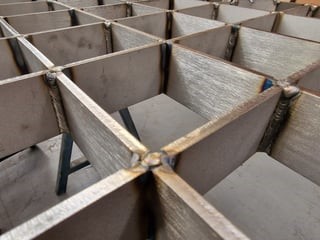
Alloy Fabrication involves the combination of two or more elements or materials to create a new material with improved properties. The specific processes involved in alloy fabrication can vary depending on factors such as the types of materials being combined, the desired properties of the resulting alloy, and the manufacturing methods used. However, there are several common processes and steps that are typically involved in alloy fabrication. Here are some of the key processes:
- Melting: The first step in alloy fabrication often involves melting the base metals or elements that will be used to create the alloy. This can be done using various methods, including electric arc furnaces, induction furnaces, or other high-temperature processes.
- Alloying: Alloying is the process of combining the molten base materials in precise proportions to achieve the desired alloy composition. This can be done by adding alloying elements, such as other metals or non-metallic elements, to the melt.
- Mixing and Homogenization: After alloying, it’s important to thoroughly mix the molten materials to ensure a uniform composition. Homogenization processes, such as stirring or agitation, help achieve this uniformity.
- Casting: The molten alloy is often cast into specific shapes, such as ingots, billets, or castings. Different casting methods, such as sand casting, die casting, or investment casting, can be used depending on the desired product and application.
Therser Wellman Fabrication services:
- Heat Treatment: Heat treatment processes may be employed to refine the microstructure of the alloy, improve its mechanical properties, and relieve stresses. Common heat treatment processes include annealing, quenching, tempering, and solution treatment.
- Forming and Machining: Depending on the final product requirements, the alloy may be further processed through various forming and machining techniques, such as rolling, forging, extrusion, or machining.
- Surface Treatment: Surface treatments like plating, coating, or polishing may be applied to enhance the alloy’s appearance, corrosion resistance, or other specific properties.
- Quality Control: Throughout the fabrication process, quality control measures are essential to ensure that the alloy meets the required specifications and standards. This includes testing for composition, mechanical properties, and defects.
- Final Product Assembly: In some cases, the alloy components may need to be assembled into larger structures or products. This can involve welding, soldering, or other joining techniques.
- Testing and Inspection: After fabrication is complete, rigorous testing and inspection are conducted to verify that the alloy meets the intended performance criteria and safety standards.
- Packaging and Shipping: The final alloy products are packaged and prepared for shipping to customers or for further processing in downstream industries.
It’s important to note that the specific processes and steps involved in alloy fabrication can vary widely depending on the type of alloy, its intended use, and the manufacturing facilities and equipment available.