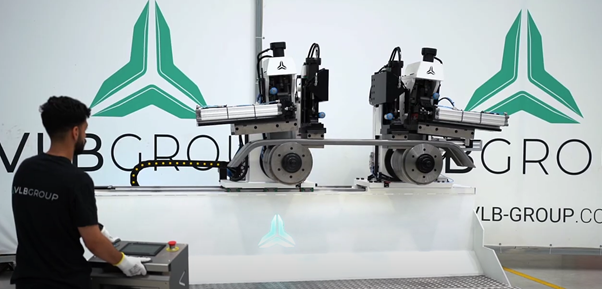
The dilemma between mass production and better customisation is universal across all industrial sectors, and the metalworking industry is no different. There is plenty of debate about which path is best to follow, though we are confident in saying that when processes are automated, the increase in quantity almost always translates into increased profitability – Engineering Technology Group
The more processes are automated, the faster, cheaper, and more accurate the output is. The problem is that as a process becomes more automated, it becomes harder to make changes to the products quickly.
The Challenge
A VLB Group customer, who is an advanced custom metal fabrication company specialising in the design, build, and customisation of aftermarket bumpers and toolboxes for pickup trucks, SUVs, buses, service vehicles, and lorries for commercial and personal use in the North American market, have found automation of their processes difficult due to the huge range of vehicles they cater for and the vast number of customisation options available. They have also experienced challenges with manpower intervention, production time reduction, and the need for increased profits, all while manufacturing the parts to tight schedules and to extremely high quality.
The Solution
Considering the huge investment and the limitations of the plate-forming solutions typically used in mass production, the VLB Group R&D team developed a hybrid solution using our know-how in plate forming and tube bending.
A double-head profile bender has adjustable tools that can be easily adapted or replaced to adapt to a new design. This customised solution replaces huge hydraulic presses and very expensive tooling.