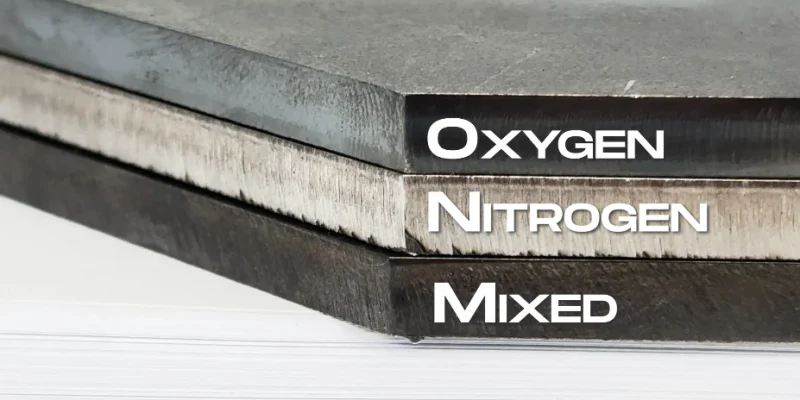
The process of laser cutting involves the use of a focused laser beam alongside a co-axial jet of gas to create a cut. The laser beam itself remains unaffected by the gas as it effectively melts or vaporises the material, with any resulting molten material or debris being blown away by the gas jet, ensuring a high-quality finished edge. The gas jet, otherwise known as the assist gas, helps prevent the molten material from re-solidifying on the surface of the material. It also helps to cool the material and prevent it from warping or distorting. The most widely used assist gases in fiber laser cutting are oxygen and nitrogen.
Oxygen for laser cutting
Oxygen is a highly reactive gas and is extensively used for laser cutting mild or carbon steels. When the laser beam is active, the reaction between the oxygen and the metal creates additional heat energy which supports the cutting process, allowing thicker materials to be cut. However, oxygen can result in oxidation, causing a carbon layer to form on the cut edge. This can result in poor product finish and adhesion problems for any coating or paint applied to the oxidised surface.
The main benefits of using oxygen as an assist gas can be summarised as:
- Smooth edges with no burrs
- More cost-effective cutting of thicker materials
but the main drawback is:
- Oxidised edges may make the cut materials unsuitable for subsequent welding, plating or painting.

Nitrogen for laser cutting
Nitrogen, being an inert gas, is particularly useful when a high-quality cut is required. Nitrogen eliminates oxygen in the air and enables the laser to run in an oxygen-free environment. This prevents any reaction with the hot metal, resulting in a perfect, shiny cut without any oxidation or discolouration on the cut edge. Nitrogen also enables increased cutting speeds, higher productivity, better control and higher efficiency.
Nitrogen also cools the material being cut which reduces warping and improves the accuracy of the final product.
The most suitable metals for laser cutting with nitrogen include stainless steel, aluminium, copper and brass, non-ferrous metals and high-alloy steels.
The main benefits of using nitrogen as an assist gas can be summarised as:
- Clean edges with reduced oxidation
- Higher cutting speeds
- Reduced warping
but the one main drawback is:
- It is a more expensive cutting method, particularly when dealing with thicker materials

The use of mixed gases
Opting for a mixture of gases is a way of leveraging the benefits of each gas, the classic example being a mix of oxygen and nitrogen. Oxygen aids the material’s melting process, while nitrogen helps to eject waste material and increase speed. Using this combination of gases also enhances the surface finish and enables subsequent welding, plating or painting of the material to take place.
Mixed gas cutting has been a key development in recent years, and today’s ultra high-powered fiber lasers have made full use of this technology to take their performance to the next level.
The use of gas mixtures has grown massively over the last 5 years, from a niche process mainly used for aluminium cutting to a genuine alternative method for cutting thick carbon steels. In some instances, straight nitrogen cutting may still be the preferred method for stainless steel, to achieve a shiny edge, but mixed gas has become a viable alternative here too.