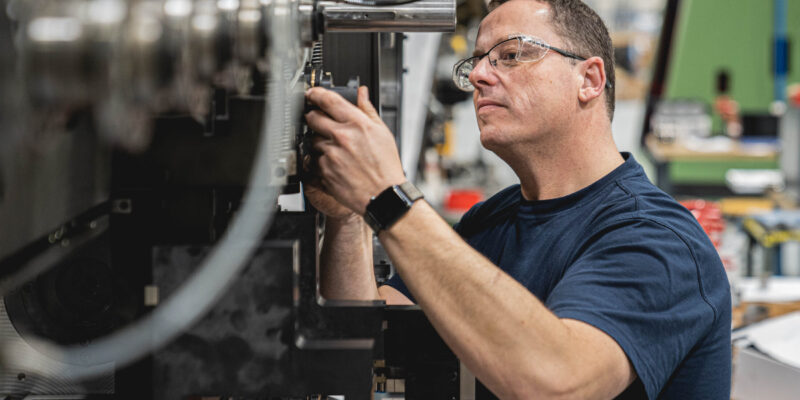
Inspections are essential and a quick and easy way to ensure the performance of a company’s in-house Bihler systems and avoid unscheduled downtimes. All the mechanical machine components are subjected to a thorough analysis and assessment, making it possible for users to act exactly as and when required, for example, by ordering spare parts in good time.
Bihler provides an inspection service for all Bihler systems, irrespective of whether they are mechanical or servo-controlled, older models or more recent designs. These are complete machine check-ups that offer many practical benefits to the customer: “Bihler’s inspections identify all the weaknesses and problems before the system fails and make sure they are eliminated in good time. Any spare parts that are needed can be purchased well in advance and the corresponding maintenance and service activities can be scheduled and conducted with minimum delay,” explains Martin Schön, Head of Technical Support. “All in all, this allows all our customers to manufacture much more efficiently.”
Comprehensive examination
Every inspection starts with the recording, analysis and assessment of the system’s key parts and components. “Experienced Bihler service engineers scrutinize every detail of the customer’s system and check all the parts for obvious anomalies or wear: From the drive and slide units, then on to the feed components, the press and the straightener, as well as the central lubrication system and the pneumatic and hydraulic components,” explains Peter Schmölz, Group Head of Mechanical
Engineering Service Technicians. “Particular attention is paid to the drive, which is a unit that is often underestimated by customers. It is particularly important to replace it in good time if the need arises because it is fundamental for machine operation and production.”
Valuable basis for decision-making
In the next step, the results of all the checks are recorded in a standardized inspection report. This also makes it possible to swap information with other Bihler service engineers, for example those responsible for performing the annual maintenance check-up. And the report naturally also gives the customer a detailed insight into their machine – and its future performance potential. “We recommend actions based on the inspection report, for example a follow-up repair or maintenance activity, a regular check-up in the form of a service agreement or a scheduled modernization,” says Schmölz. The particular benefit is that “the customer receives a separate inspection report and a separate spare parts offer for each individual machine. The corresponding spare parts delivery is then also clearly specified for each machine and delivered parts are unambiguously assigned to a specific system.” It is reassuring for customers to know that Bihler has adapted its parts stocks on the basis of the previously performed inspections and has a large number of typically needed spare parts on hand. When the corresponding repair or maintenance activities have been performed, the machine is again ready for its future tasks.
Worthwhile investment
The inspections, which take around three hours in the case of a mechanical machine, for example, are therefore an absolutely worthwhile investment: “The inspections always pay for themselves and are immensely important, in particular when we are dealing with critical machines that supply an entire line,” stresses Schön. “They can be performed with relatively little effort and, most importantly, are free from any time pressures and therefore bear no resemblance to an unscheduled machine stoppage which, as experience has shown, usually has a knock-on effect right through to the highest level.”