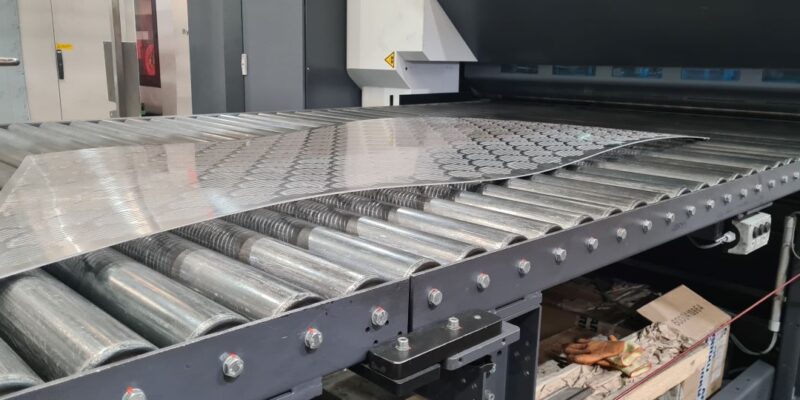
In the intricate world of metal fabrication, the journey from raw material to finished product is fraught with challenges and intricacies. Among the crucial steps in this process is the destressing and flattening of metal sheets, a meticulous endeavour that lays the foundation for further fabrication and has a transformative impact on the final product.
Here, laser cutting and subcontract engineering specialists Wrightform delve into the art and science behind destressing and flattening metal, exploring techniques, challenges, and the potential for transforming the fabrication process for your business.
Understanding Destressing and Flattening
Destressing and flattening metal is a vital pre-fabrication process aimed at alleviating internal stresses and irregularities present in metal sheets. These stresses, induced during manufacturing processes such as rolling, shearing, or heat treatment, can lead to deformation, warping, or residual strain in the material. Destressing involves the controlled application of force or heat to relieve these internal stresses while flattening focuses on restoring the metal to its original flatness and dimensional stability.
The Science Behind the Process
Destressing and flattening metal sheets entail a combination of mechanical, thermal, and metallurgical principles. Mechanical methods such as roller levelling, tension levelling, and straightening use pressure and tension to stretch and compress the metal, redistributing internal stresses and promoting uniformity. Thermal techniques like stress relieving and annealing involve heating the metal to specific temperatures and holding it for a predetermined time to induce relaxation and recrystallisation of the metal structure, thereby reducing stress and improving formability.
What can happen if metal is not destressed or flattened prior to fabrication?
When metal is fabricated without first being destressed or flattened, internal stresses from the production process can lead to significant distortions and warping. These internal stresses cause the metal to deform unpredictably when cut, welded, or otherwise manipulated, compromising the precision and integrity of the final product. This can result in misalignments, weaker joints, and overall reduced structural reliability, necessitating additional rework and adjustments, and potentially leading to failure in demanding applications.
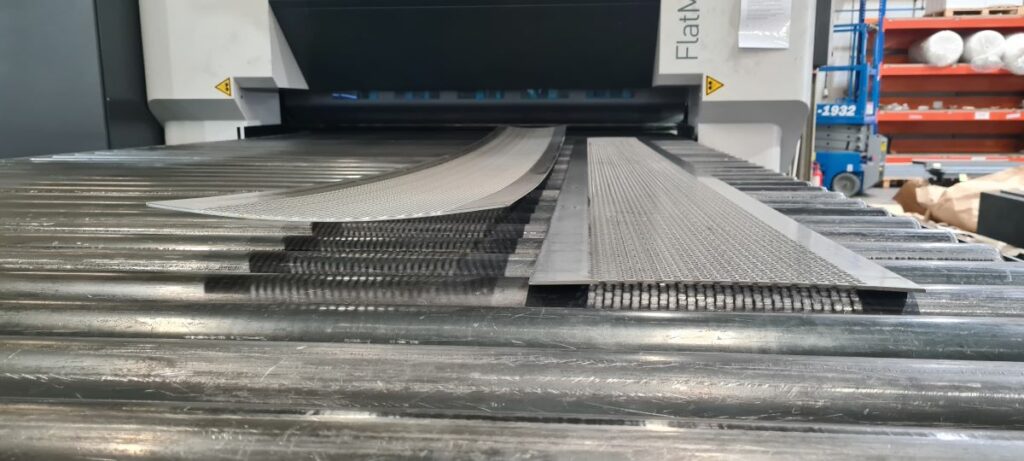
Challenges and Considerations
While destressing and flattening metal offer numerous benefits, including improved formability, surface quality, and dimensional accuracy, they pose several challenges that require careful consideration. Variations in material composition, thickness, and grain structure can influence the effectiveness of destressing and flattening techniques, requiring tailored approaches for different metal alloys and grades. Moreover, over-application of force or heat can lead to excessive material removal, surface damage, or metallurgical changes, compromising the integrity of the metal and affecting downstream fabrication processes.
Techniques and Tools
Various techniques and tools are employed in destressing and flattening metal, each tailored to specific materials and requirements. Roller levelling, the most common method, utilises sets of rollers to apply pressure along the length and width of the metal sheet, gradually flattening it to desired tolerances. Tension levelling involves stretching the metal between sets of rollers under tension to remove waviness and impart uniform flatness. Other methods, such as shot blasting, stress relieving, and annealing, offer alternative approaches to destressing and flattening, providing flexibility and precision in addressing different material properties and fabrication challenges.
Applications and Benefits
Destressing and flattening metal are critical in various industries, including automotive, aerospace, construction, and manufacturing. In automotive manufacturing, flat and stress-free metal sheets are essential for stamping, forming, and welding processes, ensuring dimensional accuracy and surface quality in-vehicle components. In aerospace, destressed and flattened metal sheets are used in structural components, fuel tanks, and aircraft panels, where precision and reliability are paramount. Also, in architectural and construction applications, flat and uniform metal sheets contribute to the aesthetics, durability, and performance of buildings, facades, and infrastructure projects. Advancements in materials science, including the development of high-strength alloys and composite materials, present new challenges and opportunities in destressing and flattening metal, driving research and innovation in the field. Advancements in materials science, including the development of high-strength alloys and composite materials, present new challenges and opportunities in destressing and flattening metal, driving research and innovation in the field.
Destressing and flattening metal is a critical step in the metal fabrication process, laying the groundwork for further shaping, machining, and assembly. Internal stresses and irregularities are alleviated through a combination of mechanical, thermal, and metallurgical techniques, resulting in flat, stress-free metal sheets ready for downstream fabrication. As industries continue to demand higher quality, tighter tolerances, and greater efficiency, the importance of destressing and flattening metal cannot be overstated. By embracing innovation, leveraging advanced techniques, and understanding the complex interplay of science and engineering, manufacturers can unlock new possibilities and elevate the art and science of metal fabrication to unprecedented heights.