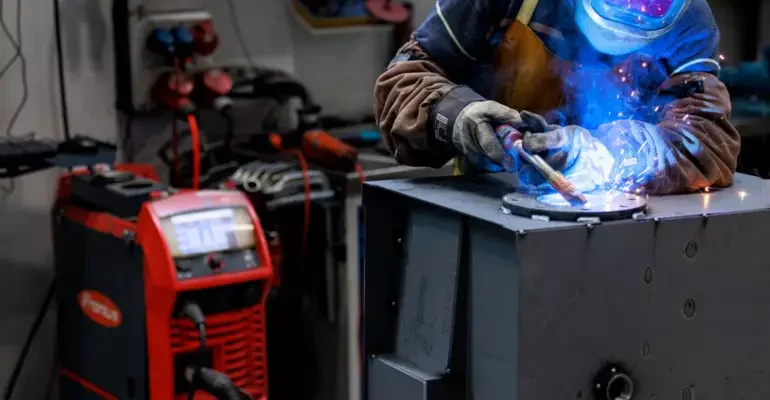
Founded in 1970 by Walter Knoll as a one-man company, today more than 1,100 employees manufacture advanced industrial systems in Germany, Poland, China and the USA. Welding is carried out with the Fronius TPS 320i, a reliable welding machine that leaves nothing to be desired when it comes to handling, welding processes, and functions.
Knoll enjoys a leading position in terms of technology, quality and brand awareness. The Swabian family business is economically independent and creates added value for all companies in which metal is machined in the automotive industry, in energy and medical technology, in machine and plant construction, and in the aerospace sector.
High Real Net Output Ratio
The advanced solutions optimize the performance of many machine tools. Resource-conserving cooling lubricant cleaning systems, chip conveyors and pumps are produced. The product range also includes central systems, which are individual pieces of equipment linked to form one system. They are required for the fully automatic transport of chips and cooling lubricants to central processing plants. Automation solutions for assembly lines and intralogistics are another mainstay for Knoll. Examples include assembly conveyor belts, automated guided vehicles or cobot solutions.
Joachim Riebsamen, Shell Construction Production Manager says, “As a solution provider, we offer all the necessary services from a single source: from project planning and manufacturing, to commissioning and service. We believe that good customer relationships are based on transparency and trust. That’s why we don’t just rely on a website, brochures and sales pitches. In-house machining allows us to convince potential customers about the advantages of our products using real operations.”
Due to the high real net output ratio, Knoll retains the majority of the added value in its own company. It significantly reduces logistics requirements and all associated CO2 emissions in a way that is both cost-effective and sustainable.
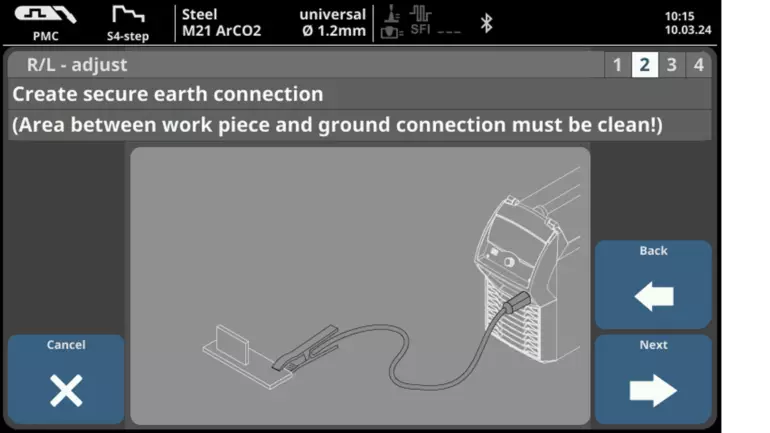
The Challenge of Thin Sheet Welding
Many components are welded by hand in shell construction. Sheets with different wall thicknesses up to 25 mm are used during this process. For coolant cleaning and conveying systems, the Knoll experts mainly use S355 steel, which is joined with the shielding gas M21 (82% Ar/18% CO2) and the wire additive SG3 (G4Si1). The company’s own WPS (Welding Procedure Specification) provides the basis for parameterisation.
“One of our biggest welding challenges is the processing of thin sheets,” explains Holger Kleck, foreman in the welding technology section. “Our components have a material thickness of 1–6 mm and warp relatively quickly. So we have to use low-warpage welding with little heat input. We often manufacture visible parts that not only need to be perfect from a metallurgical perspective, but also need to have seams that look good. We want to avoid uneconomical reworking in these areas at all costs. As a result, we mostly need spatter-free welding with a low seam build-up. For us, the Fronius TPS 320i welding machine offers the best solution for all these requirements.”
When joining thin sheets, the experts at Knoll rely on the pulse welding process. This is characterized by low spattering and reduced distortion. The intelligent MIG/MAG pulse synergic function of the TPS 320i offers Knoll specialists a pulsed-arc process with controlled material transfer. In the base current phase, the energy input is reduced to such an extent that the arc only just burns steadily and preheats the surface of the workpiece. In the pulsing current phase, an accurately controlled current pulse ensures targeted droplet detachment. Both phases result in precise, low-spatter welding across the entire power range. Unwanted short-circuits with simultaneous droplet explosion and uncontrolled welding spatter are almost excluded. The SFI (spatter-free ignition) also helps to avoid unnecessary spatter.
“When pulse welding with the TPS 320i, the arc remains very stable even at low amperage,” adds Kleck. “If we need rippled seams, we can use the SynchroPuls function, in which the welding power changes cyclically between two operating points. All in all, our long-standing partnership with Fronius has really allowed us to optimize our welding processes. We will continue to rely on the Austrian company in the future. The welding machines are advanced and easy to maintain. If we need support, we don’t have to wait long.”
TPS 320i: the Welding Machine that Uses Clear Language
Over 70 manual welding workstations at Knoll are equipped with the advanced welding machine. It is easy to operate thanks to a customisable 7-inch touch display, penetration and arc length stabilisers and the fact that it can be expanded with task-specific software packages known as Welding Packages. Examples of this include LSC (Low Spatter Control), PMC (Pulse Multi Control), and CMT (Cold Metal Transfer). Welders can log in with their own NFC card and access their personal authorisations and settings.
The menu navigation is available in over 30 languages. Considering that Knoll is using more and more welding professionals from other countries due to the increasing shortage of skilled workers in Germany, “native speaker welding machines” are extremely helpful. Not only is the welding machine’s display multilingual, it also uses clear language. Detailed descriptions and graphical animations provide welding specialists with a step by step guide, for example, in resistance alignment.
The TPS-320i variant used with integrated wire-feeder is ideally suited for welding tasks to be carried out manually. This device’s particularly simple wire threading process, which takes just a few steps, is a huge plus and makes everyday life easier for welders.
All Parameters at a Glance
The welding machine is operated with a central rotary push-button combined with a touchscreen. The quick change function that allows users to switch between properties, processes and functions is particularly practical. If you touch the respective prompt on the status bar of the display, you can immediately access the available parameters.
On the central display of the TPS 320i, the specialists can see all the relevant control variables and adjust them one by one. Innovative animations support the welding specialists when entering parameters. For example, there is a graphical representation of how a-dimensions change as arc length corrections are made, depending on whether a positive or negative correction is entered. The “synergic function,” which automatically detects how settings and corrections affect other relevant parameters, is responsible for this.
Easy Jobs and WeldConnect App
Even if the operation is carried out with welding gloves, the machine responds perfectly. Recurring parameter combinations for specific tasks can be saved as personalised easy jobs at the touch of a button. For example, when welding a 3 mm thick steel plate, job 1 is used. If you are welding a 5 mm thick chrome-nickel plate, use job 2. If a JobMaster welding torch is used, these jobs are available directly on the welding torch. The practical Fronius WeldConnect app for Android and iPhone is helpful for setting the welding specifications. As soon as the base material, filler metal and shielding gas have been scanned using a QR code and the weld seam profile, material thickness, welding process and welding position have been entered on the mobile phone, the welding specialist can use NFC (near-field communication) to transfer the calculated values to the TPS 320i or to a mobile phone belonging to another employee, who in turn transfers them to his/her welding machine.
Robot Applications Make Welding Attractive at Knoll
Welding does not necessarily have the best image. The profession is often associated with noise, harmful welding fumes and monotony. At the same time, the job is quite demanding, at least when robots come into play. Then, in addition to welding knowledge from electrical engineering to metallurgy, programming skills are also required. There is huge demand for welding technicians who know how to program robots, and they are well paid.
Many companies, including Knoll, now create their welding programs offline, i.e. separately from the robotic welding system on a PC or laptop. This not only minimises downtimes, it also offers the big advantage of welding simulation on the digital twin. In this process the software identifies axis limits, calculates starting points, limit positions and journeys, and sets teaching points independently. Obstacles are visualised and welding torch positions corrected on time, before the first weld is made.
Knoll now also uses a cobot system. It is easy to use and does not require traditional programming skills. If you want to create a weld path, you move the welding torch point by point along the joint line and save the points one after the other. The weld path and sequence are automatically calculated by the software, recorded, and are permanently available for later jobs. The system at Knoll uses CMT technology. Due to its extremely stable arc, combined with reduced heat input and low spattering, today the renowned “cold” MIG/MAG welding process from Fronius is used worldwide in plant, machine, power plant and automotive construction, in the aircraft and food industries, and in medical technology. It plays to its unrivalled strengths, especially when it comes to thin sheet welding.
“Operating cobots is intuitive and has a certain fun factor. This is especially true for young welders. They think cobot welding is cool; among other things because it is as easy as using a smartphone. Anyone who is familiar with using a smartphone can operate a cobot within a few hours. If this is enclosed and equipped with a fume extractor, the welding specialists are also protected against unhealthy welding fumes,” says Kleck, sticking up for cobots.
Quality-oriented but with a Heart
Precision is close to the hearts of the two managing directors Matthias and Jürgen Knoll, including during welding. This means that they need specialists who uphold the company standard. Being aware of this, Knoll believes that the company’s success is above all the sum of the performance of many skilled employees who give their all for the company. Profits are used for site development and are reinvested in the company. At Knoll, they think ahead in terms of generations, not just quarterly figures. The region and the employees benefit from this.
Health and Safety Are a Top Priority
Healthy employees are not a given, and neither are committed ones. Since one depends on the other, Knoll uses ergonomic workstations and the best possible personal protective equipment. All welding tables are height-adjustable, and automatically darkening welding helmets plus fresh air supply have long been standard. In addition to this, the room air is renewed four times per hour.
“Workplace ergonomics is an important topic,” Riebsamen explains. “Not only in terms of health, but also from a profitability perspective. Simple, individualised operation, short distances between the component and the welding machine: all this has a motivating effect, saves valuable time and increases the productivity of welders.”
Of course, component safety and quality also play a crucial role. The experts at Knoll therefore apply various testing methods, such as dye penetration testing (PT), to check each individual component. This is a fast, effective method that shows up surface cracks and other defects such as pores. It is also suitable for complex geometries and can be carried out on workpieces of all sizes. Even small errors that are not visible to the naked eye can be detected with PT and then corrected by the welding specialist.
During the dye penetration testing, a fluorescent dye is applied to the surface of the workpiece to be tested. This penetrates into existing cracks, pores and defects. It is then illuminated with a special lamp or sprayed with a developer. Any defects are immediately visible to the examiners because they are surrounded by the fluorescent dye.