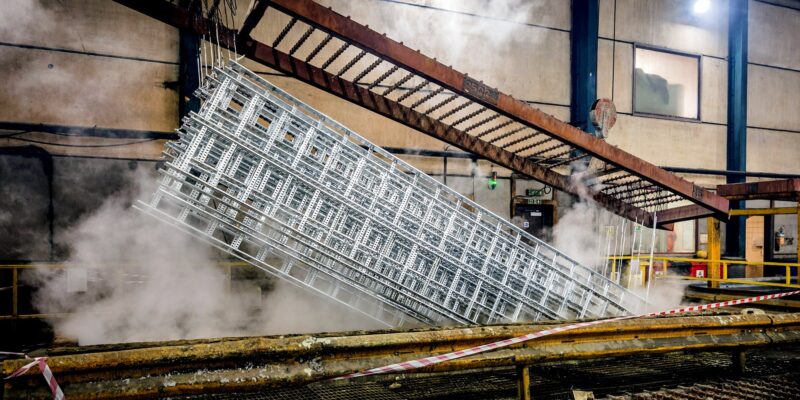
Corbetts galvanises 100 tonnes of steel daily, which is no small feat. To put this into perspective, that’s the weight of approximately seven modern aircraft carrier anchors in just one day!
Anchors, often made from cast or forged steel, can weigh up to 13.4 tonnes each, so you can imagine the magnitude of steel Corbetts processes in a single shift!

Stringent systems and best practices
These results are a testament to the team’s efficiency, dedication, and years of honed expertise. On especially productive days, Corbetts have reached 120 tonnes of Galvanised steel across its two galvanising kettles, ready for installation across various industries. This level of output is made possible by the company’s stringent systems, best practices, and the seamless operation of their dual dip tanks. With the team working a smooth double shift, Corbetts maintain this impressive pace day in, day out.

So, how do Corbetts consistently output 100-120 tonnes of high-quality galvanised steel every day? It all comes down to a combination of hard work, precise processes, and acute organisational systems. The team’s double shifts ensure continuous production, all while maintaining excellent communication across departments to keep everything running smoothly.
Each stage of the galvanising process is meticulously planned and executed, with strict quality control measures in place. These practices, combined with the dedication of Corbetts’ skilled workforce, allow them to deliver exceptional results on a large scale.

Galvanising for vital infrastructure
But it’s not just the heavy-duty items like anchors that they handle. Corbetts’ daily output also equates to the combined weight of about 150 streetlights! Street lighting is a significant part of the company’s portfolio, and the ability to double-dip up to eight metres ensures a full, even coating of zinc protection for these vital infrastructure components. Corbetts’ system not only ensures durability, but allows them to meet the clients’ needs quickly and efficiently.
