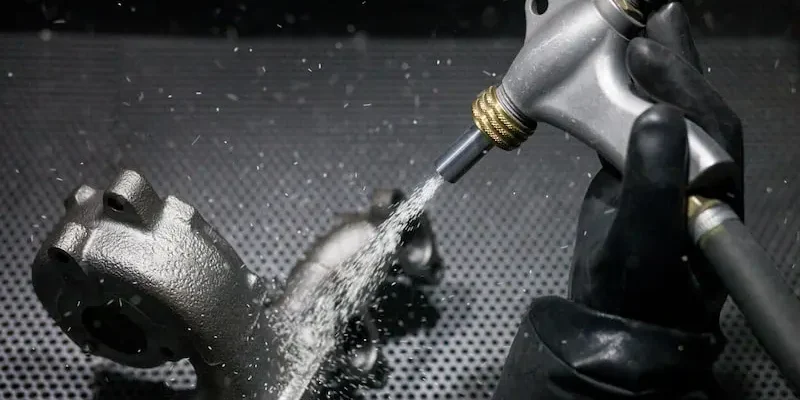
Shot peening is a cold working process that alters the mechanical properties on the metal’s surface and creates a compressive residual stress layer. Its primary purpose is to prevent the spread of microcracks on a surface. Shot peening also improves a material’s fatigue resistance, strength, and durability, making it effective in increasing its service life.
Shot Peening Process
Shot peening is a cold working process that subjects the material’s surface to plastic deformation using peening media. The process uses shot media that generally comes in the form of steel, ceramic, or glass beads. This media is bombarded onto the part’s surface at high velocities, generating enough force to compress the surface and create small indentations. It converts the residual tensile stress into beneficial residual compressive stress which improves the material’s strength under load.
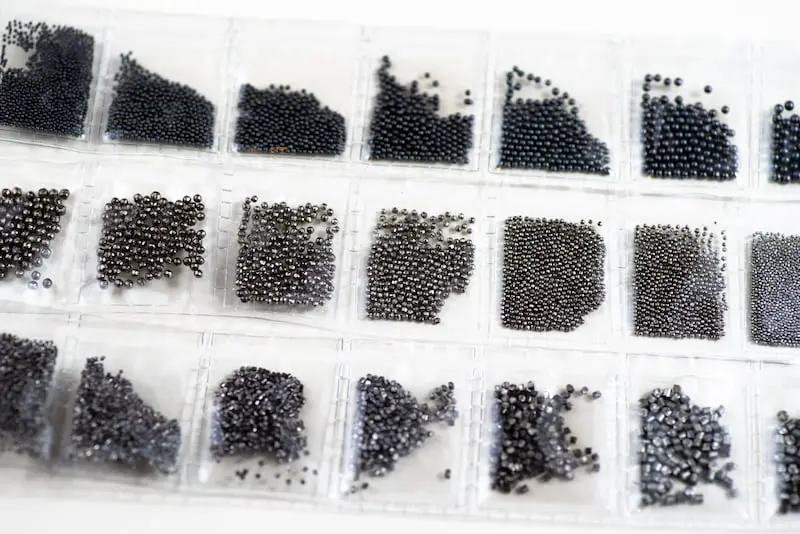
The application of the shot media may either be delivered using compressed air or a wheel turbine. The principle of shot peening remains the same with both types of equipment. Factors such as coverage, intensity, angle, and shot quality have a way higher impact on converting tensile stresses to compressive residual stress than the chosen process type.
Each shot particle hits the component’s surface at around 30 to 100 m/s, encasing the layer with residual compressive stresses. Plastic deformation, enabled by shot peening can also correct the surface roughness of a workpiece. Thousands of indentations compress and strengthen the metal, making it more resistant to failure. A correctly shot peened component will last longer and have higher maximum load capacities. Too much peening may induce excessive cold working though, which can lead to fatigue cracks and lower fatigue strength in return.
An Almen Strip Test can be performed throughout the shot peening process to measure the intensity of each shot particle. This test uses a flat strip bombarded by a shot stream which is usually adjusted through a shot flow controller. An Almen Gauge measures the bentness of the strip which determines the intensity.
Separators are used for the recovery of used media and removal of shot fragments. Feeders replace the number of damaged media for operation.
Other uses of this process include shot peening forming, a method in which the component is slightly bent from the force applied. It may be used for thin panels, skins, and wing flaps. Shot peening may also be used for correction of distortion which aims to flatten surfaces (opposite of forming).
Portable shot peening or flap peening is used for extremely difficult areas or repairs (mostly aircraft). It consists of a kevlar matrix with a flap of balls that are propelled pneumatically or electrically to the targeted area.
Shot Peening Media
There are various forms of shot peening media used to generate compressive stress on the material surface. Each has its own HRC (Hardness Rockwell C Scale) value which impacts the amount of force applied to the surface.
- Cast steel shots (40 ~ 50 HRC) are round metallic in shape and are made from steel scrap and alloys which are melted at ~1650°C (3000°F). Quenching, tempering, and other heat treatments are used to manufacture these steel shots to achieve the desired hardness. Cast steel shots are suitable for most peening intensities of ferrous and non-ferrous metal components. The major downside of a cast shot is the fact that it may shatter into sharp steel fragments at high speeds/forces, damaging the component.
- Ceramic shots (57 ~ 63 HRC) are pills made from approximately 67% zirconium dioxide, 31% silica, and 2% aluminium oxide. They have an extremely high density and hardness which makes it optimal for increasing the surface hardness of non-ferrous metals such as alloys of aluminium and titanium.
- Glass beads (>40 HRC) are made from soda lime which can come from scrap glass. The glass is crushed, melted, and formed into spheres. Glass beads are primarily used for aluminium, magnesium, titanium, and other ferrous metals. Peening with glass beads may be used as a secondary process to steel shot peening to remove iron from the surface and improve the part’s smoothness.
- Cut wire shots (50 ~ 60 HRC) are cylindrical with rounded edges and are homogenous in their composition. A cut wire shot is obtained from a cutting wire that is divided into equal lengths relative to its wire diameter. This type of shot peening media is quite popular due to its low surface contamination, solid and uniform hardness, and no dust generated. It is used for ferrous and nonferrous applications but is ruled out when small-sized shots are needed. It leaves a consistent peening intensity on the surface and is unbreakable, unlike other media. Cut wire shots may come in the form of aluminium, carbon steel, copper, stainless steel, and zinc.
Shot Media Considerations
There are quite a few variables to consider when selecting shot media aside from its type. These considerations are done in comparison to the properties of the workpiece and its desired outcome.
- Shot velocity
- Shot flow
- Shot size
- Shot hardness
- Conditioning
- Exposure time
Some other parameters to consider are generally associated with the peening equipment used. Air blast systems, for example, have to account for the nozzle speed while centrifugal systems should consider the wheel speed.
Shot Peening Methods
There are two main methods to send shot media to the metal surfaces:
- Air blast systems eject media through a nozzle directed at the targeted surface using high-pressure compressed air. The shot particles travel through the nozzle at high speeds, effectively targeting the area to be peened at great precision.
- Centrifugal blast wheels use a high-speed paddle wheel to bombard the metal surface. Shot media is introduced into the centre of the spinning wheel and is propelled towards the targeted area on the workpiece by paddle wheels utilising centrifugal force.
There are, however, other methods available such as laser shock peening, ultrasonic peening, and wet peening, that are used for specific applications.
Shot Peening Applications
Shot peening is widely used to increase resistance to fatigue, including stress corrosion cracking, cavitation erosion, intergranular corrosion and also resistance to repetitive loading cycles. The compressively stressed zone squeezes the grain boundaries of the metal minimising the amount of fretting, galling, spalling, and wear on the workpiece.
The compression stresses that resist metal fatigue help prevent the propagation of cracks on the material’s surface. Tensile stresses inside the material are not as problematic as the cracks are far less likely to start propagating from the inside of the material.
Many industries such as automotive, aerospace, machinery manufacturing, and medical utilise the shot peening process as it is an economical and practical way to improve the fatigue life of a component. Springs, gears, camshafts, drills, and turbine blades undergo this cold working process to achieve resistance to cyclic loading. Shot peening removes debris and smoothens the surfaces of cylinder heads and engine blocks. Blasting shot media through a liquid or powder may also be used to embed surface coatings onto the material.
Shot Peening vs Shot Blasting
Shot peening and shot blasting are two different methods that have different purposes. These two might seem similar as they both use shot media at high velocities, but the techniques differ in several aspects.
Shot peening is used to improve the mechanical properties of the material by increasing its strength, minimising the risk of failure. The purpose of the shot material is to increase fatigue life, much less than improving its aesthetics. Shot peening may be used in embedding coatings and lubricants to metals to achieve its desired surface coating.
Shot blasting is used in preparation for other surface treatments such as heat treatment and painting. It improves the texture of the material’s surface, removing dents or imperfections that can sometimes arise during production. The media used in a shot blast stream is generally more abrasive than in shot peening. Shot blasting may also use other abrasive shot media such as silicon carbide, copper slag, and aluminium oxide to achieve the desired surface finish.
A part can undergo both processes in the manufacturing procedure if required by the project.
Wrapping It Up
Shot peening effectively improves the fatigue life, strength, and durability of metal components. The induced compressive residual stresses on the material’s surface make it significantly more resistant to corrosion, crack initiation and wear. It is an essential method employed by various industries due to it being precise, fast, reliable, and rather inexpensive.