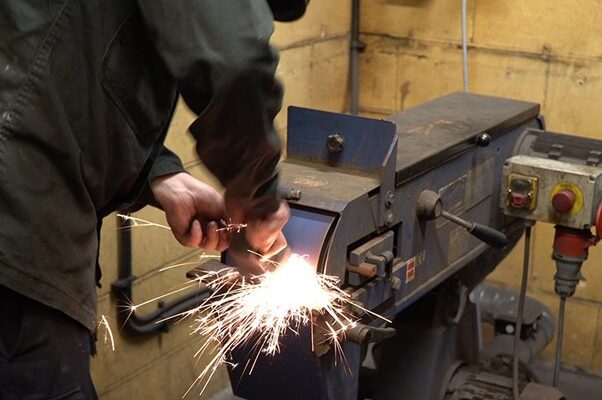
The National School of Blacksmithing, based in the Rural Crafts Centre at the Holme Lacy Campus of HLNSC (Herefordshire, Ludlow and North Shropshire College), is a provider of a wide range of Post-16 study options in Herefordshire, including an impressive; industry-leading set-up for Blacksmithing, Farriery and Welding / Fabrication based courses.
Speaking to Josh Masey, the Rural Crafts Centre Technician, about the various pieces of machinery supplied by Selmach Ltd over the years, including their Guillotine, Linisher and most recently, a new Sterling Bandsaw.
“When being quoted through Selmach, they gave us a very competitive price against other suppliers; they were very professional.”
The College has a large collection of equipment from Selmach from over the years, including Sterling & Bianco Bandsaws, Morgan Rushworth Sheet Rolls, Meyer Pillar Drills, a Steelworker, and a Morgan Rushworth Press Brake, with a Morgan Rushworth Guillotine being their most recent addition.
How did you hear about Selmach and why did you choose them?
We heard about Selmach through previous purchases through the College. We had a Guillotine off Selmach and we’ve had various other machines like drill presses and sheet metal croppers and linishers.
Why were you looking for new machinery?
The reason behind the saw we had an investment off the Vaughan Nash Trust, which is a trust through the College which is usually give to students every year. But unfortunately due to Covid the previous years, they weren’t given it. So this year, it’s been invested back into the department, and we decided to buy a few machines for that the students could use, and utilise state of the art machinery.
What impact has the machinery had?
The latest machine is a horizontal auto feed down bandsaw. The machinery is working out very well. Obviously, in the forging set-up, it’s very good because we can use it to cut up forged components and then vice versa in the fabrication workshop we can use it to cut some box up and some angle up. It’s been very versatile and diverse in both the blacksmithing and fabrication settings.
How was the experience with Selmach while ordering?
When being quoted through Selmach, they gave us a very competitive price with other suppliers, they were very professional and very outgoing. When being quoted for the saw, they never put any pressure on when asking for answer for the quote. It was very professional, very information procedure to go through. When I was in the initial stages of the process of looking to get a new piece of equipment for the college, I went down the show room and a had a look. One of the sales reps showed me around, and how the machines worked. It was just very professional and sort of almost like going around a car showroom looking to buy a car and seeing all the gadgets and all of that sort of stuff on the machinery, and what applications we would be using the machinery for. Then we came to decision of what we would be quoted on after that.
What about aftercare and service?
The aftercare and service through Selmach’s been very good. We’ve had instruction manuals for all of the machines, we’ve had outlining all of the potential problems or teething problems that may occur with the machine and we’ve also had engineers come out here when there’s been a problem and that’s usually been next day – so it’s been a very good service from Selmach.
Would you recommend Selmach and our machinery?
Yes. So anybody looking to purchase any equipment, I’d be more than happy to send them their way again because they’ve been very professional through the process of selling, quoting and aftercare and all that stuff as well. So yeah, I’ll be more than happy to send them their way.