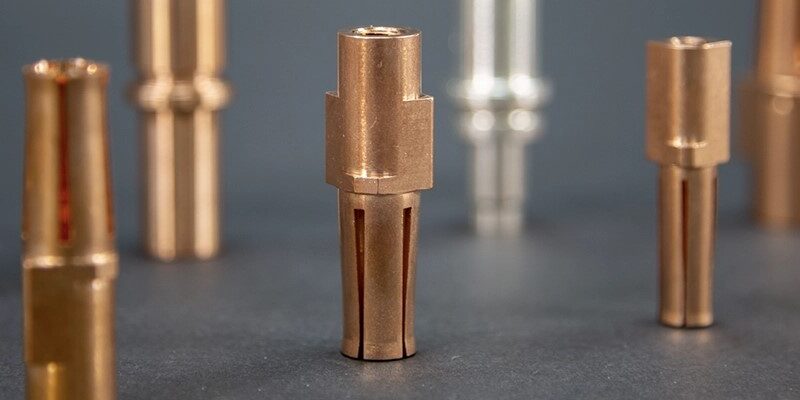
Cold forming continues to be a popular way of creating complex geometry metal components that maintain their dimensional accuracy. Over recent years, this technology’s growth has been driven by innovations in the process, a move to using lightweight materials in certain applications and increasing demand from the automotive, aerospace and electronics sectors.
The process of cold forming is suitable for all fields of application where harder metals and stronger yield strengths are required, including mechanical, plant, and apparatus engineering, automotive engineering, and electrical engineering. For cold forming, any metal that is non-brittle and that cannot be hot formed can be used, even if they are not suitable for hot forming. It is no surprise that cold forming technology continues to be a cornerstone in manufacturing, offering a unique blend of efficiency, precision, and strength for a wide range of applications.
Cold forming is an integral part of various industries. Among its benefits are improved material strength and surface finish, reduced waste, low energy consumption, and high-volume production. In addition to offering versatility, it provides environmental benefits such as reduced emissions and scrap metal recycling. Here, we will examine how cold-forming technologies can be used in different industries.
Automotive Industry
• Fasteners: Bolts, nuts, and rivets are commonly produced through cold forming
• Engine Components: Valve lifters, push rods, and various brackets
• Transmission Parts: Gears and shafts formed through cold extrusion
Aerospace Industry
• Fasteners: High-strength fasteners for assembling aircraft components
• Structural Components: Brackets and other small parts requiring high strength and precision
Electronics and Electrical
• Connectors: Electrical connectors and pins are often cold-formed for precision
• Terminals: Cold forming is used to produce a wide variety of terminal types used in electronics
Consumer Goods
• Tools: Wrenches, pliers, and other hand tools
• Appliance Parts: Small parts for household appliances that require precision and strength
Medical Devices
• Surgical Instruments: Precision parts used in surgical instruments and devices
• Implants: Certain types of medical implants can be cold-formed to achieve the desired mechanical properties
Building and Construction
• Fasteners: Screws, nails, and other fasteners used in construction
• Structural Components: Brackets, hangers, and other hardware
Industrial Equipment
• Bearings: Bearing races and other components requiring high precision and strength
• Hydraulic Parts: Components for hydraulic systems, including fittings and connectors
Cold forming excellence at Dawson Shanahan
Dawson Shanahan, have over 80 years’ experience in the cold forming of complex components for technical industries. In the aerospace industry, the company manufacture components for military and civilian aircraft, piston and jet engines, braking systems, undercarriage systems, flight surface controls, and cabin environment systems. Using the company’s precision cold forming and machining expertise to maximise performance and efficiency for engine, chassis, and drivetrain manufacturers in both automotive and commercial vehicles. Its services include design, prototyping, low- and high-volume production, project management, and single-source agreements aimed at reducing costs, lead times, and improving supply quality.
Precision engineering of electrical and electromechanical connectors is one of our specialties, along with cleanrooms and production facilities that comply with stringent medical industry standards. As a manufacturer of components ranging from simple connectors to advanced power distribution systems, the company can supply small batches or manage long-term or single-source supply contracts.
The company can create cold form parts in almost any metal, including copper alloys such as Zirconium Copper (CuZr), Tellurium Copper (CuTe) and Copper Chromium Zirconium (CuCrZr), plus aluminium and ferrous.