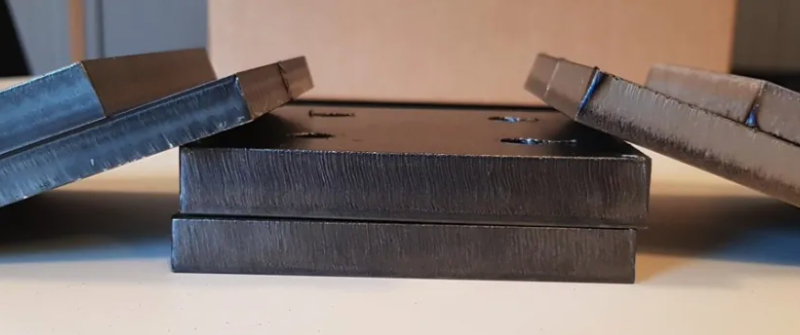
Laser cutting is a widely used manufacturing process where a high-power beam is used to laser cut or engrave materials. One critical aspect of this process is the choice of assist gas, which can significantly influence the quality and durability of the final product. In the context of laser cutting, the use of nitrogen as an assist gas is often preferred over compressed air, especially for applications where high-quality edges and long-term durability are essential, such as in powder coating.
SUPERIOR EDGE QUALITY WITH NITROGEN
- Reduced Oxidation: Nitrogen, an inert gas, prevents oxidation during the cutting process. This is crucial to laser cutting metal like steel, where oxidation can lead to weaker, less consistent edges. In contrast, compressed air contains oxygen, which can react with the material being cut, leading to oxidised, lower-quality edges.
- Cleaner Cuts: Nitrogen assist gas produces a cleaner laser cut with a smoother finish. This is particularly important for intricate designs or when a high level of precision is needed. Compressed air, due to its composition, often leaves a rougher surface which might require additional finishing work.
ENHANCED DURABILITY FOR POWDER COATING
- Better Adhesion: When preparing for powder coating, the quality of the substrate surface is key. Nitrogen-cut edges provide a smoother surface that ensures better adhesion of the powder coat, leading to a more durable and consistent finish.
- Reduced Surface Imperfections: Compressed air can introduce surface imperfections due to its reactivity and the potential for introducing contaminants. These imperfections can affect the powder coating process, leading to inconsistencies and potential weak spots in the coating.
LONG-TERM RELIABILITY
- Resilience to Environmental Factors: A nitrogen-assisted laser cut offers better resistance to environmental factors like moisture and temperature variations. This is particularly important for components that are exposed to harsh or variable conditions.
- Consistency Over Time: Products laser cut with nitrogen maintain their integrity over a longer period, making them more reliable for applications where long-term performance is critical.
CASE STUDY: LASERED COMPONENTS, LASERED.CO.UK
We’re a prominent UK-based laser cutting service, exemplifying the preference for nitrogen over compressed air. At Lasered Components, we never use compressed air when the material can be laser cut with nitrogen, primarily due to the following reasons:
- Commitment to Quality: Lasered Components prioritises the highest quality in our cuts, understanding that the assist gas plays a pivotal role in achieving this.
- Client Satisfaction: We acknowledge that the superior edge quality and long-term durability afforded by nitrogen align with our clients’ needs, especially for applications requiring powder coating.
- Industry Standards: Staying ahead in a competitive industry, we adheres to best practices, including the use of nitrogen for laser cutting, to ensure that our products meet and exceed industry standards.
CONCLUSION
In conclusion, while compressed air may be a more cost-effective option, its use in laser cutting metal can compromise the quality and durability of the final product. Nitrogen, with its inert properties, ensures superior edge quality, better preparation for powder coating, and long-term reliability, making it the preferred choice for high-quality laser cutting applications. At Lasered Components, we understand these benefits and therefore choose nitrogen over compressed air for our laser cutting processes.