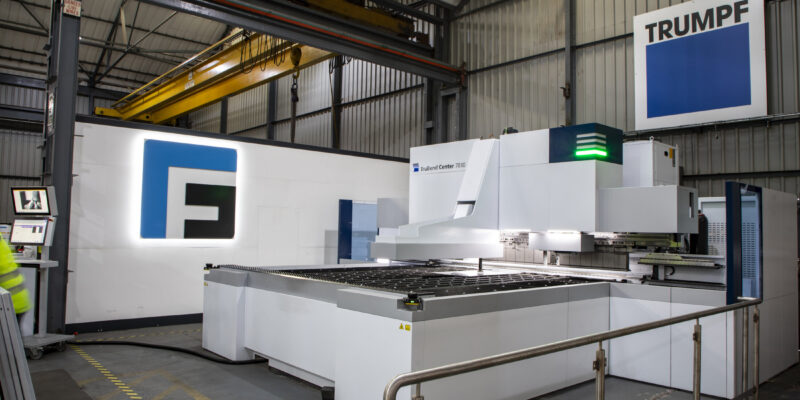
Genius Facades, a leading manufacturer of A1 non-combustible rain-screen façade systems, is taking its production capabilities to the next level by investing in a TRUMPF TruBend Center 7030 fully automated panel bender.
Adding to the company’s growing range of TRUMPF machines, the impressive speed and right-first-time capabilities of the new TruBend Center 7030 will help Genius Facades keep pace with rapidly increasing demand for its aluminium rain-screen façades.
With a fast-expanding order book, Genius Facades has been investing heavily in new manufacturing technology for its two purpose-built factories in the Midlands. Factories are the heart of Genius Facades: the company continually strives to innovate its manufacturing and fabrication processes, improve its capability and productivity, and offer lead times that match the expectations of its clients. This progressive manufacturing business saw the acquisition of a new panel bending machine as the next step in the evolution of its production proficiency.
“We were keen to expand our in-house manufacturing capabilities to keep up with rising customer orders for our A1 non-combustible rain-screen facades,” confirms Richard Bland, Production Director at Genius Facades. “We looked to TRUMPF in the first instance due to our long-standing and successful working relationship.”
In 2022, Genius Facades installed a TRUMPF TruPunch 5000R XL punching machine and a TRUMPF TruBend 5170 press brake, adding to a long line of TRUMPF models at the company. Indeed, Genius Facades even has a 21 year-old TRUMPF punching machine that is still fully operational, speaking volumes about the reliability and longevity of this industry-leading brand.
“We knew that investing in a fully automated panel bender such as the TRUMPF TruBend Center 7030 would significantly increase our bending speed and offer excellent automation capabilities,” states Mr Bland.
Panel bending is ideal for complex bending applications with radius bends, short sides or narrow profiles. The bending frame of TRUMPF panel benders comprises a C-profile mounted with the lower and upper bending tools. Upon bending the sheet metal, the profile moves up or down and performs a small elliptical movement, known as the swivel. Speed and flexibility are the main characteristics of panel benders, especially when handling small-to-medium batch sizes. Panel benders are also suitable for productively bending a component’s different radii sizes using the same tool.
The TRUMPF TruBend Center 7030 panel bender offers automatic part loading and unloading for forming panels up to 3m in length. The machine features both rotary and two-axis part manipulators.
Using the rotary part manipulator, the TruBend Center 7030 can bend components fully automatically. The manipulator secures and rotates the sheet into the required position. Here, axis speeds of 3,000 mm/s make it possible to increase productivity significantly. When it comes to positioning smaller parts, the patented two-axis part manipulator also comes into play. Synchronised interaction of the rotary and two-axis part manipulators allows what is for fully automatic panel bending an unusually large degree of freedom to shape components.
Another impressive feature of the TRUMPF TruBend Center 7030 is its ACB (Automatically Controlled Bending) laser measuring system, which ensures precise angles for a first part/perfect part approach. Sensors determine the actual angle together with the spring-back and guide the ram to achieve the desired angle.
“Ultimately there were many reasons why we returned to TRUMPF for our new panel bender,” concludes Mr Bland. “Top-quality machinery is the obvious one, but TRUMPF’s excellent customer service, dependable delivery and fast system assembly were also primary factors in our purchase decision.”