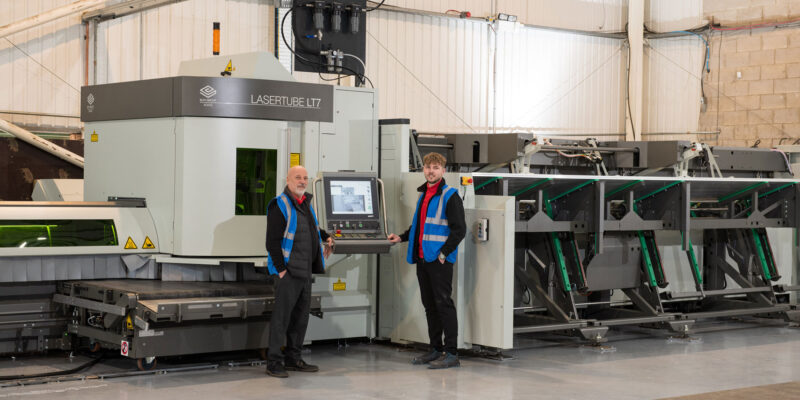
Among the many talents attributed to the Greek and Roman god, Apollo, was the ability to see the future. The same could be said of the team at Apollo Scaffolding Services, who’ve embraced their vision for the company’s future – and scaffold production – with the acquisition of an LT7 Tube Laser Machine from BLM.
“Cutting components accurately is a key requirement for Apollo,” explains Mark Holmes, Apollo Manager. “All our equipment is set up and welded in jigs. If there is a discrepancy in material sizes, it slows or stops our production. We previously used CNC chop saws and they just were not accurate or quick enough.”
“We purchased the LT7 because of how fast and precise it can cut,” says Jordan Hibberd, Apollo Engineering Technician and Factory Manager. “Using this modern method of manufacturing we can keep up with the ever-growing demand within our industry.”
Apollo opted for the BLM LT7 for its 6.5m loader and 6.5m off-loader. The left-hand configuration has enabled Apollo to make best use of available space, and the 4kW laser source allows for cutting thicker section sizes faster. It’s also allowed the company to broaden its client base, now offering laser tube cutting services alongside welding and fabrication to BS 3834 standard.
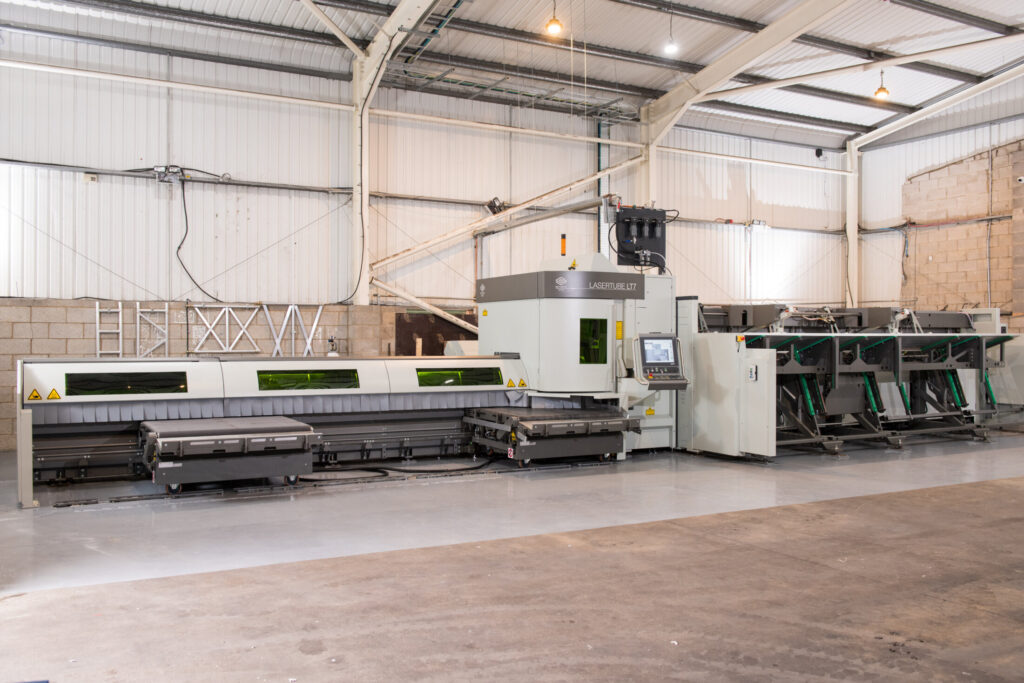
Productivity doubled with LT7
As the only beam manufacturer in Britain, Apollo is well known as a quality manufacturer and supplier of scaffold products into the industry. The company also specialise in undertaking fabrication works and are audited to EN1090-3 manufacturing products up to and including Execution Class 2.
Apollo was incorporated in 2008 at the back of a yard in a small unit, manufacturing beams for use on special projects on bridges. The Scaffold Industry soon took notice. Over the last 16 years, it’s gone from strength to strength, supplying top-quality products that are “Made in Britain”.
Apollo Manager Mark Holmes acquired the responsibility for the Barnsley-based scaffold manufacturing business just two years ago. In that time, the improvements he’s made to their processes – including adopting BLM’s latest laser-cutting technology – have seen an incredible increase in productivity.
“We’ve evolved as a company. Now, with better welding facilities and faster, more accurate parts being cut, we’re producing double what the company was a couple of years ago,” Mark says.
“We can now do things like common cutting,” explains Jordan. “It allows you to make multiple cuts on the same parabola one after the other, which saves time because you’re not cutting twice. And it also saves on materials, so it’s more efficient with less waste.”
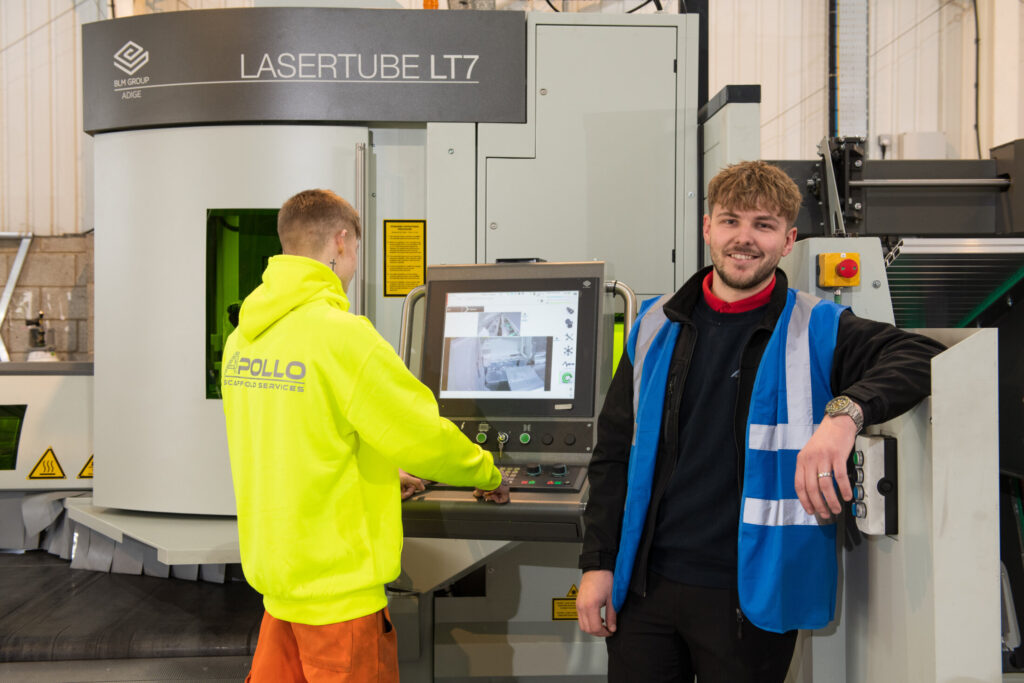
Industry leading capabilities
In addition to the speed and efficiency with which Apollo can now cut aluminium and steel tubing, the LT7 has improved cutting accuracy, making welding the parts a smoother process – quite literally.
“Our welders love welding joints that have been laser cut,” says Jordan. “And having components to work with that are so precise they just drop into the jig first time. With the LT7, we get a precise, quality cut every time.”
The accuracy with which Apollo can cut scaffolding parts using the LT7 has led the team to develop a new industry-leading beam – the 1300mm Super X-Beam. It’s proved 7.8kN/m stronger than its nearest competitor in bending tests and is economical to produce, something that wouldn’t have been possible before utilising the LT7’s precision-laser cutting capabilities, as Jordan explains:
“The X-Beam is all made from 48mm tube. The cross that goes through the beam wouldn’t be possible to produce on a cutting or notching process, it has to be done on a laser tube machine to get the precision needed on those joints.”
Cost and energy savings
With greater accuracy comes the benefit of less waste – and cost savings on materials.
“The new machine has helped us be more environmentally friendly,” adds Claire Marsden, Apollo’s Sales Co-ordinator. “Less impact on the environment, and the new machine is more energy efficient, too.”
Apollo were originally using bottled Nitrogen for the laser cutter; this proved very costly, so the company invested in a Nitrogen Generator.
Now, Apollo generates their own nitrogen for the laser cutter by extracting the gas from the atmosphere, which is made up of 78% nitrogen. The machine removes all the other trace elements (oxygen, carbon dioxide, hydrogen etc) and what is left is 99.97% pure nitrogen, saving on buying bottled gas and reducing waste.
The fully automated laser cutter also requires fewer operators, which has helped to further reduce running costs. Materials are loaded into the machine in bulk. The machine is then fed with materials automatically into the laser cutter. The operator takes the finished cut item off the conveyer and loads into stillages.
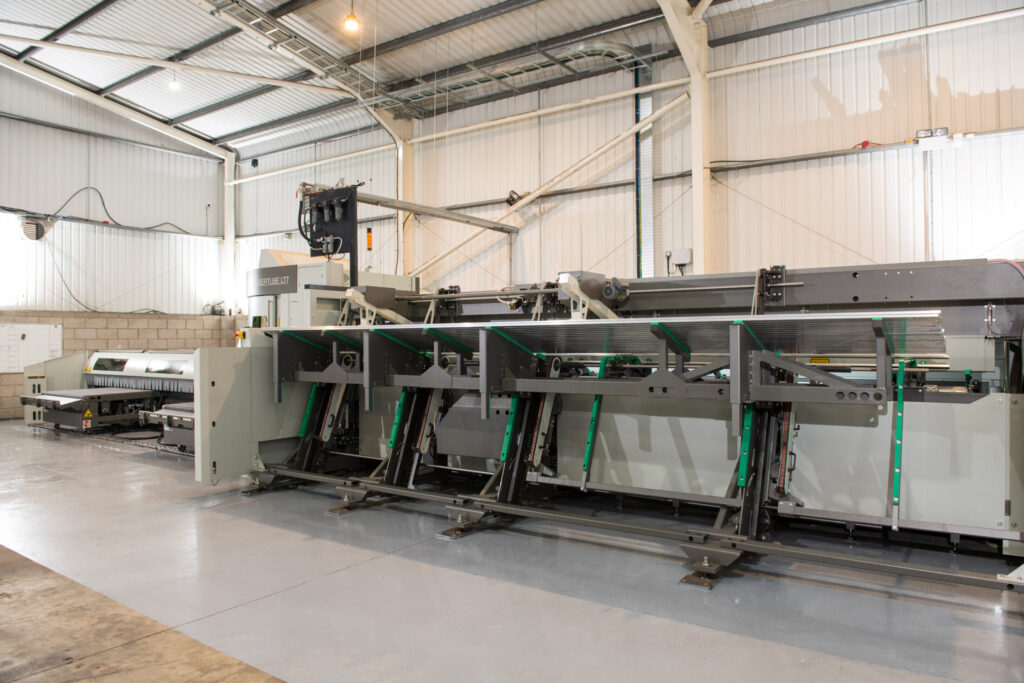
Reliability and customer support
Having previously bought a budget laser cutter that broke down 87 times in 12 months, Mark was keen to ensure his next purchase was reliable and came from a reputable manufacturer offering good customer support. He did his research and chose BLM for these very reasons, as he explains:
“We spoke with BLM’s existing customers prior to our purchase; they were all happy with the service BLM offers and years of trouble-free running with the machines,” he says.
BLM’s support was evident right through from purchase and installation to machine set-up and staff training.
“We got a full installation package, telling us exactly what we had to do before the machine arrived, including laying floor plates and installing the nitrogen and air piping,” says Mark.
With a brief overview of the machine from BLM engineers, Mark was able to begin using the LT7 right away, while four members of his team travelled to Italy for more comprehensive training. “The training has been second to none,” he adds.
“We would recommend BLM to anyone looking for a new Laser Cutter. Once we get this laser cutter busy, and if there’s demand, we may look at extending the service into bending tube with the BLM pipe bender.”
See here for more on the BLM LT 7 Laser Tube Machine.