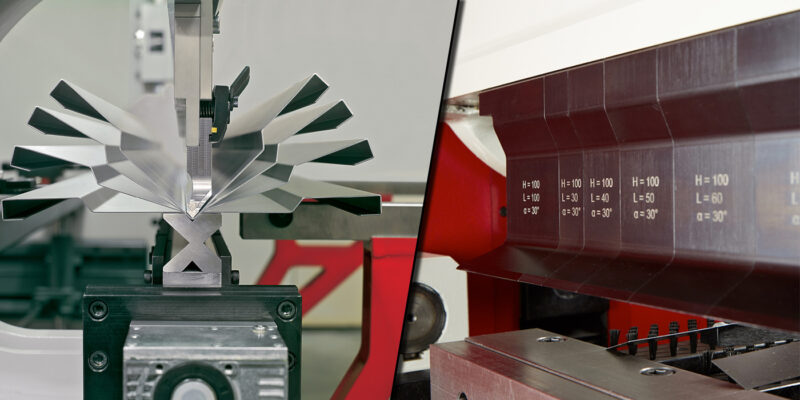
When adding bending capacity to a sheet metal workshop, the question comes up as to whether to purchase a press brake or a CNC folding machine. Actually a busy sub-contract sheet metal shop can save time and money by having both machines. So the question for you could be ‘why add a CNC folder to your plant list?’ For those making a product there are applications which favour either process, so it is helpful to review what these machines do differently.
Sometimes it’s two ways to the same end, but read on to find out the most important considerations……
WHAT DO THEY DO DIFFERENTLY?
A press brake works by using a top tool – or punch – to press the material into a vee on a bottom tool – or die – to form an angle. The majority of press brakes working today use the air bending method where the two shoulders of the vee die create three points with the tip of the punch to create the bend. A folder on the other hand clamps the material in the flat position and uses a folding beam to bend the material up in a rotary action to the desired angle.
VERSATILITY
A press brake is undeniably the more versatile machine. If your requirement is to handle a range of bending tasks from thin to thick material, without knowing what might come through the door tomorrow, then a press brake is likely to be the best solution. With the correct tooling, heavier plates can be bent on narrower widths within the tonnage capacity of the machine, while a large number of different tools are available for specific tasks such as hemming, over bending and joggling.
SO WHAT ARE THE ADVANTAGES OF A CNC FOLDER?
HANDLING LARGE OR HEAVY PARTS
When bending large parts on a press brake it will typically involve two operators to gauge the material and support it during bending. This greatly increases cycle time, manual handling and risk of injury, all of which can be avoided on a CNC folder with a back gauge table. In this case the material is continuously supported and the operator merely has to position the material against the back gauge fingers.
WORKING WITH VERY THIN MATERIAL
When gauging longer flanges in very thin material on a press brake, the material can drop down under its own weight before meeting the back gauge. While you can often program the machine to use the back gauge finger as a support, it is still quite slow and awkward work. On the folder, with the material continuously supported, this issue is completely avoided.
BENDING SMALL FLANGES ON LARGE PARTS
An application at which folders excel is when there is a requirement to bend small flanges on large sheets. With a press brake the majority of the sheet will be out of the front of the machine, probably requiring two operators to handle it. On the folder only the flange to be bent will be out of the front, with the rest of the material resting on the back gauge table, therefore ensuring accuracy and avoiding distortion from the weight of the sheet.
BENDING A RANGE OF APPLICATIONS WITHOUT CHANGING TOOLS
While a press brake may need tool changes to cope with different material thicknesses and bending angles, a folder will bend all angles and thicknesses – within the capacity of the machine – without any tooling changes. This is a significant time saver, especially when doing small batch work or interrupting production with an urgent off-cycle part.
USING COATED OR SENSITIVE MATERIAL
Folders are also very effective at bending polished, coated or other sensitive materials, as the part remains clamped securely while the folding beam creates the bend, resulting in little or no marking of the material. Press brake tooling can significantly mark material resulting in damaged parts or a secondary clean up operation, although operators will try to prevent this using non-marking film.
ALREADY RUNNING PRESS BRAKES? FREE UP YOUR MACHINES FOR WHAT THEY ARE BEST AT!
In situations where press brakes are tied up producing large parts using two operators, it can make sense to move production of these parts to a CNC folding machine where they can be produced by one operator. This leaves the press brake free to work with smaller, complex parts in thicker material and higher batch quantities which they excel at and also leaves an operator free for other tasks.
SUMMARY
It is important to bear in mind that there are jobs that can only be produced on a press brake and vice versa; however for a significant number of applications you have a choice. Why not visit the Bison showroom to make a direct comparison? Please get in touch using our contact form or emailing us at [email protected]. Or simply give us a call to discuss on 01785 336732.