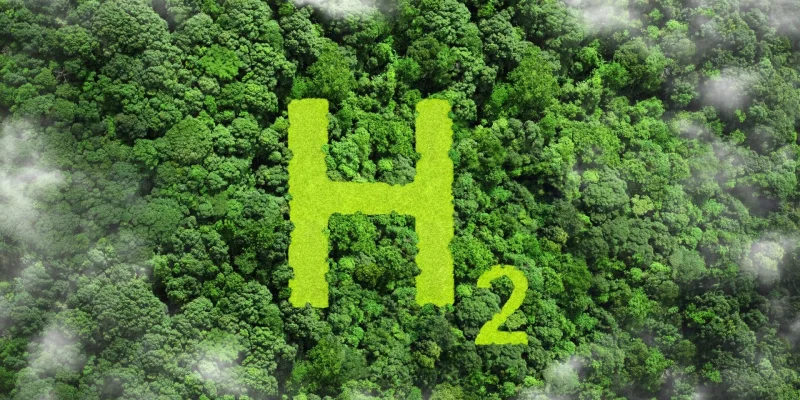
A large portion of the world’s steel is currently manufactured using the traditional blast furnace-basic oxygen furnace (BF-BOF) method. This conventional steelmaking process heavily relies on fossil fuels, primarily coal and coke, making the transition to non-fossil fuel alternatives a crucial step for reducing carbon emissions. But is there a greener alternative?
One approach to decarbonising the steel industry involves using hydrogen and steelwork companies adopting a fossil-free fabrication process. In this method, fossil fuels are replaced with green hydrogen, which is generated from renewable energy and water, leading to a substantial reduction in CO2 emissions.
Besides hydrogen, another strategy for reducing carbon emissions is to use fossil-free electricity. The reduction process can be customised based on hydrogen and fossil-free electricity availability, incorporating a mixture of hydrogen and natural gas in scalable ratios. This H2/NG mix can achieve significant CO2 reductions compared to the traditional steelmaking process.
The Green steel process results in almost zero CO2 emissions, in stark contrast to the current steelmaking practices that account for over 7% of worldwide carbon dioxide emissions. This significant impact makes decarbonising the steel industry and fossil-free fabrication a top global priority.
What is Green Steel and How is it made?
Green steel aims to produce steel in a more environmentally sustainable manner, thereby lessening its climate impact. This can be accomplished through several strategies, including minimising the use of carbon-based reducing agents and fuels during pelletising and transitioning from the blast furnace method to electric arc furnaces that utilise steel scrap and direct reduced iron and are powered by renewable energy. Additionally, converting from fossil-based fuels to hydrogen or electricity in downstream processing plays a crucial role. Fossil-free fabrication is the future and the production of greener steel won’t compromise on the quality.
The idea of green steel aligns with a broader initiative towards more sustainable and eco-friendly industrial production practices.
Greens steel is produced with methods and technologies that aim to reduce the impact of traditional carbon emissions in the steel industry.
Renewable Energy Sources & Greener Practices
- Wind
- Solar
- Hydropower
- Using Hydrogen
- Steel recycling
- Minimising steel waste
- Carbon capture and storage
- electric furnaces are cleaner technologies
- sustainable mining as a transition to a greener future
At Staffordshire Fabrications we take responsibility for improving our practices and aim towards green production in the years to come; with fossil-free fabrication becoming a practice that will be necessary as soon as possible. We invest time and training into a fossil-free future in multiple ways such as recycling steel, reducing waste with bespoke measurements and working with companies that also have more environmental plans for their projects. We invest in technologies that are state-of-the-art and are always in the loop on production news and improvements.
The Role of Hydrogen in Green Steel Making
Staffordshire Fabrications understands the necessity of renewable energy and the essential transition needed to reduce the impact of steel fabrication and making on the environment. Nature’s most plentiful element, hydrogen, can be harnessed as a clean energy source through green hydrogen production. Unlike coal and oil, this method only releases water vapour, leaving no harmful residue in the air. Therefore fossil-free fabrication is in sight! But are there any cons to this new practice?
Advantages and Disadvantages of Green Hydrogen
Pros
- Clean: Green hydrogen produces no polluting gases during production or use, unlike fossil fuels which emit harmful emissions.
- Storable: Hydrogen can be easily stored, allowing for later use when needed, independent of production times.
- Versatile: Green hydrogen can be converted into electricity or synthetic gas, making it adaptable for various applications in commercial, industrial, and transportation sectors.
Cons
- Cost: Currently, green hydrogen production is expensive due to the reliance on renewable energy sources for electrolysis.
- Energy Consumption: The process of producing hydrogen, even green hydrogen, requires more energy input compared to some traditional fuels.
- Safety: Hydrogen is highly flammable and volatile, necessitating extensive safety measures to prevent leaks and explosions.