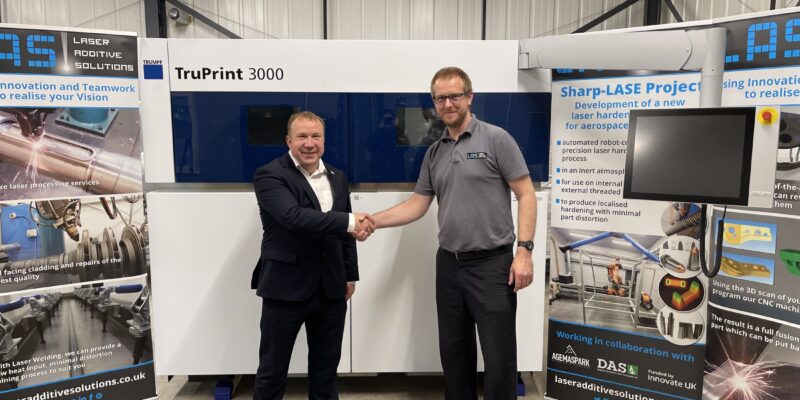
Doncaster-based Laser Additive Solutions (LAS), a rapidly expanding subcontract provider of laser processing and additive manufacturing services, is targeting customers in the UK’s burgeoning space sector following its investment in an advanced TruPrint 3000 additive production system from TRUMPF. If things go to plan, the machine could be the first of many metal 3D printers at this progressive manufacturing business.
Founded in 2015, the team at LAS has over 50 years of combined experience in precision laser repair, manufacture and joining processes. Customers include those operating in the general engineering, fusion energy, aerospace and military sectors, among others. ISO9001-accredited LAS also harbours close ties with a number of UK universities and research organisations.
“Our core expertise is LMD [laser metal deposition], although like most in the industry we’re now referring to this process as laser DED [direct energy deposition],” explains Managing Director Peter Brown. “We have two very good systems that undertake laser DED, both of which use TRUMPF lasers. While these machines can support our steady growth moving forward, to drive faster progress I felt we needed a complementary process, hence our interest in a powder-bed machine.”
LAS made enquires for a new TRUMPF TruPrint 1000, a compact metal 3D printer that is ideal for fast, cost-efficient, small-series production. However, the company’s application for a grant was unsuccessful so LAS put the project on hold. Then came a stroke of good fortune.
“TRUMPF alerted us to the availability of a quick delivery TruPrint 3000 machine, says Mr Brown. “Although the machine had been previously used, it had very low running hours, almost untouched. A powder-bed system had been in my thoughts for a number of years; this was clearly the opportune moment to make the leap.”
Another major driver of the investment was a surprise new contract secured by LAS involving a long-term production welding job on its laser DED machines. The company has had TRUMPF laser and welding systems on site since its formation in 2015.
“This work began generating extra revenue that we hadn’t expected, so we used some of that as a deposit on the TruPrint 3000,” he explains. Fortunately, LAS already has ample laser/metal-powder experience, so are not anticipating a huge learning curve.
“Our number one target for the TruPrint 3000 is the UK’s space sector,” states Mr Brown. “The space sector is constantly seeking manufacturing solutions for lightweight structures that are not easy to build with other technologies.”
A key material for many of these lightweight structures is high-strength aluminium. As it happens, the TruPrint 3000 is already set-up for this material.
“We’ll continue with this material initially, maybe introducing others at a later date,” says Mr Brown. “The TruPrint 3000 is the start of a journey for us, but we don’t expect it to be vastly different to how we work with our laser DED systems. We’re familiar with developing machine parameters for new components, performing trials and experimenting with different build techniques. We can also assist with design suggestions to suit additive manufacture and help minimise costs for customers.”
Another advantage that LAS sees with the addition of its TruPrint 3000, which is the first such model installed in the UK for job shop applications, is its ability to run 24/7, unmanned overnight and at the weekends.
“The machine is very production-oriented and, if we find the right jobs, I’m sure we can keep it running around the clock,” he says. “In 10 years’ time we could have multiples of these machines, potentially a unit filled with banks of them. Broadening our customer database into 3D metal printing may also lead to additional laser DED and laser welding opportunities.”
Business growth at LAS, which today occupies three industrial units, is presently robust, prompting the company to double its headcount in recent years. The future is also looking bright, with LAS currently bidding for what will be its biggest ever contract at a value in excess of £1 million.
“If we win, we’ll invest in another laser DED system and hire more people,” concludes Mr Brown. “We’re very heavy investors and plough everything back into the business. Obviously that can’t go on forever, but my ambition for now is to continue building our technological capability.”