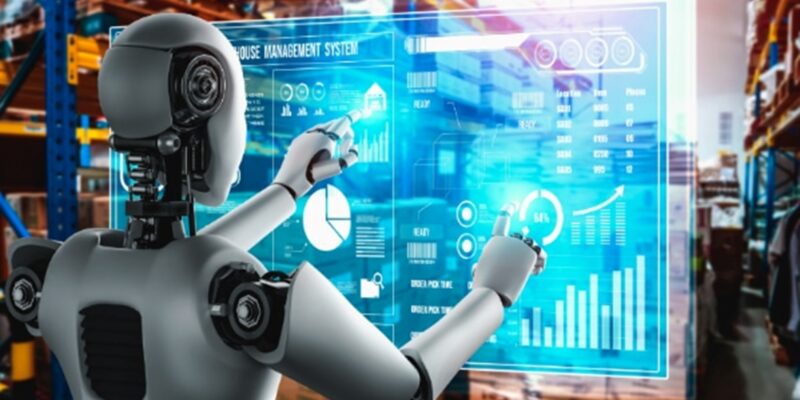
Wrekin Sheetmetal Ltd explains – The biggest advancement of the fourth industrial revolution has been the internet. This has provided the internet of things, allowing for the interconnection of technologies and better access in real-time to cyber-physical systems and information.
This industrial transformation has helped manufacturing companies and organisations to work well together across departments. They can do this in a way that is far more connected than it ever has been before. Using this technology, businesses can be more efficient and productive in their daily work. Also, have access to more real-time data, (as a result of embedded software systems), and this gives them better insight into what’s happening with the business, with their vendors and with their customers.
Manufacturing is being digitally transformed from the front office to the plant floor with the help of Industry 4.0. The advancements that are included in this new revolution allow companies to connect better with integration, they have better intelligence and more insight into data from across the business. Alongside this, you can benefit from automation, ensuring that your processes are faster and more accurate.
The Fourth Revolution: 5 Ways Your Business Can Adapt
Develop Your Workforce
You want your workforce to be more efficient and more productive, and that means making sure that you have the right people working on your team at any given time. Developing your workforce is one of the many ways businesses can adapt to Industry 4.0, and with the right investment in education and training for your workforce, you’ll be able to retain your staff. We are currently living in a talent-tight world, which means that businesses are struggling to keep hold of the staff that they’ve got, who are leaving in favour of better options elsewhere.
There is a shortage of specialist workers in the manufacturing sector specifically, so retraining your staff and investing in their education allows you to invest in their future. This could help you appeal to your employees and enable you to keep them working with you. This will also help to reduce any anxiety that can come with using new technologies. Your recruitment and training processes should be used in a way that helps keep young people interested in what you have to offer as a business. You can adapt your business with recruitment and training, and make people feel like they are in the best place to work.
Establish Clear Goals
As a business leader, you know how important it is to have goals for your business to follow. It’s not just about the fact that you need to have goals for your financial aspirations, but you need to have long-term industry 4.0 objectives set so that your business can reach the right heights and still become a force to be reckoned with in your industry. Industry 4.0 can help achieve this as it is most concerned with connecting the entire production chain.
This level of integration ensures that you can make the most of automation and data exchange technologies in your manufacturing systems. Some of the technologies you can utilise include things like advanced robotics or 3D printing, and if this means that you will be paying out for machinery, you will find that your return on that investment will more than pay for the money you invest.
Analysis of Data is Key
Data analysis is vital for any business, but for businesses in the manufacturing sector, it’s one of the pillars that keeps your business ticking forward. You need to know your input and your output and you need to understand the figures to ensure that your employees are safe. This is all done through the process of data analytics. Most manufacturing businesses can have hundreds of sensors that generate huge amounts of data every single day. With the help of Industry 4.0, this data can be processed using artificial intelligence technologies that you might not have had access to before. All of this information can be turned into useful business insight.
For example, predictive maintenance can be done by measuring the output of the machine. If the machine is not working at the capacity in which you are most comfortable, you can fix it so it does. If you are looking at your analytics and are finding that there is an efficiency issue in your production operations, you can locate the source of the issue and fix the problem. You can only do this with the right data and analytics, so you have to ensure that you have this in place when it comes to implementing Industry 4.0 in your manufacturing business.
Choose the Right Tools
Not all businesses do the same thing the same way, which means it’s very important for you to choose the right technology and machinery when you are adapting to Industry 4.0. There are plenty of digital tools out there that you could utilise, and they can be beneficial because they can help you with your productivity, your data analysis and your long-term business goals.
These include big data analytics in advanced algorithms, advanced human-machine interfaces, mobile devices, location detection technologies and multi-level customer interaction and customer profiling technologies. That’s not an exhaustive list, by the way!
Introduction of Pilot Projects
Before you do anything in your business you should want to trial a project so that you know whether or not it’s right for you. A pilot project for Industry 4.0 will help you to assess whether or not it’s the right way for your business to go. You can introduce it slowly, by just choosing one or two of the technologies available to you. When you do this, you can see how your employees and your customers take to it. It will enable you to go further and determine whether or not you say yes or no to launching this particular technology in your business. It’s ok if something doesn’t work for you the way that you thought it would because you can always look at other technologies available.