
Trumpf, has been at the forefront of laser metal fusion and deposition technology for many years, will focus on the huge scope of its additive manufacturing range at TCT 3Sixty 2023. Its machines and systems are used for producing a wide spectrum of parts from large structural components for the aerospace, automotive and energy sectors down to smaller complex medical implants and dental components.
Uniquely, all elements of the TRUMPF machines and laser systems are produced in-house. The laser beams sources for all TruPrints are manufactured in the UK by TRUMPF. Not only does this allow UK customers the best combination of features for any given application but it also ensures the systems are fully optimised and integrated to give customers a clear competitive edge.
The latest innovation is the TruPrint 5000 Green Edition which is based on the previous TruPrint 1000 Green Edition concept but with increased build volume of 300mm x H 400mm and higher productivity. With the green wavelength (515 nm), the TruPrint 5000 Green Edition has the right tool for printing highly reflective materials such as copper. This opens up new opportunities for manufacturing induction coils, components for complex cooling applications, and for products such as high-performance heat exchangers for power electronics and optoelectronics, as well as electric motor development and further high-end applications that can benefit from the highly conductive properties of copper.
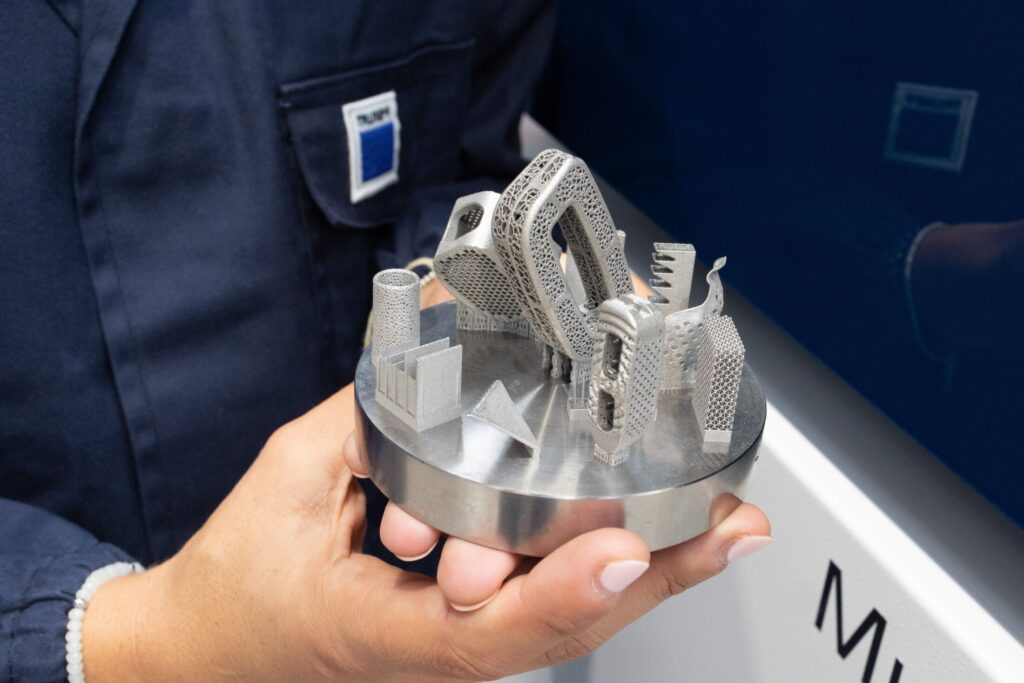
Also new to the product portfolio is a newly designed TruPrint 1000. The new design is optimally structured so that the machine fits through a standard door and can find its place in any laboratory, e.g. in the dental field or in universities.
Even higher productivity and premium quality, thanks to the full-field 2x 200 W multilaser and completely redesigned homogeneity of the gas flow. The 3D printer is intended for processing metal powders using the laser metal fusion process, also known as Powder Bed Fusion.
Due to the high level of robustness and quality in 3D printing, the TruPrint 1000 is not only perfectly suited for the dental market, but also impressive in the R&D area or in small series production.
These developments demonstrate how the ever-expanding breadth of TRUMPF additive manufacturing technology gives manufacturers the freedom to design and produce whatever they need. It enables structural components with the highest material requirements to be produced, coated and repaired and elaborate shapes and individual components to be manufactured fast, flexibly and cost-efficiently. And not just in one-offs or small batch sizes but right up to volume production.