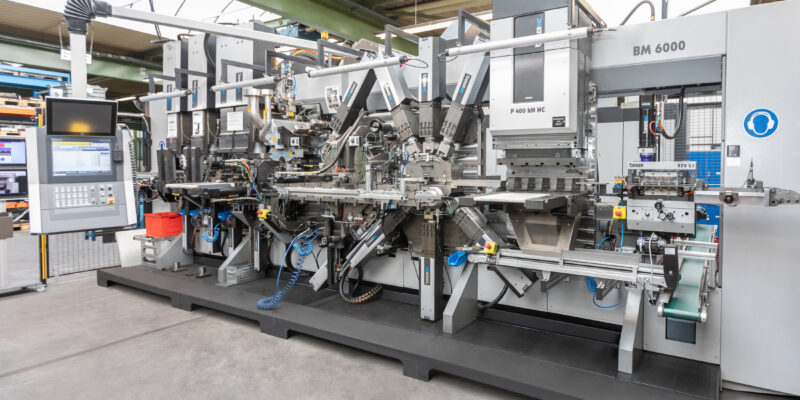
In times of increasing scarcity of resources and sharply rising material prices, material-efficient production with maximum productivity is of strategic importance. Otto Bihler Maschinenfabrik offers innovative process technologies for stamped and formed parts and assemblies that minimize material usage while maintaining consistently high component quality and system availability.
The constantly rising and at the same time strongly fluctuating raw material prices on the international raw material markets are constantly presenting metal processing companies with new challenges. In the processing of raw materials such as strips and wires, optimized production processes are therefore required to reduce raw material consumption. By optimizing existing processes and using new, highly standardized machine and tool solutions, large-scale potential savings can be achieved in production. In this way, corresponding investments pay for themselves within a very short time – and this applies to the production of all batch sizes. The development of innovative automation solutions with very high material efficiency is therefore at the top of Bihler’s agenda.
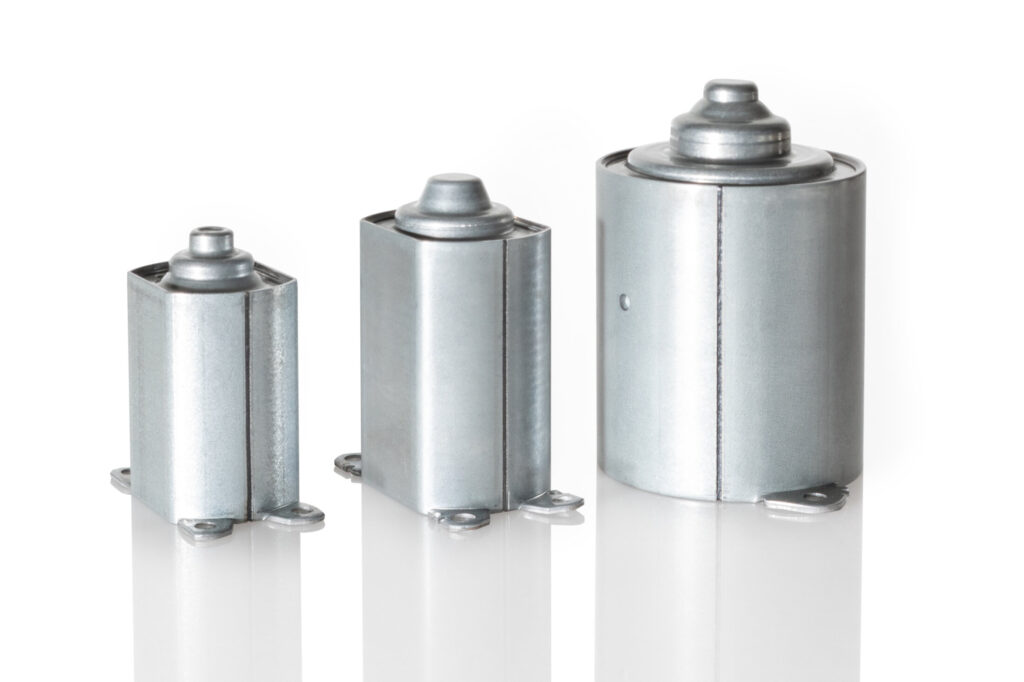
Stamping and forming plus instead of deep drawing
The objective was to move away from the material-intensive deep-drawing process towards resource-saving stamping and forming technology. In close cooperation with its partners Schürholz and BROSE, Bihler developed a new type of manufacturing process for electric motor housings in the wet area. These are used in window regulator mechanisms in car side doors. Until now the housings were manufactured purely as deep-drawn parts on presses. The disadvantage: a lot of material waste and lubricant was produced. This meant that it was no longer possible to keep up with the increasing price pressure on window regulator drives. The successfully implemented automation solution on a Bihler BIMERIC BM 6000 servo production and assembly system now provides a remedy. The motor housings are manufactured on this system in a continuous flow process from the starting material to the finished part.
The galvanized steel strip is drawn from the coil highly dynamically and precisely using the RZV 2.1 radial gripper feed. The blank is stamped in the 400 kN servo press, separated and then formed in a radially arranged forming tool. The components are then calibrated and the seam is welded by laser. The next step is to form the screw-on tabs of the housing by 90° and punch holes. The housing is turned and a step is sheared at the top end of the housing for the lid stop. The lids fed from the rear of the machine are placed onto this projection using a pick & place unit and then pressed to create an absolutely tight, form-fit connection. Finally, a camera inspects the component and a laser sensor checks the weld seam. The finished motor housings leave the system in a matter of seconds.
Cost- and weight-optimized production
The globally unique Bihler-Schürholz solution offers decisive advantages. Compared to the deep-drawing process, the net weight per motor housing has been reduced by 25 percent and the material costs by around 30 percent. This significantly reduces the impact of raw material prices for the company. Production costs have also been reduced. The lighter components also help to reduce the
weight of the vehicles, thereby reducing secondary CO2 emissions. Drawing oil can be dispensed with completely. In addition, in contrast to deep drawing, the new technology allows a wide range of material thicknesses to be realized easily and flexibly, and precisely across the entire housing body. Entire families of parts can thus be produced flexibly. The great success of the project also prompted Schürholz to commission another BIMERIC BM 6000 for the production of larger housings. These are also used in cars, but also in garage door drives and coffee machines.
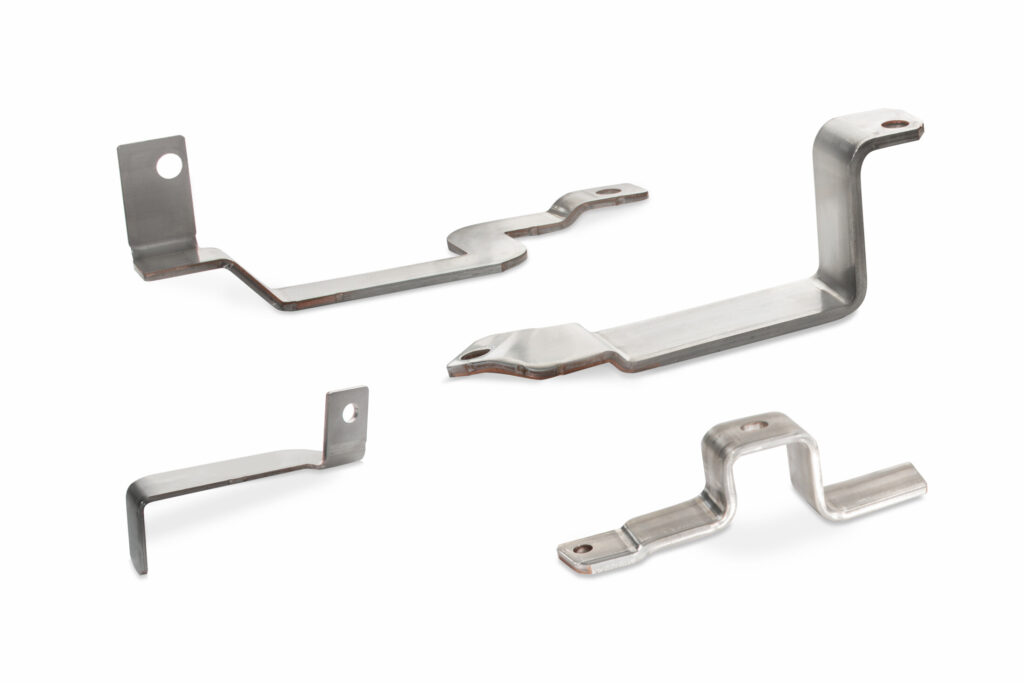
Busbars with 50 percent less material
In addition to motor housings made of steel strip, Bihler technology can also be used to manufacture busbars for power distribution in electric cars particularly economically from copper and save a great deal of material. As part of its reorientation towards e-mobility, a leading global automotive supplier contacted Bihler with the requirement to realize production options for a large number of busbar variants within nine months and at the same time meet the highest standards of material efficiency. The task was ambitious, but feasible with the implementation of the tools in the standardized LEANTOOL system. The efficient and flexible Bihler manufacturing solution, which the automotive supplier now uses to produce its busbars, achieved the desired result. Bihler was able to meet the tight schedule thanks to its network of LEANTOOL partners.
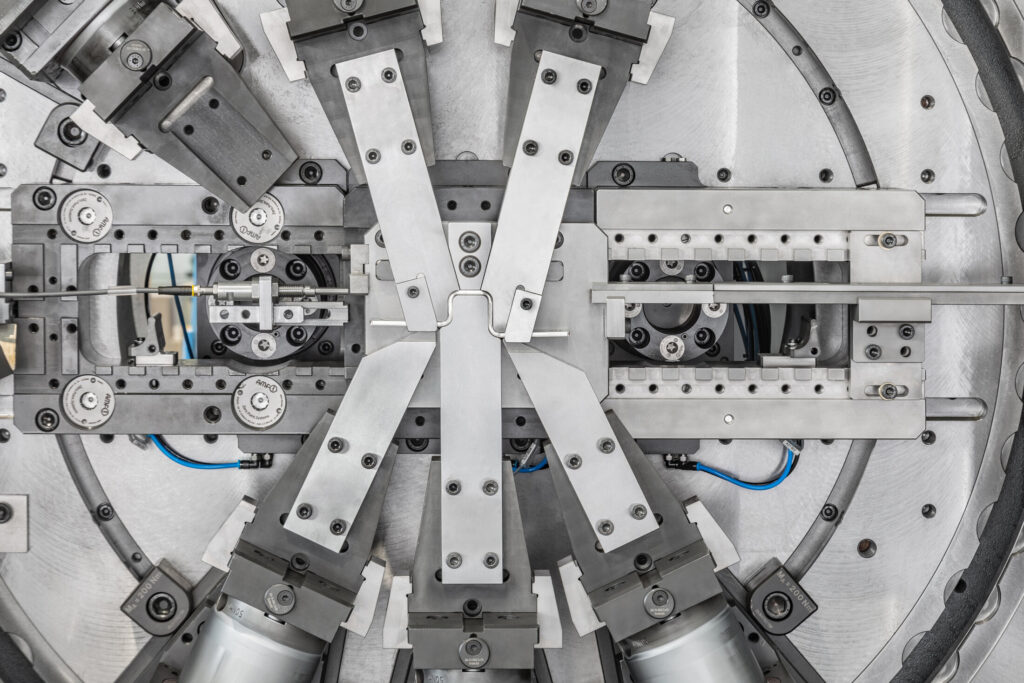
Radial and linear on one machine
The manufacturer only needs one GRM-NC servo stamping and forming machine for the different component variants. The universal machine is equipped with six NC units and two 400 kN presses. Half of the busbar variants are produced with radial LEANTOOL forming tools due to their geometries and smaller dimensions. With these, the NC units with the punches are arranged in a circle around the forming center. The big advantage: In radial production, the raw material width corresponds to the part width. In the case of busbars, which are made from four millimetre thick pure copper, this saves up to 50 percent of cost-intensive material compared to production with wide strip. Only one servo press with a corresponding number of standardized Meusburger cutting frames is used.
The other half of the busbars are produced using the LEANTOOL linear system due to their greater component length and the additional forming steps. Three L250 forming modules and two cutting frames in the two servo presses are available for each of the variants. In linear production, process lengths of over 2,000 mm can be realized on the compact GRM-NC for a large number of forming steps. The short changeover times from one variant to another are one to one and a half hours. Users also benefit from high material savings in linear production. This is up to 33 percent, as one carrier strip is sufficient in the production process. The radial and linear LEANTOOL forming tools also impress with their low number of components and their high proportion of standard parts of up to 70 percent.