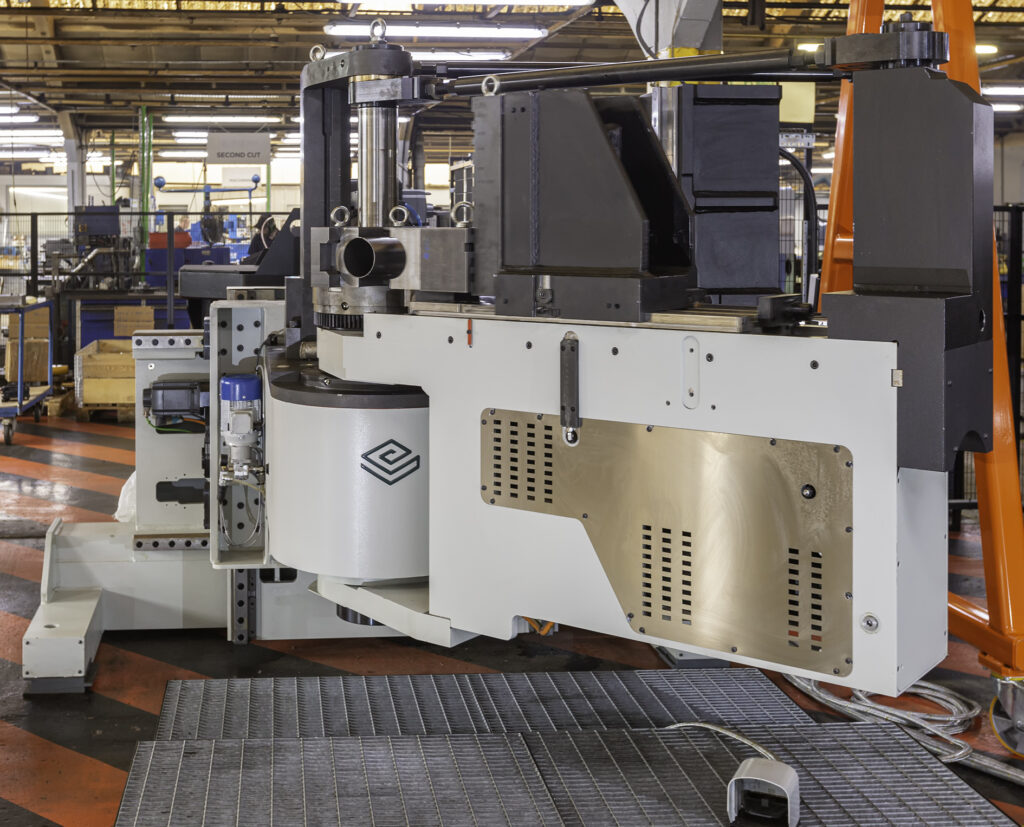
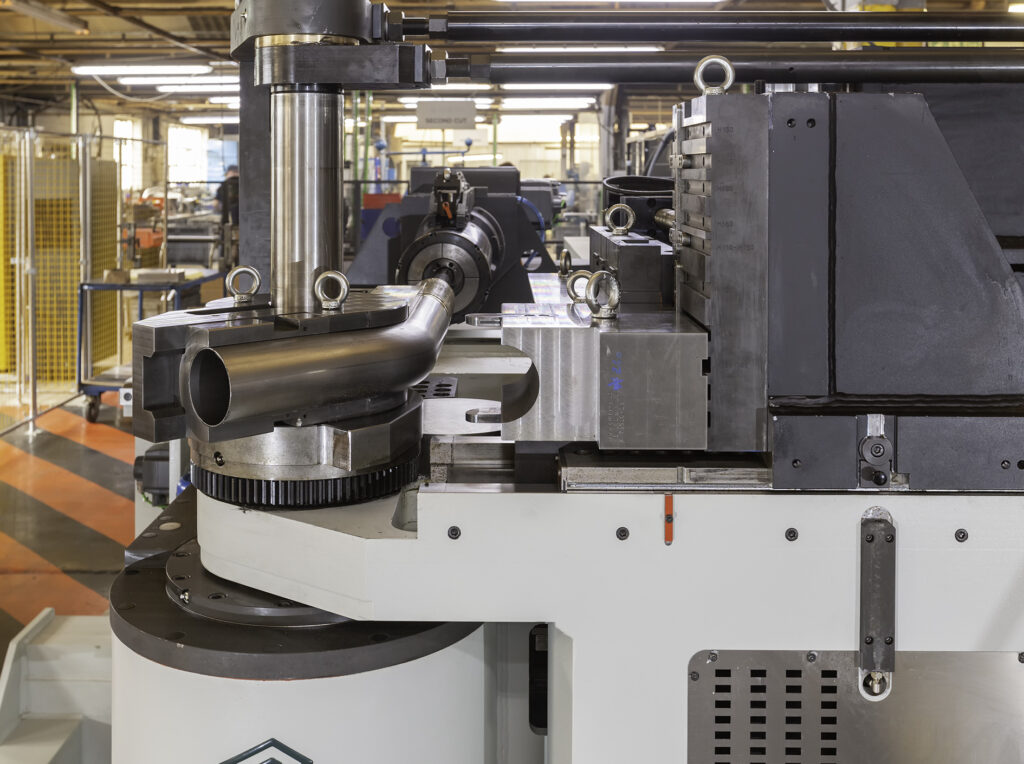
The BLM ELECT 150 all-electric bender installed at the Lander Tubular Products Malvern facility will enhance product quality and production efficiency while allowing the business to expand its customer base.