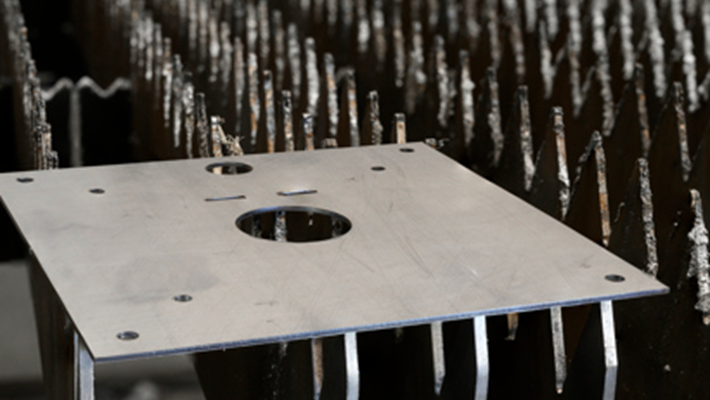
In its quest to increase the scope and efficiency of its laser-cutting facility, HBH Laser, based in Kettering, has installed two state-of-the-art fibre optic laser cutting machines and replaced its two existing nitrogen generators with a single Atlas Copco NGP70+.
As an addition to its established capacity to laser cut common materials such as mild, stainless, and galvanised steel, as well as aluminium, the laser and nitrogen generation equipment upgrade now enables HBH Laser to cut brass, copper and other non-ferrous materials. This gives a quicker, cheaper alternative rather than using their waterjet cutting machines.
“Our ability to precision laser-cut many different materials delivers major advantages to our customers in terms of design options and savings in both time and costs,” explains Lee Humphries, Managing Director, HBH Laser. “Our new equipment utilises state-of-the-art technology, allowing us to produce components that would otherwise require CNC machining, and to offer a range of product features that might not previously have been possible or would have required costly alternatives.”
Within the industry, some laser cutters use oxygen to cut profiles which leaves a carbon-covered edge on the metal. This can make welding and powder coating more difficult to perform satisfactorily. HBH’s new laser technology allows them to cut thicker materials with nitrogen, which provides a super-clean finish to cut edges and a consistency of finish that is essential for repeat product parts. Furthermore, it is accepted that its use results in a much faster production rate.
“Because we produce our own nitrogen gas, we have the assurance that we can rely upon a continuous and sustainable supply and are not reliant upon gas suppliers’ scheduled deliveries and charges, making our processes more cost-effective and self-sufficient,” concludes Lee.
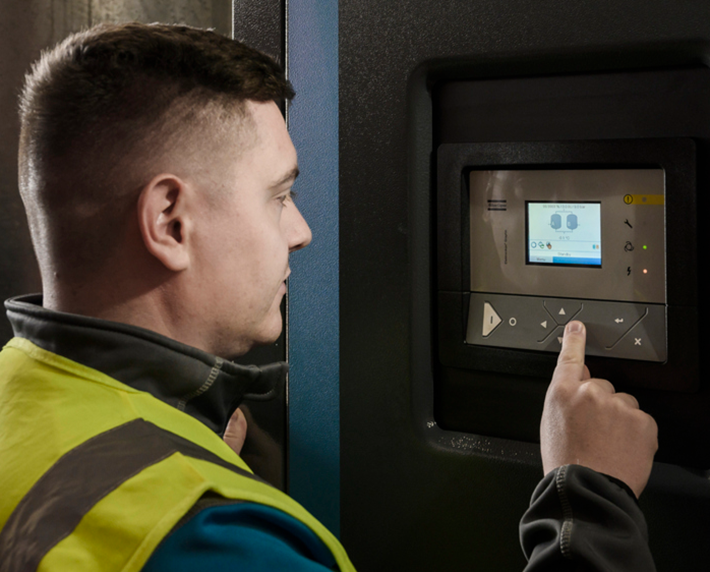
The onsite nitrogen generation system
Atlas Copco’s compact on-site nitrogen generator system comprises a NGP70+ nitrogen generator, a full-feature GA18 VSD+ FF rotary screw compressor as the dry air source feeding the company’s 6kW Trumpf Lasers, plus a 300bar booster, together with filtration and air and nitrogen storage.
In comparison to the output of the company’s original two generators, the new Atlas Copco installation can deliver 99.99% pure nitrogen at the rate of 30.5 m3/h.
The system was recommended on the basis of the company’s laser cutting process consuming 25 m3/h on average and utilising the unit’s high-pressure bottle bank for storage and filling during periods of low demand.
The NGP70+ nitrogen generator sits at the heart of HBH Laser’s installation and is part of Atlas Copco’s NGP/NGP+ range of service-friendly nitrogen generators, which combine high flow capacity, exceeding 3000 Nm3/h, with low operating and maintenance costs. Fully automated, with oxygen monitoring as a standard feature, the units require no specialist installation or commissioning – and thanks to its exceptionally low air and energy consumption, it also offers the lowest cost of ownership on the market today.
An NGP nitrogen generator operates with Pressure Swing Adsorption (PSA) technology that works by separating nitrogen and oxygen molecules within the compressed air stream feeding the unit. PSA does this by trapping the oxygen using adsorption techniques. Adsorption takes place when oxygen molecules attach to a carbon molecular sieve (CMS), allowing the smaller nitrogen molecules to pass through.
Central to the nitrogen generation system is the supply of quality, dry air. The Atlas Copco GA 18 VSD+ FF compressor, with its innovative vertical aspect, is a full-feature compressor designed with a Specific Energy Requirement (SER), which is, on average, 20% lower than comparative models. It delivers a variable output from 14.9 – 62.5 l/s at 7.5 bar and is complete with a built-in refrigerant dryer for dry compressed air supply. It comes as a plug-and-play concept with a host of innovative features that increase its efficiency, cut its energy consumption, lower its noise levels, and reduce its operating costs.
The nitrogen generation system was acquired through a fixed term rental scheme, one of the deals offered by Atlas Copco and its finance partner Société Générale Equipment Finance, which give customers a different option to pay for their equipment.
Applications of nitrogen and compressed air
HBH Laser was founded in 2005 and is part of and supplier to its sister business in fabrication processes, H. B. Humphries & Company Ltd., which produces a variety of standard and bespoke products for diverse applications such as flashings, ductwork, display units, guards, railings, gutters, and rainwater pipes. Its expertise in general fabrication processes embraces working with many metals, including specialist plastic-coated products that are part of projects where hygiene or corrosion protection is vital.
Located in H. B. Humphries’ fabrication plant is a second Atlas Copco air compressor, a GA11 VSD+FF, which powers a CNC punching machine. The compressed air is needed for the suction cups which pick up the metal sheets, for sheet loading and unloading, sorting the punched parts, as well as for general pneumatic controls.
The full benefits of HBH Laser’s upgrade project, in which Atlas Copco’s solutions have played a major role, will be manifested in new business opportunities within the two companies’ customer bases and the expanded capacity to reach out to other industries to meet their specific fabrication requirements.