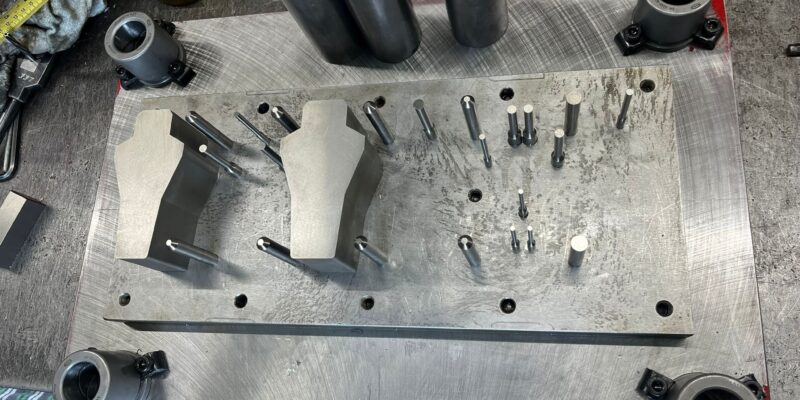
TWP Manufacturing announces significant tooling manufacture project following last year’s Subcon Show. The commission will see TWP complete tooling for seven 304 stainless steel anti-static clamps. This comprehensive project showcases the company’s in-house design and manufacturing capabilities and commitment to quality and efficiency.
TWP’s expert team designed and manufactured five piercing and blank tools, as well as six forming tools ganged on two die sets. This strategic approach reduced tool setting and tooling costs, enabling the production of seven different clamps with interchangeable piercings to meet variable requirements.
The project involves manufacturing over 190,000 machine parts annually in the company’s state-of-the-art CNC shop. Each part is meticulously formed, assembled, and approved by the customer, ensuring the highest standards of quality and precision.
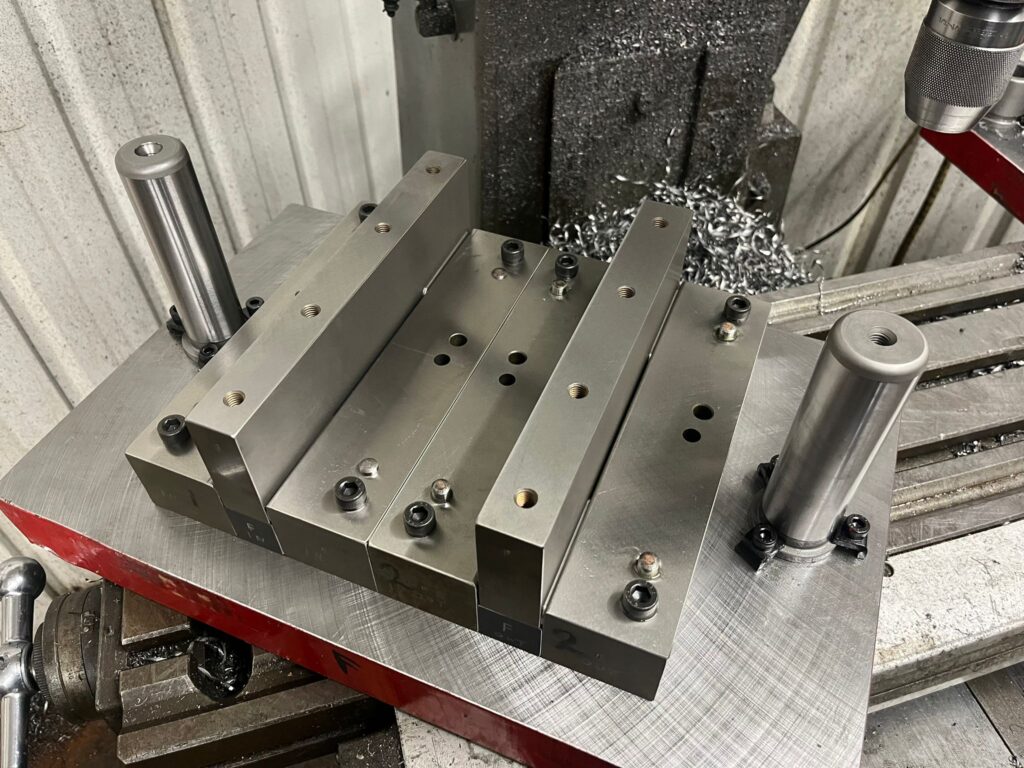
This project exemplifies TWP’s turnkey manufacturing capabilities, combining several advanced processes:
- Automatic Piercing and Blanking: Efficiently creating precise components.
- Second Operations on Forming: Ensuring detailed and accurate shaping of parts.
- CNC Turning: Achieving high precision and consistency in every component.
- Spin Riveting: Providing robust and reliable assembly.
- Injection Moulding: Producing high-quality plastic components.
- Final Assembly and Testing: Ensuring each clamp meets stringent performance standards.
- Laser Engraving: Marking every part with the customer’s logo, batch number, date, and CE markings for traceability and compliance.
A customer-centric approach
The varied sizes, jaws, and connections of the seven clamps were meticulously designed to meet the specific needs of the customer. TWP’s commitment to customisation and precision ensures that each product meets the highest standards.
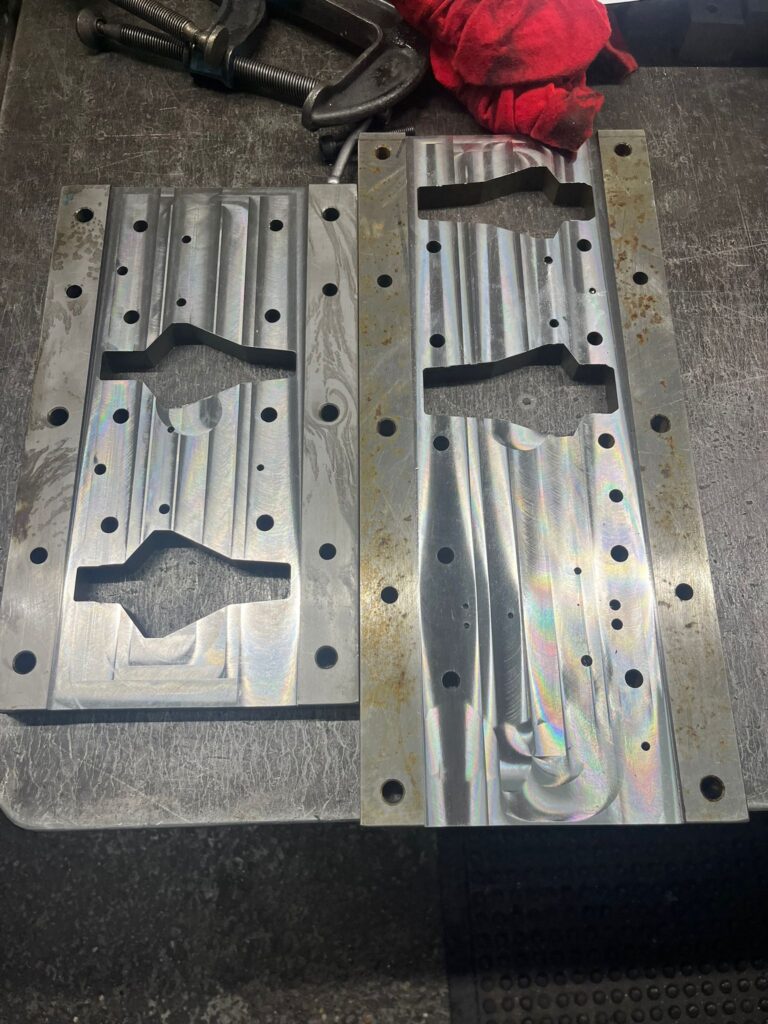
The success of this project has allowed TWP to expand its team, employing two additional skilled professionals who have joined the TWP Manufacturing family. This growth underscores the company’s dedication to creating job opportunities and supporting the local economy.
All parts are crafted from premium 304 stainless steel, ensuring durability, corrosion resistance, and superior performance. This choice of material reflects our commitment to using only the best resources for our projects.
TWP Manufacturing is proud to deliver turnkey solutions that combine innovation, efficiency, and quality. This project not only highlights their capabilities but also the company’s dedication to meeting and exceeding customer expectations. Every single part of this project has been carried out in TWP’s Tipton factories – supporting their passion for UK Manufacturing. A spokesperson for TWP said: “We are proud to say that we have the skills, experience and most of all passion for designing and manufacturing this project from start to finish.”