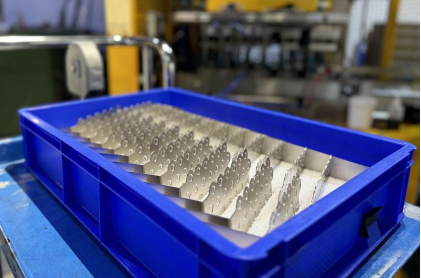
An innovative new production process developed by Redditch based Samuel Taylor Limited (STL) has successfully enabled the production of over 70,000 busbars for the battery packs of the world’s first fully electric British hypercar.
Busbars are an integral part of EV battery packs. Improving the busbar can lead to lighter packs, extended range, and greater power output.
One of STL’s success stories involves producing the dual thickness, contacted busbars used in smart meters. Utilising this core competency, STL partnered with a leading developer of EV battery modules from the offset to design and build a pilot scale stamping line for their EV battery, working to produce 10,000 initial prototypes.
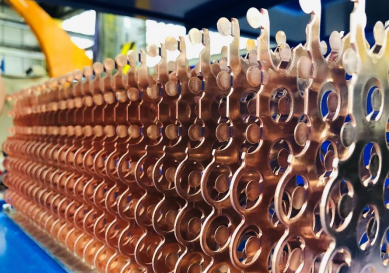
This was followed by the development of a brand ]new dual-thickness method of manufacture to enable scalable production of a total of 70,000 busbars in accordance with stringent quality requirements.
An evolution of this technique is now being used on prototype shunt for a different application being developed by STL and a Cambridge based design house.
Aaron Ball, Engineering Manager at STL explains: “The end user specified the design of the product, which was difficult to achieve. This was a unique case, with the application being the world’s first fully electric British hypercar and the most powerful car to enter series production.
“In parallel to assisting with a completely new design for a busbar, we have also been able to innovate to create a brand-new production process. This process enables us to consistently meet the stringent tolerance requirements. There was no blueprint for this, as it is the first time that a process like this has ever been developed for busbar manufacture”.
STL believe the new production process to be significantly more accurate than simply stamping the component out with a traditional press tool, achieving a +/-0.020 on the dual thickness tolerance on the weldable connector tab.
Ball continues: “We helped the customer achieve a manufacturable route for the product that they wanted. This is the perfect example of the value in getting STL involved within the prototyping phase before mass manufacture commences. Without STL’s expertise regarding the principles for progression press tooling at the prototyping phase, it is unlikely the component could be manufactured to the desired requirements.
“The car is very specialised producing over 1500kW of power (equating to over 2000hp), as such this power requirement from the battery pack meant we could not use what is now becoming the industry standard – a lamination busbar – we instead had to create our own process to deliver the dual thickness busbar the customer needed.”
A lamination busbar involves a thin lattice structure which attaches like a web to all cells, along with a carrier plate on top which acts as a heat sink and gives the busbar rigidity.
However, a standard lamination busbar would not have been able to deliver the amount of current that is to be drawn out of the modules for the hypercar battery pack, with it being around four times higher than a performance EV. This would restrict current flow, and build up heat, leading to thermal problems within the battery.
This led to a total rethink of component production, with STL opting to manufacture the component from pure copper whilst reducing the thicknesses locally where required.
“We made certain adjustments within the stamping process to increase the accuracy of busbar production. For example, we established a customised press line to produce busbars with the ability to switch modules on and off, enabling us to deliver optimised pressure but spread over a row of two or three cells – a pattern that repeats row by row through the part.
“We also had to integrate feeding control into this process, so that we can re-strike the same stage multiple times. This meant that we could finely balance the control over those two or three impressions, vastly reducing our tab thickness variation to meet the requirements of the component. This is critical for the laser welding that happens afterwards. The sequential control and timing of this process was therefore incredibly important.
“Post processing, we are 100% inspecting every component, adding threaded inserts & fasteners as needed, plus verifying that they meet the required tolerances and that we do not have any deterioration within our production process”, adds Ball.
Whilst developing the new production process, STL’s primary objective was to meet the requirements of the end customer.
A secondary objective was to ensure the process was scalable to enable the production of between 500,000 to 1,000,000 busbars per annum and could therefore be utilised more widely within the high-volume production of electric vehicle batteries.
“The press can create four to six components per minute, or one part every ten or fifteen seconds – depending on which component we are making. We have currently set up the process to run a total of eight different components, four of which are the live components within the hypercar project.
“Essentially, what we have developed is a series of modules that can then be re-used for other purposes, using different punches, dies and configurations.
“The beauty of cylindrical cells within battery packs is that there is only one optimised arrangement, meaning the same pattern on a busbar. We can respond to differing needs because we have a fixed start point and can then tailor the process based on requirements for cell-diameter and the length of the busbar. We only need to create a module to cut the part off. This means we are well placed to produce busbars for a variety of different battery pack designs, to meet various range, performance or voltage requirements” concludes Ball