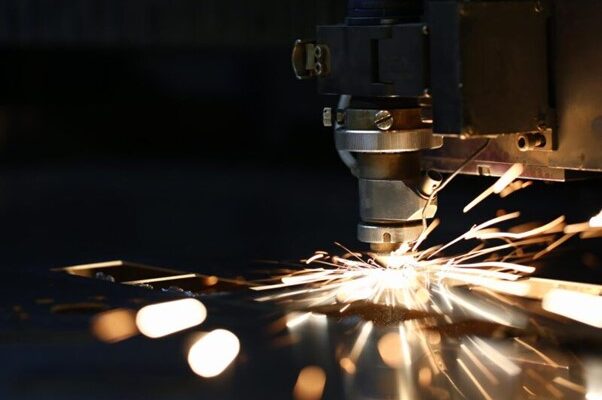
FROM RAW MATERIAL TO THE FINISHED PRODUCT
The journey of steel from raw materials to its various end products is a testament to human ingenuity and the relentless pursuit of innovation. This transformation involves steel fabrication – a meticulous process which has shaped our cities, industries, and daily lives.
RAW MATERIALS USED IN STEEL FABRICATION
The principal raw material for steel fabrication is iron ore. Coal is another significant raw material processed into coke to fuel blast furnaces. Limestone is also a flux to remove impurities during smelting.
These raw materials are sourced from large-scale mining operations spread across the globe. For instance, iron ore is extensively mined in countries like Australia, Brazil, and China. Coal and limestone, on the other hand, have a more widespread availability and are sourced from numerous countries worldwide.
THE PROCESS OF STEEL FABRICATION
The steel fabrication process is a multi-step procedure, which can be broken down into six principal phases:
- Design Phase: the process begins with the conceptualisation of the final product. This is achieved through Computer-Aided Design (CAD) software that enables precise blueprint creation.
- Cutting phase: once the design is finalised, the steel is cut into the required shapes and sizes. Depending on the project’s needs, this can be accomplished via laser, plasma, or sawing.
- Forming Phase: the cut pieces are then shaped into the desired forms. This involves processes like rolling and bending.
- Machining Phase: after forming, the steel might need further modifications like milling (removing excess material) or drilling (creating holes).
- Welding Phase: the individual components are then joined together using various welding techniques, depending on the design requirements.
- Assembly and Finishing Phase: the product is assembled, and finishing touches are added. This might include sandblasting to smoothen the surface, painting for aesthetic purposes, or coating for additional protection.
THE ROLE OF TECHNOLOGY IN STEEL FABRICATION
Technology has played a critical role in the steel fabrication process. It has increased efficiency, accuracy, and the overall quality of the final product.
Robotic automation has also found a place in steel fabrication, with robotic arms now capable of performing complex tasks like welding and assembly. These technologies increase productivity, ensure consistency, and reduce the margin for human error.
QUALITY CONTROL AND TESTING IN STEEL FABRICATION
Ensuring the highest quality and safety standards in steel fabrication is paramount. This is achieved through stringent quality control procedures and rigorous testing. Some of the common testing methods include visual inspection, ultrasonic testing, magnetic particle inspection, and tensile testing.
These tests help identify any defects or irregularities that might compromise the product’s quality or safety.
CONCLUSION
The journey of steel from simple iron ore to a functional, sturdy, and reliable product is truly fascinating. Each stage of the process, from sourcing raw materials to the final assembly, is critical to achieving the desired end product.
Technological advances continue to refine this process, ensuring that steel remains an indispensable part of our modern world.
HIGH-QUALITY STEEL FROM EXPERT FABRICATORS
Baker Steel Trading’s expert steel fabricators have a track record of providing excellent quality steel to clients from our workshop in Woking.
Whether building a small residential home or a large commercial building, structural steel is a versatile and reliable option that can help you achieve your construction goals. So if you’re looking for a cost-effective solution that won’t compromise on quality, consider using structural steel for your next construction project.