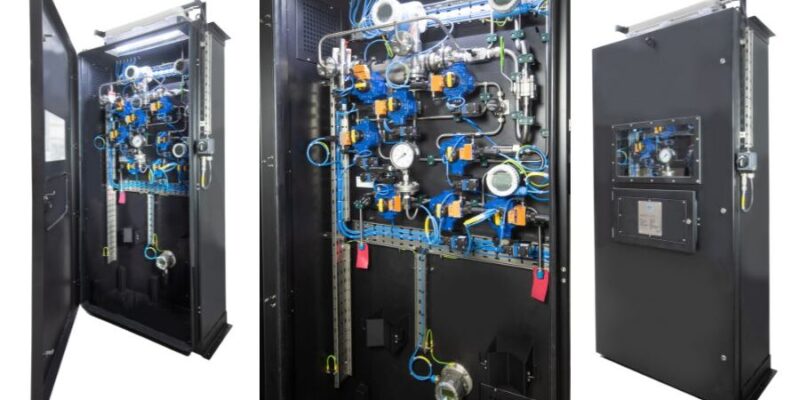
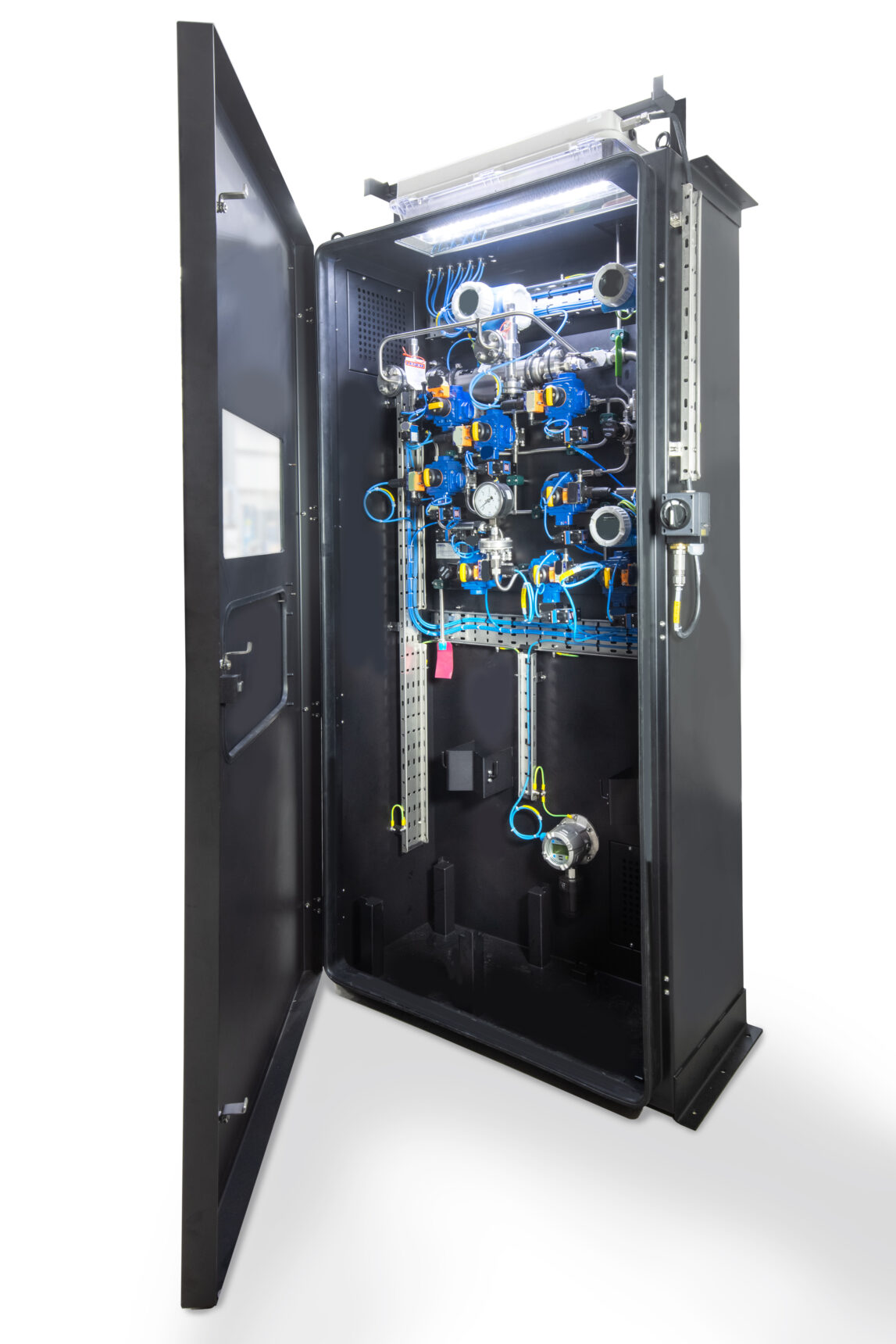
Howorth Air Technology, a customer of Orbital Fabrications, representing a leading pharmaceutical manufacturer, required a bespoke hydrogen chloride control system to be integrated into a solvent transfer process, and requested Orbital’s expertise in the design and manufacturing process. The new system needed to fit within a predetermined physical design envelope, as well as meet stringent chemical compatibility and durability requirements. This case study outlines the process of this project, leading to the successful delivery of the cabinet to the customer.
Once the P&ID was provided, Orbital Fabrications was able to design the bespoke hydrogen chloride control system to fit within the physical envelope of the provided Howorth Air Technology cabinet. All materials utilised in the project are C22 Hastelloy, to ensure chemical compatibility as well as resistance to corrosion and strong durability.
Enhanced seal integrity was a priority, with components being joined using precision welding techniques to eliminate any potential leak paths, and maximise the joint’s integrity. Additionally, selected valves were disassembled and retrofitted with superior seals by Orbital Fabrications, to enhance durability and longevity.
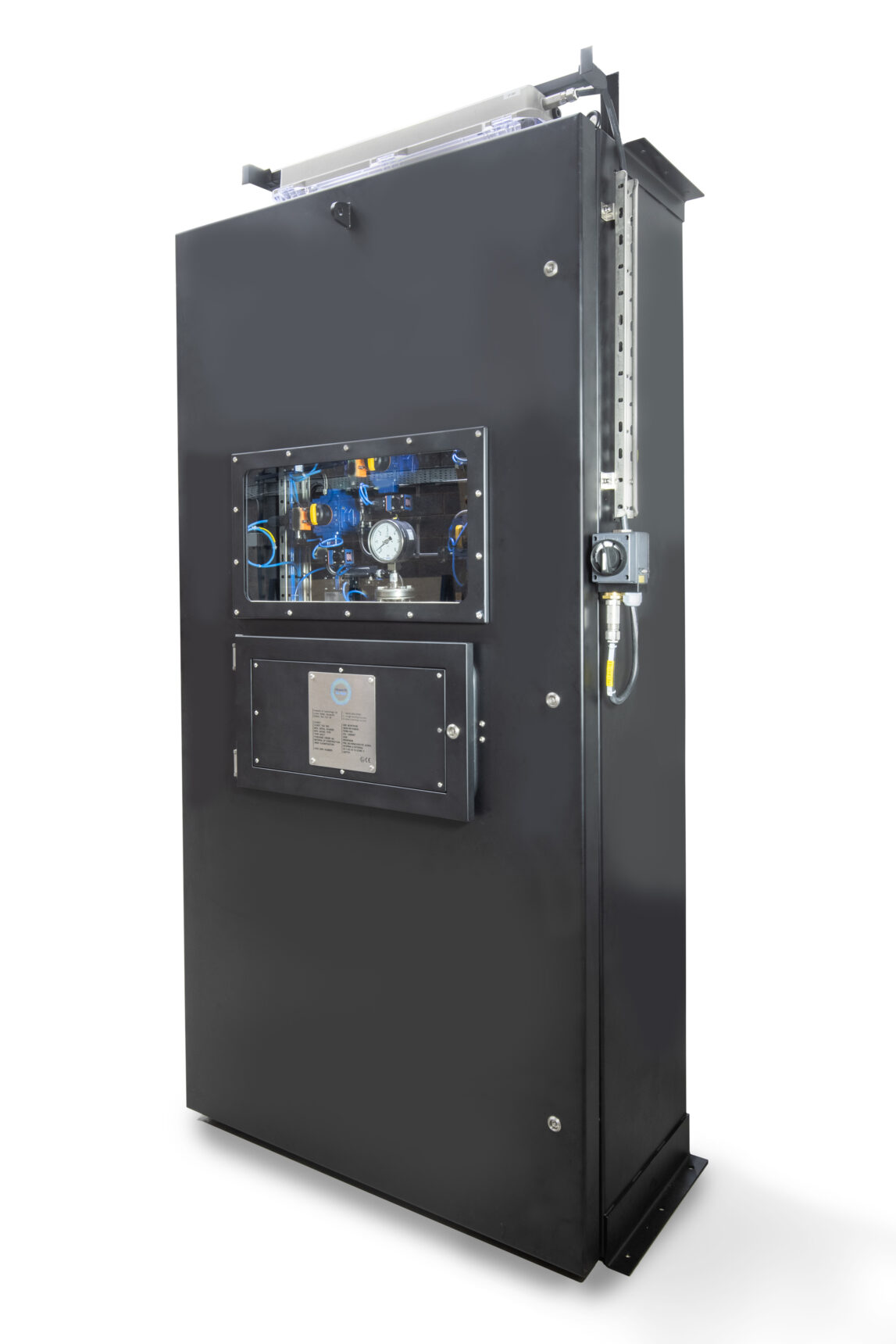
The system was housed within a cabinet provided by Howorth, which featured a specialist coating designed to further enhance chemical compatibility. This additional layer of protection ensured the cabinet’s resilience against the harsh operating environment.
The completed hydrogen chloride control system met the customer’s specifications exactly and exceeded expectations in terms of durability, reliability, and chemical compatibility through the use of C22 Hastelloy throughout the bespoke hydrogen chloride control system, as well as industry-leading welding techniques and quality.
The success of this project demonstrates Orbital Fabrications’ ability to deliver high-quality bespoke solutions for the complex demands of the pharmaceutical sector.