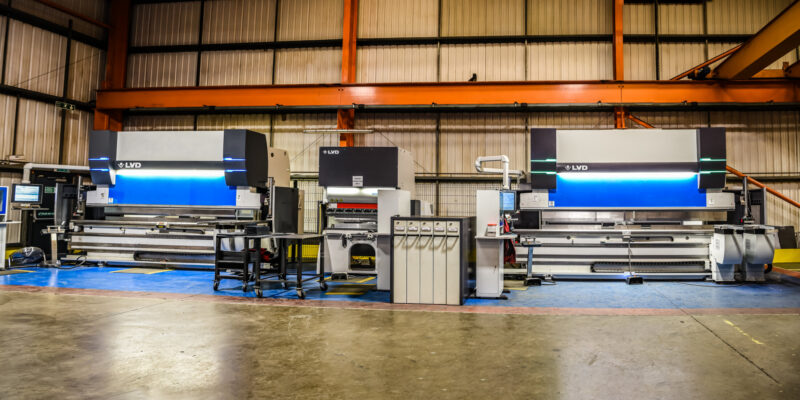
Investment in a new automated laser cutting system and associated software has doubled manufacturing capacity for swarf management systems produced by LNS Turbo’s factory in Wombwell, near Barnsley. This has allowed them to continue their strategy targeting OEMs and dealers rather than end users.
The £850,000 investment includes a 4kW LVD Phoenix fibre laser with a 10 station Compact Tower automation system for blank sheets and finished parts. Also included in the package are 4m 135 tonne LVD Easy-Form press brake and LVD’s CADMAN software suite.
These latest machines join an existing LVD Easy-Form press brake – which has been upgraded to be fully compatible with the latest software – and a small LVD Dyna-Press electric press brake.
Mark Scanlan, the European Chief Operating Officer at LNS, first visited LVD in Belgium five years ago and realised how its technology could transform manufacturing at LNS UK.
“I went to look at the equipment but immediately saw the software could give me another level of automation. When people talk about automation, they tend to talk about the machine tool, but LVD has a whole suite of software that makes our engineers’ job easier.
“This means they can automate the process of taking a 3D model, creating a 2D pattern, putting that through a CADCAM system and making a verified component that will be right first time. That was a big driver for the investment.”
“We got our first LVD press brake seven years ago and post-Covid we bought an LVD Dyna-Press, which is great for small parts. But I had always been pushing for the LVD laser with autochanger and a second press brake – and all the associated software to really automate the complete process.”
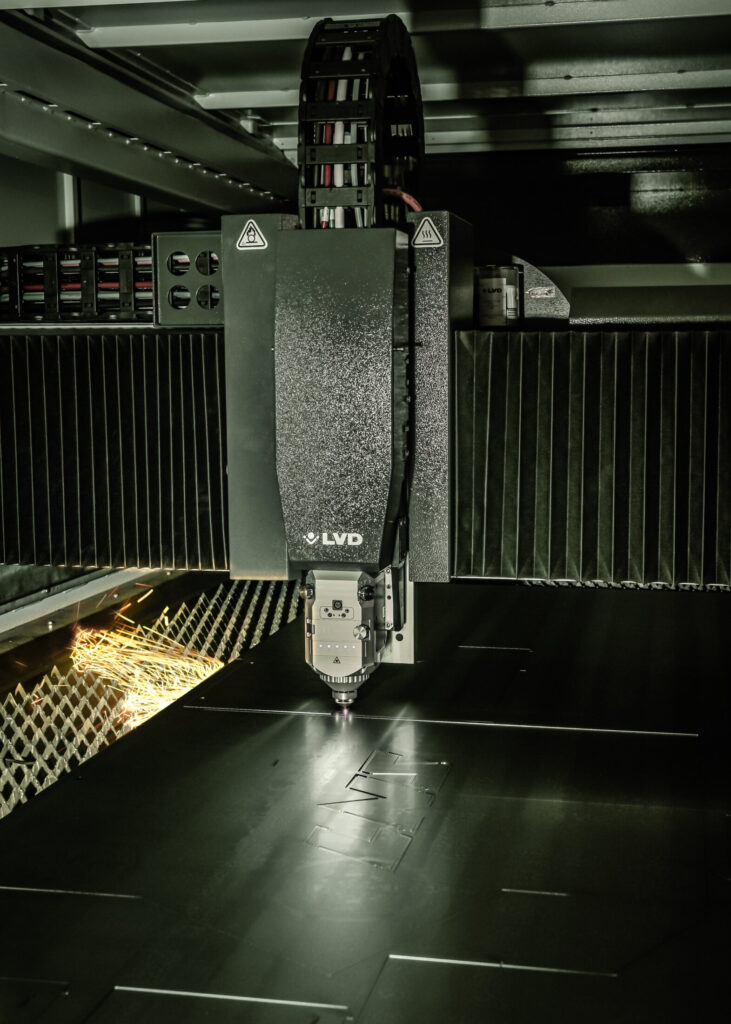
The new investment coincided with a change or ownership of the LNS group – which is now part of Swedish investment group Storskogen – and a new market focus.
This has changed the strategy from making one-off machines for end users to targeting machine tool OEMs and dealers where it could achieve economies of scale, and this required it to ramp up its manufacturing capacity.
As Mark explains: “We have changed our market focus from making machines per order for end users, to partnering with OEMs where you are focused on making higher volumes of similar types of equipment. To meet that demand for volume manufacturing we wanted to automate not just the physical manufacturing process but also the software behind it.
“With the new LVD laser and software everything is now focused on mass production – but with a high degree of variability. The Phoenix with the 10-station tower storing sheet and finished parts gives us the ability to work lights-out.”
“The whole laser package has enabled me to more than double my overall capacity from 240 machines a month to 500. The second press brake helps me to bend more parts, but the laser was the key.”
“The capacity increase was really important as it will enable us to have a greater presence in the OEM Market. But it was not just about capacity, it was also about upskilling people within the business.
“The focus now is that the team will eventually be multi-skilled. They will be able to operate the laser and operate the press brakes, because the touch screens are very similar. We are going to change how the overall department works. We want people to be able to operate any of the machines so that the team leader is not hands-on all the time but can run the department – managing workflow and performance.
The skills issue also comes into play with the Easy-Form press brakes.
“Skills are not abundant in the labour market, so we are training people to operate that machinery from scratch – so the EasyForm angle measuring technology is a great help.
Automating the software process from 3D design to finished part was vital to be able to cope with the high product mix that was now required.
Mark explains: “If we sell 200 machines in a month there could be 160 variants. If a customer places an order for 80 units, it could be spread across eight different models with only be 25 of them the same.
“Dealers will sell multiples of the same machine in a year and once we have the design and it is in our system it is easy for us to just pull that design out, call off the laser patterns and make it. But every week we get new variants where we need to program a new part – and that is where the software automation comes in.”
On the production side, most of the material being processed is from 2.0 to 3.0mm, although the laser can cut up to 20mm. The cut 2D parts are then formed and welded to create the machine frame. Although it is thin material it is a very robust and strong product once it has been fabricated.
The accuracy of the EasyForm press brake ensures accurate fit up of the formed parts for welding.
As well as structural components, the laser cut nest will also include smaller parts such as legs, covers, brackets and so on.
“A lot of what we are manufacturing is for small components, but some of the machines we build are 10m long – the biggest we ever made was 25m long – so we use 3m sheets and bolt the fabricated sections together if we need to.”
Wombwell is LNS’s European manufacturing centre for swarf management equipment, with 60% of production destined for the UK and 40% for export to Europe. Other machine tool peripherals in the LNS portfolio, such as bar feeders and air filtration systems, are manufactured at sites in Switzerland and Italy.
Mark says that as COO for Europe he will be taking an overall view of manufacturing processes across the sites.
“The sheet metal work for the products manufactured in Italy and Switzerland is all subcontracted. One of the questions is whether we could bring that in-house.”
He adds that LNS in China also has an LVD laser with Compact Tower system and a LVD Robotic Dyna-cell installed and followed from the lead of the UK operation.
“We were the ones that started the LVD process – that’s where we wanted to go. We saw the power of what it could do for us. After I had been to Belgium, the person who runs the facility in China came over and went to LVD in Belgium and saw the opportunity.
“The factory in China manufactures all the LNS products including bar feeders, swarf conveyors and other machine tool peripherals. The sheet metalwork for all our various products is made in that one factory – so we can see the way it works across the portfolio. So have good models to work off for our other factories.”
Mark says that the bottom line is that the LVD technology is really giving LNS UK an advantage in the market.
“It puts us ahead of our competition in terms of lead time. We have two customers who we guarantee a 10-day turnaround from point of order to delivery. Our competition doesn’t offer that service and we have won all the work from a major UK supplier on that basis.”