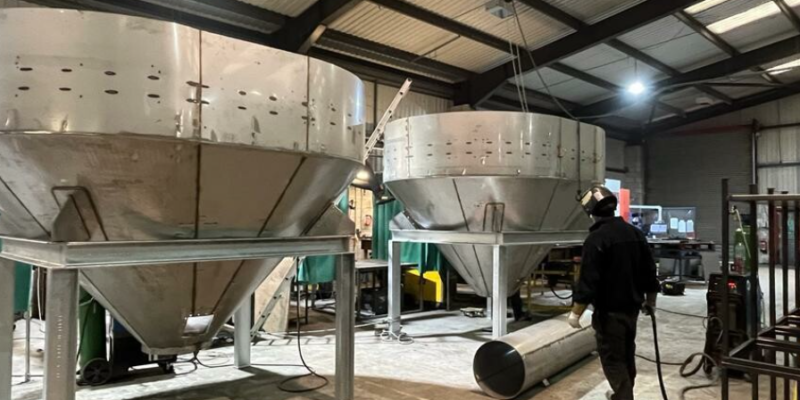
CSM’s 30-year commitment to quality is showcased by the recent replacement of a fertiliser funnel that served for decades, now upgraded to boost efficiency and meet modern demands.
Background
Since its inception in 1992, CSM has worked with a range of businesses to create bespoke metal fabrications to meet specific requirements. Fertiliser processing is just one area in which our expertise and craftsmanship has been put to the test to help customers boost productivity and profitability.
One of the earliest examples of our work in the sector was a large custom-made fertiliser mixer funnel, meticulously designed and fabricated in low carbon galvanised steel for a fertiliser manufacturing company 30 years ago. During that time, the very same machine has processed millions of tonnes of fertiliser.

Challenge
More than 30 years after the original fertiliser funnel was installed, the customer wanted to invest in a new model to reduce mixing time and increase output. It was essential for the new solution to be developed with careful research and expertise, as some fertiliser ingredients can react with certain materials – or even become explosive in contact with the incorrect elements. The manufacturer also required the replacement funnel to be just as durable and reliable as the previous model to ensure business continuity, peace of mind, and maximise the investment.
Solution
As the original custom-made fertiliser mixing funnel exceeded expectations with its performance and durability over the 30-year period, the fertiliser manufacturing company knew exactly where to turn to commission a new model. The team at CSM were delighted to assist the customer a second time around, with CSM co-founder, Malcolm Pearce, keen to turn his hand to the project 30 years on from the original design and put new technologies and out-of-the-box techniques to work.
After an initial consultation to gauge specific requirements and timelines, the team got to work, putting
a colleague’s newly acquired university course knowledge to the test and used fluid dynamic modelling and mathematical hand calculations to find the most efficient method for fluid and solid mixing to boost throughput. The team also developed cross-sectional scale models to provide evidence for the most appropriate profiles of the formed sheet metal. Once the new design blueprint had been developed and approved by the customer, CSM’s in-house team of specialist fabricators were engaged to turn the vision into reality.

Results
The brand new custom-made fertiliser funnel was completed, delivered and installed at the manufacturer’s headquarters to desired timescales, ensuring downtime through the process was minimal. Where the original mixing funnel could handle two to three tonnes per mix, the new and improved model processes six to eight, significantly reducing mixing time and increasing throughput and efficiency.
The customer was impressed with the ease of the process, the evident quality of the product and the increased capacity of the blender – with up to four times as much material being processed at once.
Keith David, managing director of Customised Sheet Metal, commented: “The team at CSM has grown and evolved since the original project, and we’re proud to have our unwavering commitment to quality rewarded with customer loyalty spanning decades. We were delighted to assist the customer again and feel confident that the new mixer funnel will stand the test of time, while significantly outperforming the throughput of the original.”