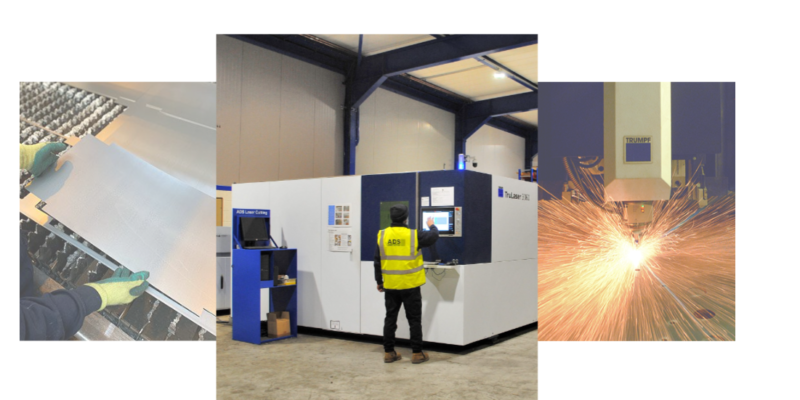
Supply chain challenges have prompted many businesses to diversify their suppliers in recent years. Developing new relationships or expanding existing ones helped to overcome the longer lead times or higher import costs seen throughout the conditions created by domestic and global challenges in recent years.
Diversifying suppliers was an essential exercise in the face of these challenges. However, while intended to mitigate risk, continuing to manage multiple manufacturers can push up costs over time. It can also cause project delays, risk inconsistent product quality, or push up administrative costs.
Instead, working with a streamlined pool of suppliers can keep costs and lead-times in check and support consistency and quality in end-products.
Whether mass manufacturing commonplace products or producing specialist parts, safe and reliable products require quality, consistent components from reliable suppliers
Streamlining supply chains is one of the main ways businesses are managing costs now, pulling ahead of traditional cost-saving measures like cutting back on labour. Research by Boston Consulting Group last year found that 65% of businesses believe that when managing costs, the most important function to look at is supply chain and manufacturing costs.
The benefits of streamlining your supply chain:
- Lower costs – Easily see and manage all costs – for materials, production, delivery and administration
- Save time – Limit time needed to brief and follow up with suppliers
- Ensure quality – Ensure consistency and overall quality of products
- Improve forecasting – Predict demand or price rises using consistent data from fewer suppliers
To enjoy these benefits, it’s valuable to understand exactly how hidden costs can creep in from ordering from multiple manufacturers.
Shipping and packaging costs can increase when working with multiple manufacturers. Different locations, delivery protocols or minimum order quantities (MOQs) can lead to higher costs, require extra resource to receive deliveries, incur extra fees for smaller orders, or incur excessive levies for packaging. This can also worsen environmental impact from transportation and packaging.
Delivery delays or varying lead times are also a cost risk. Ordering stock or individual items from different suppliers is likely to create different lead times for goods, making project coordination tricky and risking delays. Additionally, managing stock or inventory from multiple suppliers can create logistical challenges, risking overstocking items or shortages.
Perhaps the most overlooked cost can be in managing relationships with multiple suppliers, draining time and risking confusion, particularly if raising queries or returning items. Handling invoices and managing payments will also require extra time of other departments.
Finally, perhaps the biggest challenge of relying on multiple manufacturers is quality control – risking your bottom line and reputation. Sourcing from multiple manufacturers risks inconsistent product quality, with each supplier likely using different material grades or processes. For example, in cases where multiple components from multiple suppliers are required for one end-product, if errors occur with one supplier’s component, this can cause headaches around agreeing responsibility for footing the bill to remedy or rework elements.
Streamlined supply chain in practice:
At ADS we support businesses to streamline their production processes. Our clients take advantage of all our services – from buying in cut-to-size materials; laser cutting and folding components; fabricating, painting and assembling; then storing and delivering products.
As the main point of contact for each aspect of the process, responsible for production from start-to-finish, we’re able to maintain consistent communication and offer updates throughout, preventing any misunderstandings or unnecessary delays.