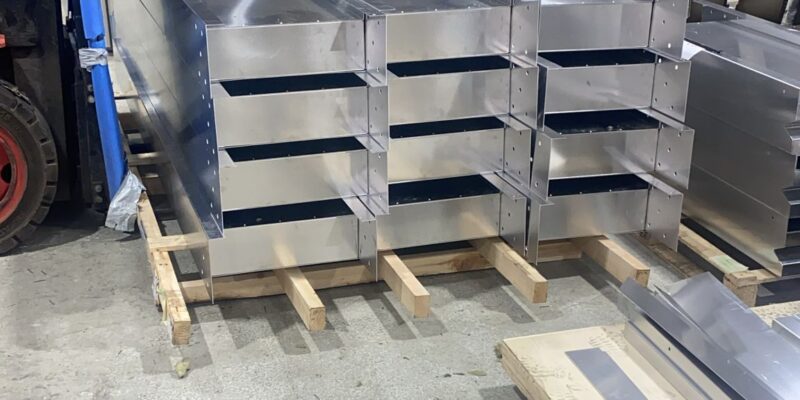
Essential TfL project completed with significant time, cost and environmental savings.
Leicester-based metalwork firm, ADS Laser Cutting has successfully delivered a project in partnership with UB Infrastructure that is set to revolutionise how upgrades to essential trackside infrastructure are delivered across the UK’s rail network.
Responding to a brief from Transport for London (TfL) to deliver a safe and efficient upgrade to a lineside electrical switch box bear the Willesden Depot in West London, UB Infrastructure devised a modular concept to clad the existing building in non-corrosive aluminium that was then manufactured by the team at ADS Laser Cutting.
The critical lineside building had experienced water ingress due to poor design and without urgent replacement or remediation, was in danger of a catastrophic failure. However, mindful of potential disruption to rail services whilst the work was carried out, TfL turned to UBI, experts in modular construction solutions, to deliver an innovative building wrap solution.
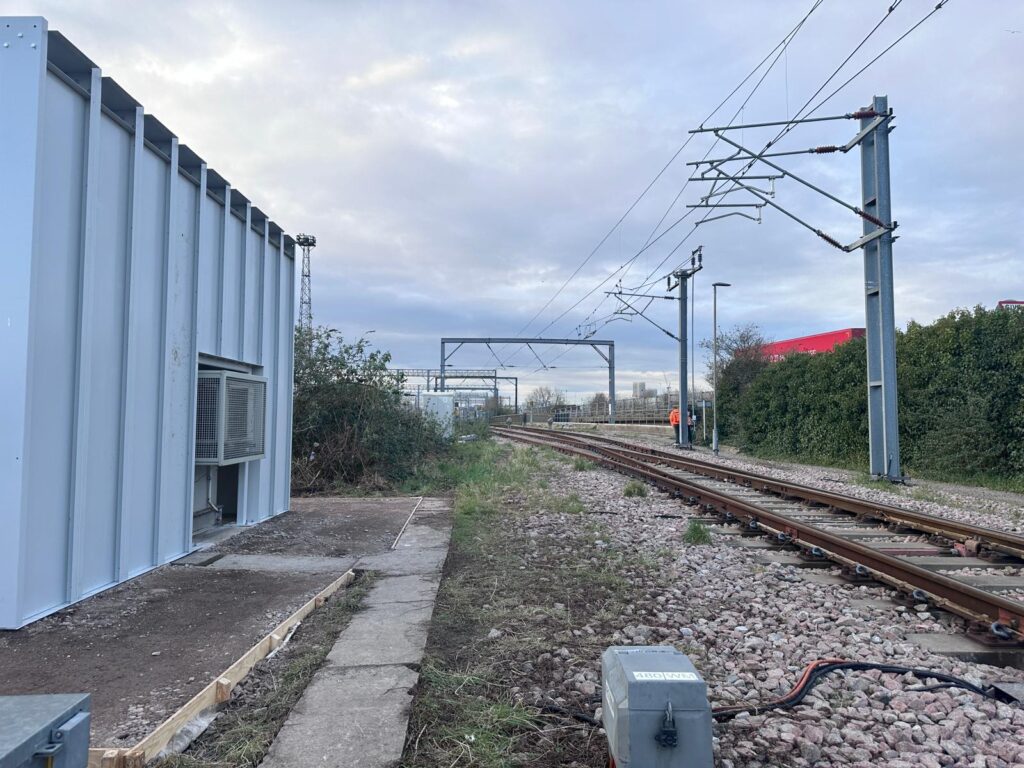
Charlie Davies, managing director at UBI, comments:
“To remove and replace the existing building would have involved lengthy design and planning approvals, whilst more traditional remediation processes would have carried risks due to the site’s proximity to the live rails. Both options would have incurred significant costs.
“In comparison, our UBI Shell solution has been designed with sustainability, longevity of lifespan and ease of installation as paramount considerations. Consequently, it is also 85% cheaper.”
Comprised of a series of aluminium panels that were laser cut, folded and fabricated off-site, their low weight meant that the individual components could be easily sent to site for assembly in just two days. The solution is also more environmentally friendly than other more traditional approaches with the completed building delivering a forecasted energy efficiency saving of 97%.
ADS Laser managed all manufacturing processes ensuring seamless integration of the components, and Stuart Rowan, production director, comments:
“Modular and off-site solutions within construction are growing at pace and it has been a privilege to partner with the UBI team to deliver what we believe is a game changer for UK rail infrastructure.
“As one of the only UK metalwork companies to boast the ability to manage laser cutting, folding, fabrication, finishing and assembly on sheet metal up to six metre all in-house, we were well-placed to partner with UBI on this project. Unusually, we powder coated the parts when fully assembled to mitigate any damage to the components during either the deliver or assembly process.”
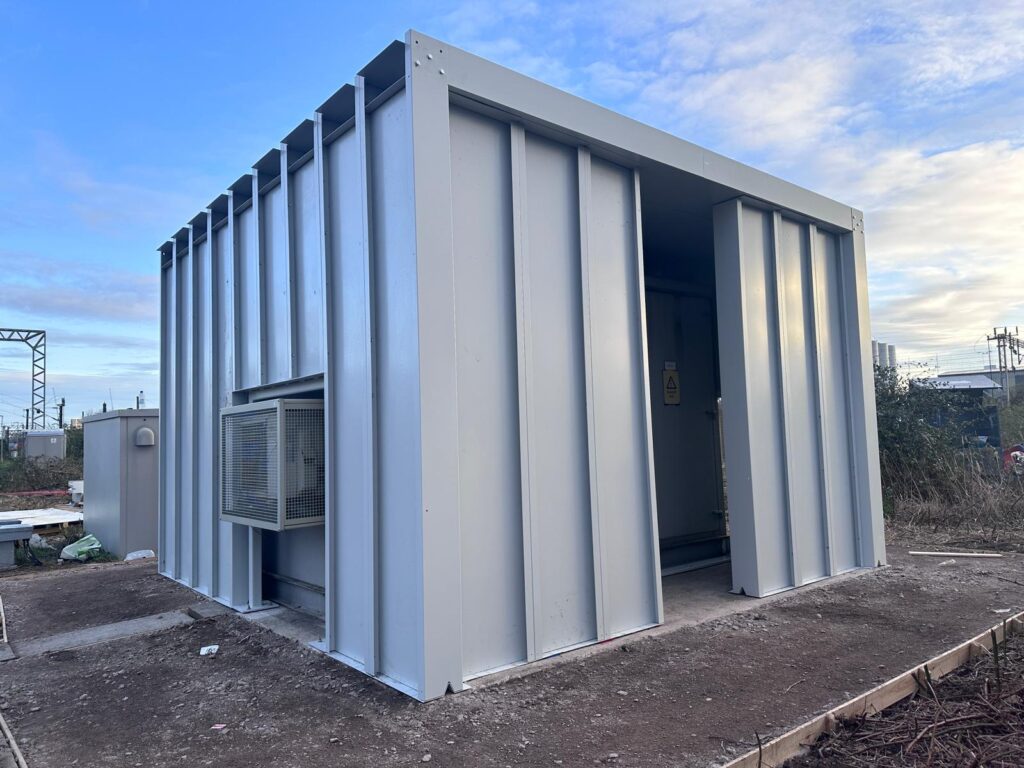
With up to 12,000 trackside structures requiring similar upgrades across the UK rail network, Charlie concludes:
“The team at ADS Laser is more than simply a manufacturing supplier to UBI. We consider them partners in our work and benefit hugely from their expertise within the sheet metal industry.
“The fact that they have invested heavily in market-leading technologies positions them perfectly to adapt and scale to the varying requirements of projects such as this one.
“Witnessing our modular concept come to fruition, thanks to ADS Laser, places us favourably to complete similar rail infrastructure projects across the UK.”
Installation of the modular cladding system at Willesden was carried out by Walker Construction.