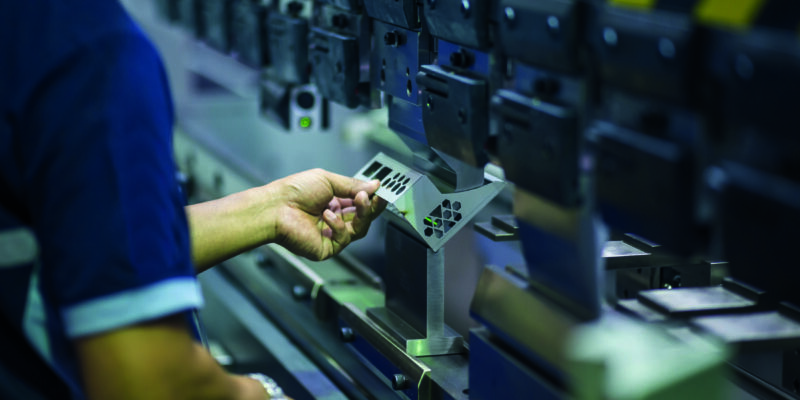
Driven by reliable data, connected solutions for sheet-metal fabrication optimise materials, time, and labour
Striving for greater efficiency has historically meant churning out parts at breakneck speed, crossing our fingers as we test prototypes destined for the scrap heap, and dealing with quality issues only after components are finished. While this approach paved the way for past success, stark new challenges make it increasingly important to view processes holistically and to understand how digitally connecting those processes helps conserve the precious resources of materials, time, and labour.
Making modern manufacturing even more difficult are lead times that grow ever shorter and material costs that precariously balance on a wave of global challenges. On top of this, bent parts are more complex than ever and the press brake operators of yesteryear, who seemed to bend metal by sheer instinct, leave a yawning skills gap as they retire from the workforce.
The good news according to Olaf Körner, (Hexagon Production Software) is that a range of powerful digital tools developed to directly solve these all-too-common problems are more available than ever before, including those that can be easily linked to create a robust end-to-end solution for sheet-metal fabrication. Connectivity between processes helps fabricators put data to work for a clear understanding of where efficiency can be gained and to manage jobs from planning through invoicing with the central goal of optimising time, materials, and labour.
From inquiry to quotation
Feedback from our customers reports that the conversion rate of quotes to orders is about 35%. With success rates relatively slim and second chances rare, the key is to deliver a comprehensive quote without investing undue time in a job that may not pan out.
Data collected at the beginning of a job, during the inquiry phase, is ideally used to provide an accurate quote and steer each downstream process if the job is won. Connectivity between a manufacturing execution system (MES), quotation software, and computer-aided-design (CAD) software eliminates redundant data entry during the planning and quotation phase and ensures that everyone in the shop is working with the same information.
The inquiry is the point at which we get an idea of what a job looks like in terms of difficulties, such as challenging materials or complex shapes, and details like lot sizes and lead times. This is the stage at which we determine if we truly understand the scope of the project and if there’s enough information to start the job. MES software can be especially helpful at this point if a manufacturer has stored information that affects the quotation, such as whether a customer receives a discount or if their delivery point is difficult to access. Information from MES software can then be shared with the quotation system to begin building the quote.
At the point of inquiry, a CAD system developed specifically to solve manufacturing challenges and optimise design for manufacturing should be used to determine if the part can be made with the tools at the fabricator’s disposal. For example, if you cut 100 parts before discovering they won’t fit on your press brake, that’s a problem that should have been identified prior to fabrication.
Once how the job will be performed is determined, the quotation software can use the data derived from the MES and CAD systems to complete the quote. The ideal quote covers any customer-specific charges, as well as machine time, materials, welding, painting, assembly, shipping, and consumables such as oxygen or nitrogen.
A single staff member may use all three systems to develop quotes at a smaller company, while three different people may handle the tasks separately at a larger business. Regardless, compatibility among the three systems makes the sharing of data safe and seamless for providing quotes that remove the guesswork and ensure you’re paid for the job that you’ll actually do.
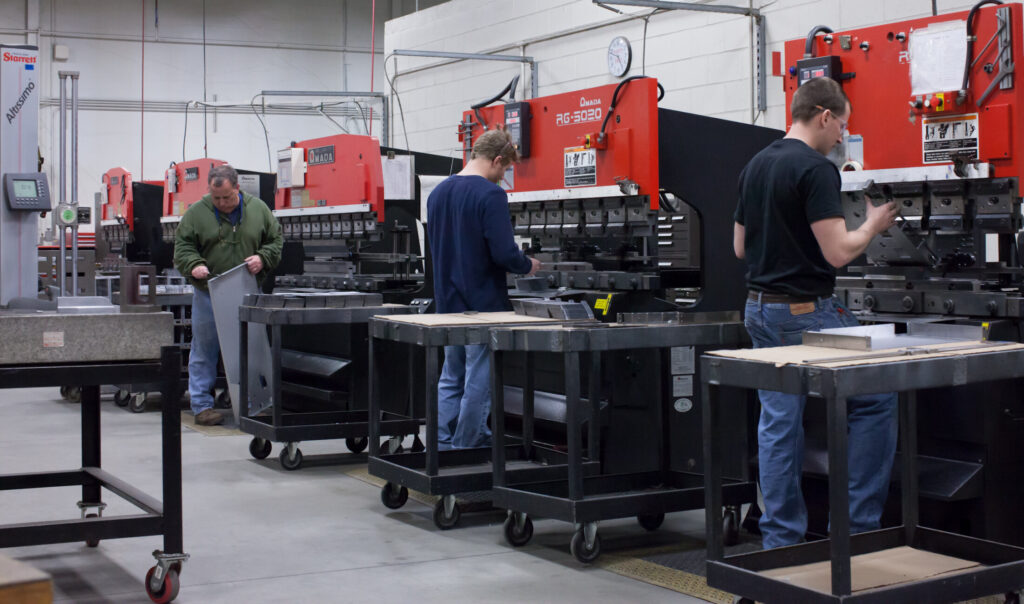
First time right
How profits are achieved in fabrication can hinge more heavily upon material optimisation than in other manufacturing disciplines due to the relative simplicity of many sheet-metal components. While OEMs typically expect a hefty price tag for, say, gas turbine blades machined in Inconel, the expectation is that the price of steel sheet-metal parts should remain relatively low regardless of rising steel costs.
Unfair as it may be, this expectation leaves little wiggle room for trial and error that results in scrap, so the elimination of prototypes can be vitally important, especially for low-volume manufacturing. If half of a component’s cost is in the material and that figure cannot be significantly altered, turning a profit is dependent upon the ability to quickly understand from a digital standpoint how a part can be made. The challenge with eliminating prototypes is in being confident that that we can correctly produce the component right out of the gate.
While digitally connecting the process thread significantly increases efficiency, optimising part design for efficient production after jobs are won is the single greatest opportunity to increase profits. Provided that customers receive the components or assemblies they paid for, fabricators are free to make those products however they choose.
Using CAD-for-manufacturing software, they can, for instance, reduce the parts required by the customer from two separate pieces to a single part for less processing, or choose to bend an area that would otherwise need to be welded to reduce time and labour. Likewise, they may opt to create a tenon, or a notch on the end of a tube that’s designed to fit into the slot of another. Tenons help ensure that tubes are assembled correctly and that they can be easily welded by a single employee, which reduces both opportunity for error and labour.
At this stage, the CAD and bending software work in tandem to help manufacturers optimise design. A completed design can be run through bending software for analysis of the fabrication process and, if that process isn’t optimal, changes can be made using the CAD software until the fabricator achieves an ideal balance between what the customer wants and the capabilities of their shop.
Proving out processes digitally eliminates the excruciatingly slow and painful loop of cutting a part and handing it off to the press brake operator to see if they can bend it to specifications. On top of contributing to the scrap heap, this tiresome process tied up the time of both the operator and the machines needed for cutting and bending. If a test performed by the press brake operator didn’t work the first time, it was back to the drawing board for redesign so the prototyping loop could begin all over again.
Due to the widespread availability of robust nesting technologies, efficiency in cutting sheet metal is no longer difficult to achieve. Nowadays, the significant challenge lies with perfecting bending operations, especially as parts continue to increase in complexity. Production software then provides detailed operator instructions helps to essentially teach operators how to bend parts and ensure that they will be bent correctly the first time.
Powering manufacturing
After design is optimised using a combination of CAD and computer-aided manufacturing (CAM) software for bending and cutting operations, the MES software takes its rightful place on centre stage. By this point, the system understands every detail of the project and can effectively assign job tasks based upon material, machine, and staff availability, among other factors. The system will distribute the work and plan each step — from cutting, bending and welding to painting, assembly, shipping, and invoicing — based upon the job’s lead time.
The system will also automatically check existing inventory to determine whether the required materials are available prior to manufacturing. If they aren’t in stock, materials can be ordered from a preferred supplier directly from the system’s interface. As shortened lead times ensure that suppliers are now accustomed to delivering materials in hours instead of days, a job that began in the morning can often be ready to leave the shop by the afternoon.
As manufacturing begins, the MES software helps ensure that machine operators know where to be and when, as well as which materials are required. It tracks the progress of cutting, nesting, and bending operations in real time and, if delays occur, automatically adjusts subsequent steps in the production schedule. For instance, if a cutting operation was supposed to take three minutes, but the operator wasn’t at their station to perform the work, the system will automatically adapt the timeline.
While managing the many moving parts of sheet-metal fabrication is where MES capabilities truly shine, it’s also a valuable tool for comparing how actual manufacturing measures up to what was planned in the pre-manufacturing phase and how much the job actually cost. It’s also an ideal tool for measuring the success of process changes, such as producing parts with tenons for easier assembly and welding, or the automated labelling of cut parts. If MES software recorded manufacturing data before and after the use of tenons or labels, for example, it’s easy to compare differences in the amount of time and labour required to complete the sorting, assembly, and welding stages of the job.
Though not directly connected to an end-to-end solution for sheet-metal fabrication, asset management software can be used to track the overall equipment effectiveness (OEE) of machinery to better understand machine performance and utilisation, and to pinpoint problems that cause down time.
Hi-Tech Fabricators
As a job shop that specializes in both precision sheet metal and machining, U.S.-based Hi-Tech Fabricators delivers added value to customers by offering a range of services under one roof. The company has diversified since opening in 1983 and today performs work for the aerospace, automotive, defence, and medical industries.
In 2018, Hi-Tech Fabricators acquired a new IPG laser cutter and implemented CAM software dedicated to sheet-metal fabrication to program the new machine, its existing Mitsubishi laser cutter, and two Amada punch presses.
After researching options for a production management solution, the company chose an MES system that offers interoperable functionality with its new sheet-metal production software. Its goal in adopting the software for to achieve more efficient production while eliminating data-entry redundancies and mountains of paperwork.
“We’re using it for estimating, scheduling, ordering materials, and job organization,” said Michael Bailey of Hi-Tech Fabricators. “Before the software, I had a dozen different locations for things like files, non-disclosure agreements, and programs scattered about on my server; now, all of that is on one place and I don’t have to spend time looking for any of it.”
Various software packages were used by the company, and, at one point, five different systems were used to manage jobs and business data. The company now uses its MES system and CAM software to generate quotes and uses the MES system to manage all downstream activity.
Mapping the road ahead
Despite the numerous challenges of increasingly complex sheet-metal fabrication, we have at our fingertips powerful digital tools developed specifically to solve the everyday problems that diminish efficiency and shrink profits. In joining robust planning, design, quotation and manufacturing software to create end-to-end solutions, we can immediately begin to utilise the valuable data that propels projects from planning through delivery.
Accurate and reliable digital replicas of manufacturing processes enable the elimination of prototyping and associated waste while ensuring that operations can be performed safely. Striving for faster production has been replaced with a striving for greater understanding of how well our processes work and where they can be improved. Driven by reliable data, an end-to-end solution can be an invaluable roadmap that relies upon information about where we’ve been to help us determine where we’re going.