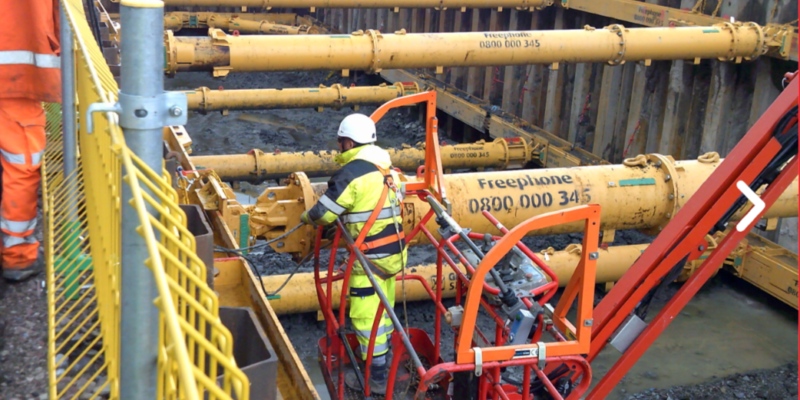
Project Overview
Bama Fabrication Ltd was contracted to support a deep excavation project in the South of the UK. The job required the installation of a complex structural support system, ensuring the stability of the excavation for subsequent construction works. The project is currently ongoing, with continuous monitoring and adherence to strict safety protocols. The work is being carried out using a highly skilled team comprising experienced welders, erectors, and slinger signallers, ensuring precision, efficiency, and safety throughout. This was a collaborative project with MJ Church, Balfour Beatty and Babcock.
Project Scope & Execution
The project involves the fabrication, assembly, and installation of large-scale steel struts and bracing frames supplied by Groundforce Shorco. Key tasks include:
- Erection and alignment of steel bracing structures to maintain excavation stability.
- Welding and securing of critical joints to ensure structural integrity under heavy loads.
- Rigging and lifting operations using slinger signallers to safely position steel components within the excavation.
- Collaboration with site engineers to maintain alignment accuracy and compliance with project specifications.
- On-site adjustments only after approval from key engineers and health and safety officers to ensure safety and compliance.
- Daily safety checks of hydraulic components to guarantee the ongoing stability and safety of the excavation.
- Conducting daily briefings and welfare meetings to ensure team awareness, coordination, and well-being.
Challenges & Solutions
- Deep excavation complexity: The project requires precise placement of heavy structural supports in a confined and deep excavation. This is managed through coordinated lifting operations and strict adherence to safety protocols.
- Adverse ground conditions: Uneven terrain and loose material pose a challenge during installation. The team uses advanced surveying techniques and pre-fabricated components to expedite installation while ensuring stability.
- Logistical constraints: Delivering and handling large steel components within a restricted site requires careful planning. Detailed logistics coordination ensures timely deliveries and efficient workflow.
- Safety and compliance: Continuous safety monitoring is in place, with daily hydraulic checks and strict adherence to engineer-approved adjustments to maintain a safe working environment.
Expected Outcomes:
- Successful completion of all structural bracing components within the designated timeline.
- No recorded safety incidents through strict adherence to daily safety checks and compliance with health and safety regulations.
- Seamless integration of fabricated elements with on-site requirements, reducing downtime and ensuring project continuity.
- Positive engagement with the workforce through daily welfare meetings and briefings to enhance safety awareness and team cohesion.
Conclusion
Bama Fabrication Ltd continues to play a critical role in the success of this excavation support project. The company’s ability to manage complex installations, adhere to strict safety protocols, and execute precision welding and erection works reinforces its reputation as a trusted partner in the UK’s construction industry. This case study highlights the expertise and efficiency of our workforce in handling large-scale infrastructure projects with confidence and skill while maintaining the highest safety standards.
For more information about our bespoke metal fabrication services, please contact us today.