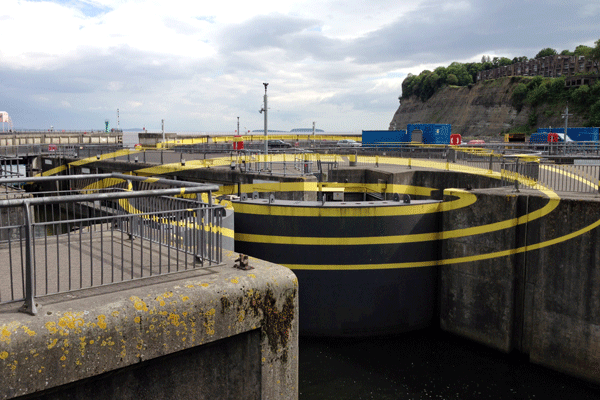
When Technocover were asked to design secure access solutions for the Cardiff Bay Barrage the Technical Team soon realised that more than standard galvanised steel access covers would be required for this project.
The Cardiff Bay Barrage is 1.1km long and extends from Cardiff docks in the north to Penarth in the south. The major £220 million civil engineering construction project subsequently led to the formation of the Bay and was the catalyst for the £2 billion regeneration of the old docklands areas of Cardiff and Penarth. The Barrage features locks and bridges, sluice gates and a fish pass as well as a landscaped embankment area.

At the centre of Barrage operations, a control room is staffed 24 hours a day, 365 days a year by a team of operators, lock managers and engineers and is the main point of contact for boats navigating to and from Cardiff Bay.
There are three locks on the Barrage; each one is 40m long, two are 8m wide and one is 10.5m wide. They allow boats to navigate between the Severn Estuary and Cardiff Bay. Each lock can accommodate up to 10 average sized vessels, with passage through the locks taking between 5 and 20 minutes, depending on the tide.
Each lock has a bascule bridge weighing approximately 88 tonnes. As the estuary has a high tidal range, the sector lock gates are up to 16m high to enable the boats to pass through at all stages of the tide.
When the locks are closed, they allow passage over the Barrage structure for pedestrians, cyclists and vehicles.
There are five sluice gates that control the level of water in the Bay. The sluices are used to either allow flows from the rivers Taff and Ely to exit into the Bristol Channel, or to create a barrier to stop the high tide from entering the Bay. Over a quarter of a million litres of water per second can flow through each gate, which is 7.5m high and 9m wide.

Technocover – Providing Access and an Emergency Escape Solution
In 2018 Technocover were contracted to design and manufacture four purpose made flush fitting access covers to be installed within the paved, public trafficked, areas close to the Bascule Bridges on the Barrage. Three of the four hatch covers were specifically required to provide secure plant access, however, in addition to providing a controlled access solution, all, including the fourth hatch, were required to provide safe exit routes for inspection and maintenance personnel working within the Barrage and its main internal gallery shafts, even if closed and locked from above.

The Solution … By incorporating an external locking system compatible with internal emergency escape hardware, access from above could be controlled and facilitated via a turn-catch hasp and staple padlocking entry system and from below this would be overridden by a single lever handle, providing efficient exit from inside the chamber shafts, especially in an emergency situation.

Standard hinged, flush fit access cover features:
- Hidden holding down anchor points to maintain secure location of frame with paved area.
- Single BSI sealed lifting keyhole in left-hand side of cover.
- Recessed padlock with hinged anti-trip locked down cover plate with loading identification.
- Stainless steel torsion sprung lid to provide a single person operation to conforming to Health and Safety Executive directive for manual handling.
- Hidden hinges – protected against damage from vehicle loadings and ingress of grit, etc.
- Cover lid opens 95 degree for safety and unobstructed access to chamber shaft.
- Hand operated auto safety stay to hold hatch lid in open position.
- Wide sealing strip to underside of cover lid, preventing damage to seal when cover is open.
- C250 load strengthening underbracing to underside of hatch cover.
- All mild steel is hot dip galvanised after manufacture to BS EN ISO 1461 as standard.
Enhanced product features for the Barrage project:
- Internal emergency escape hardware – single lever handle exit locking system that overrides the external hasp and staple pad-locking device.
- Grab handle to underside of cover lid to assist exit of the chamber.
- Moated drainage channel frame design with twin drainage pipes to allow water build up from inside the frame to drain down into chamber sump via top connection pipe and drain tube to the base of shaft.